Extrusora
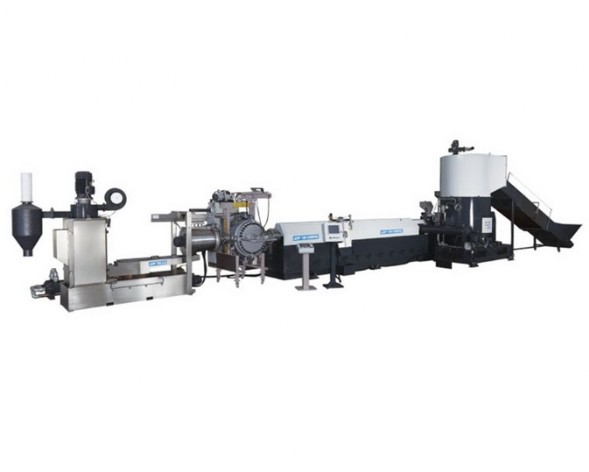
EXTRUSORA TORNILLO SIMPLE
EXTRUSORA TORNILLO SIMPLE
Las tecnologías de Delco srl hacen de la extrusora una máquina fácil de usar y flexible en la producción.
- alta especialización para cada tipo de aplicación
- alto rendimiento para cada producción
- minimización de los costes de mantenimiento
- larga duración
Nuestra gama de monotornillos se compone de:
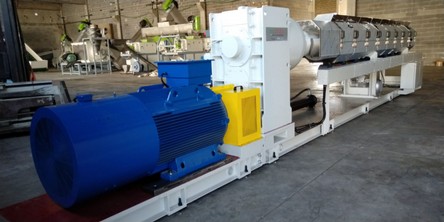
MD35
MD 60
MD 85
MD 105
MD 130
MD 180
MD 200
MD 250
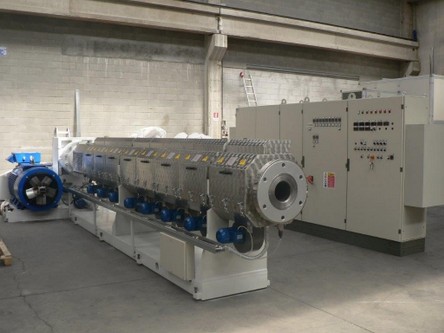
EXTRUSORA TORNILLO SIMPLE 130
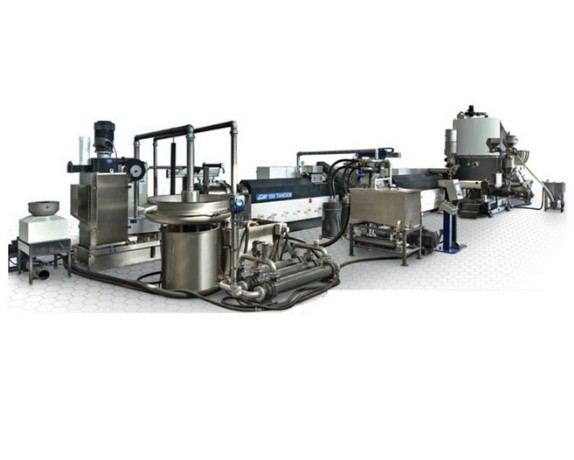
Tecnología TANDEM
La tecnología TANDEM aplicada al reciclaje de plásticos altamente impresos, contaminados y húmedos garantiza una excelente calidad del gránulo con un considerable ahorro energético con respecto a los sistemas de reciclaje tradicionales que efectúan una segunda extrusión del material.
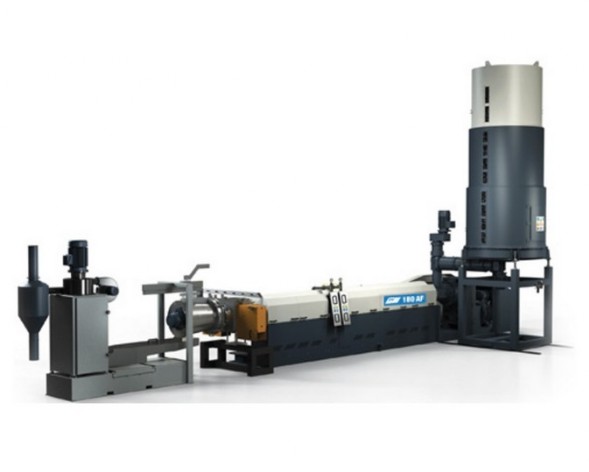
Líneas de regeneración tradicionales
Las líneas de regeneración tradicionales son ideales para reciclar materiales plásticos que requieren el uso de un molino. Pueden contar con un sistema de ALIMENTACIÓN FORZADA y un silo de almacenamiento, y estar disponibles con uno o dos sinfines, para materiales molidos, duros, en películas o escamas.
Extrusoras de doble husillo
Extrusoras de doble husillo
Con tecnología italiana y componentes electrónicos Siemens, diseñamos y construimos extrusoras de doble husillo co-rotativas y líneas completas para la producción de masterbatches y compuestos en los más variados sectores de uso. Más informaciones ➠
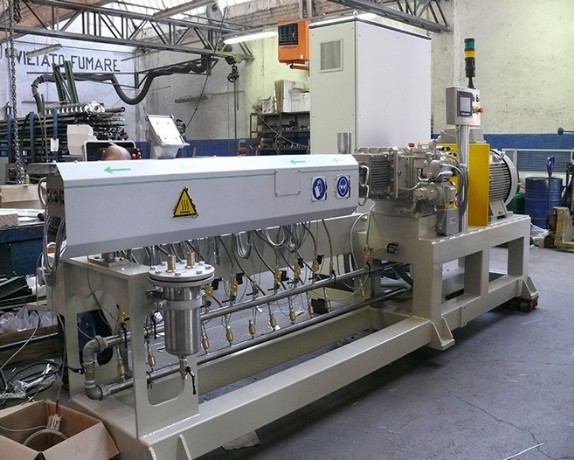
Extrusión de polímero
Los polímeros rara vez se usan solos sin composición. La composición, como se usa aquí, se refiere a mezclar en estado fundido los componentes de la mezcla y preparar un compuesto terminado a partir de todos los componentes de la mezcla. Los ingredientes de la composición son de diferentes tipos, cada uno con una función diferente para mejorar el rendimiento del polímero Además de los ingredientes mencionados anteriormente, una gran cantidad de polímeros se utilizan como mezclas con otros polímeros. Comercialmente, en el sector de materiales de polímeros, mezclas de polímeros juegan un papel muy importante. Estas mezclas representan una cantidad muy significativa de uso de polímeros y son uno de los sectores de mayor crecimiento en el campo de los polímeros. Esto es evidente en la literatura de patentes, donde cada año se emiten numerosas patentes relacionadas con mezclas de polímeros. La literatura técnica sobre temas relacionados con mezclas de polímeros, que incluyen composición de la materia, preparación, procesamiento, propiedades, aplicaciones, morfología, aspectos teóricos, etc., se está expandiendo a un ritmo aún más rápido. La combinación de polímeros existentes ofrece la posibilidad de crear un compuesto que tenga las propiedades deseadas de los componentes poliméricos individuales.
Líneas de composición por extrusión
Las líneas de composición vienen en muchas formas y tamaños. La composición se puede realizar en extrusoras de un solo tornillo, extrusoras de doble tornillo, mezcladores de un solo tornillo alternativos, mezcladores internos por lotes y mezcladores internos continuos. La configuración de la línea está determinada, entre otras cosas, por los ingredientes que se van a combinar en la extrusora de composición. El equipo aguas abajo generalmente consiste en un sistema de peletización. Los componentes poliméricos generalmente se agregan a través del primer puerto de alimentación. Los rellenos a menudo se agregan a un puerto de alimentación aguas abajo en un punto donde el plástico ya se ha derretido; esta disposición reduce el desgaste de la extrusora que podría ser causado por el relleno. Con frecuencia, una embutidora de doble tornillo agrega altos niveles de relleno, particularmente cuando el relleno tiene una densidad aparente baja. Con altos niveles de relleno, a menudo hay una cantidad sustancial de aire arrastrado; esto se elimina a través del puerto de ventilación. El puerto de ventilación suele estar conectado a una bomba de vacío; un alto nivel de vacío mejora la eliminación de volátiles del plástico. Algunas granuladoras cortan hebras extruidas enfriadas en un baño de agua; estos se denominan granuladores de hebras. Las cortadoras de cubos cortan láminas extruidas en lugar de hebras. Los gránulos de una cortadora de cubitos tienen una forma cúbica u octaédrica uniforme. Otras granuladoras cortan el material justo a la salida de la matriz; estos se denominan granuladores de cara de troquel. Estos sistemas de corte pueden ser granuladores de cara de matriz seca, granuladores de anillo de agua y granuladores bajo agua. En las granuladoras de cara de matriz seca, el plástico fundido se corta en la cara de matriz. Los gránulos se lanzan lejos de la cara del troquel mediante el movimiento rápido de las cuchillas de corte, generalmente en una suspensión de agua. En las granuladoras de anillo de agua, la acción centrífuga del cortador arroja los gránulos a una jaula de agua de caracol que gira alrededor del perímetro de la carcasa del cortador. La lechada fluye a un secador centrífugo. En las granuladoras submarinas, el plástico fundido se extruye directamente en agua y se corta inmediatamente con un cortador de múltiples cuchillas. Es posible que el troquel necesite una capacidad de calentamiento especial para evitar que la placa del troquel se congele. El procedimiento de puesta en marcha de las granuladoras submarinas a menudo requiere una secuencia cuidadosa del flujo de plástico, la rotación del cortador y el caudal de agua de entrada para evitar la congelación o aglomeración de la matriz. Las extrusoras de composición también se pueden combinar con sistemas de conformado directo aguas abajo. En muchos casos, se coloca una bomba de engranajes en el extremo de descarga de la extrusora para generar la presión del cabezal y controlar el rendimiento. El plástico se introduce en el primer puerto de alimentación de la extrusora de combinación, el relleno se introduce en el segundo puerto de alimentación y los volátiles y el aire atrapado se eliminan del puerto de ventilación. Se coloca una bomba de engranajes entre la extrusora de composición y la matriz de láminas. La hoja se alimenta a una pila de rollos y desde allí se manipula como en una línea de hoja normal, como se discutió anteriormente.
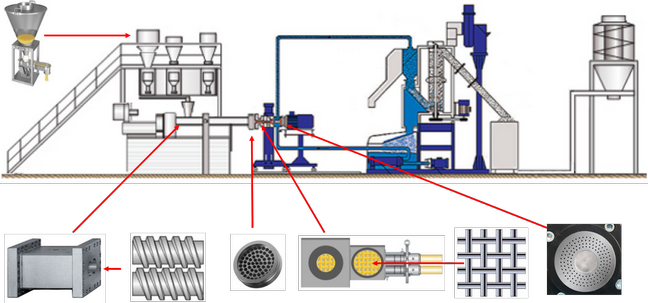
Proceso de extrusión
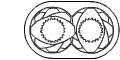
Compound
Compounding describe todos los pasos necesarios que deben tomarse antes de que el material polimérico se procese en el producto terminado. Dichos pasos incluyen la adición de aditivos como tintes y pigmentos, rellenos y refuerzos, plastificantes, lubricantes, estabilizadores, retardantes de llama, agentes espumantes, solventes u otros polímeros, o la transformación del material en una forma adecuada para su posterior procesamiento (polvo, pasta o pellets). Las operaciones de preparación de material más importantes son mezclar, dispersar, amasar, disolver, granular o granular, y secar.
Procesos de mezclado
Las propiedades del producto terminado en casi todos los procesos de polímeros dependen en parte de qué tan bien se mezcló el material, y todos los métodos de procesamiento incluyen una etapa de mezcla de los materiales base. Por ejemplo, una parte integral de una extrusora de tornillo es una zona de mezcla. De hecho, la mayoría de las extrusoras de doble tornillo se utilizan principalmente como mezcla dispositivos. Por lo tanto, una mejor comprensión del proceso de mezcla ayuda a optimizar las condiciones de procesamiento y a aumentar la calidad de las piezas. El proceso de mezcla o mezcla de polímeros se logra mediante la distribución o dispersión de un componente secundario o secundario dentro de un componente principal que sirve como matriz. El componente principal puede considerarse como la fase continua y los componentes menores como fases distribuidas o dispersas en forma de gotas, filamentos o aglomerados. Al crear una mezcla de polímeros, siempre se debe tener en cuenta que la mezcla probablemente se volverá a fundir en procesos posteriores de procesamiento o conformación. La coalescencia puede comprometer la estructura finamente dispersa creada durante la composición al causar la separación de fases. Para evitar este problema, son comunes los compatibilizadores, que son macromoléculas utilizadas para garantizar la compatibilidad en las capas límite entre las dos fases.
Tolva
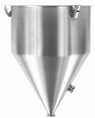
Husillo o tornillo
Extrusores Contra-rotantes No Entrelazados
Los extrusores contra-rotantes no están en contacto íntimo, siendo por esta razón excelentes en los casos donde sólo requiere un mezclado distributivo, es decir, que no requiera de una reducción del tamaño de los aditivos agregados. También se usan en desvolatilización de altas producciones.
Extrusores Co-rotantes Entrelazados
Estos extrusores se prefieren para compounding en volúmenes mayores. Entre los husillos existe solo una pequeña separación, forzando con esto al plástico a circular por la periferia de los husillos, generando un patrón de forma de "8". Por esta pequeña separación se crea un efecto de "auto-limpieza” de la superficie del otro.

Barril o Cañón:
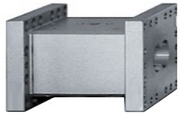
Keywords: plasticos de ingenieria, distribuidor definitive innovation en mexico, definitive innovation en mexico, distribuidor gamma meccanica en mexico, gamma meccanica en mexico, distribuidor tsa industriale en mexico, tsa industriale en mexico, maquinaria para plastico, maquinaria para polimeros, maquinarias italianas, proyectos para la industria, proyectos para plasticos, proyectos de ingenieria, polymer machinery, silos para industria plastica, extrusoras para industria plastica, dosificadores para industria plastica, transportadores para industria plastica, transportadores para industria plastica, proyectos con maquinarias italianas, las mejores maquinarias italianas, maquinaria italiana en mexico, proyectos para industria plastica en mexico, maquinarias italianas en mexico, maquinaria, extrusoras, silos, dosificacion, transportador, maquinaria, polimeros, italiana, proyectos, cargadores, transportador.