Agente espumante
Aditivos > ► B-C-D-E-F
Agentes Espumantes
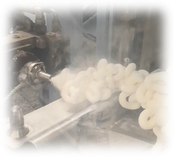
Hay dos grupos principales de agentes de expansión, que difieren sustancialmente según su mecanismo de reacción:
- endotérmico (consumo de calor)
- agentes de expansión exotérmicos (liberación de calor)
Los agentes de expansión se utilizan principalmente para reducir la densidad, lo que conduce a una reducción en el peso del producto final y una reducción en los costos. Las características adicionales o mejoradas del producto son otra ventaja del uso de agentes de soplado químicos.
Algunas ventajas son:
- Mejora en el aislamiento térmico y acústico
- Mejora de propiedades dieléctricas
- Mejora de las propiedades de amortización
- Evita la formación de depresiones en la superficie durante el moldeo por inyección
- Efectos decorativos
Agentes de expansión endotérmicos
Cuando se agrega calor, estos agentes de soplado se descomponen y generan gases neutros en el medio ambiente. A menudo estos gases son dióxido de carbono y vapor de agua; los ingredientes activos más conocidos son carbonatos y ácidos carboxílicos. Como el calor se consume para iniciar y propagar la reacción, las sustancias se denominan agentes de expansión endotérmicos. Su ventaja radica en el hecho de que cuando se interrumpe el suministro de calor, la producción de gas se detiene y se reanuda si se suministra más calor. Como resultado, los agentes de expansión endotérmicos son fáciles de manejar durante el procesamiento. Muchos de los agentes de expansión endotérmicos que empleamos están aprobados para su uso con alimentos y, por lo tanto, pueden incluirse en muchas soluciones de envasado.
Agentes exotérmicos
Después de un proceso de iniciación con radiación, calor u otras formas de energía, los agentes de hinchazón exotérmicos al descomponerse liberan calor y gases como nitrógeno, dióxido de carbono y amoníaco. La reacción de descomposición continúa entonces autónomamente debido al calor liberado y no puede ser interrumpida por simples medidas de enfriamiento. En contraste con los agentes de expansión endotérmicos, se pueden lograr rendimientos de gas significativamente mayores con agentes de expansión exotérmicos. Al usar aditivos adicionales, podemos influir en la energía inicial y, por lo tanto, en la temperatura de descomposición inicial.
Propiedades
Los agentes de expansión favorecen la disminución de la densidad para hacer que los productos terminados sean más livianos. Los expansores también mejoran los fenómenos de retrolavado y llenado del molde. El retrolavado es un fenómeno que ocurre durante la fase de moldeo y causa el llenado incompleto del molde; como consecuencia, el artículo impreso aparece "vacío". Para resolver este tipo de problemas, se utilizan agentes de expansión que, al liberar gas dentro del molde, comprimen el material fundido, favoreciendo el llenado del mismo de manera homogénea. El uso de estos maestros reduce las características mecánicas del producto.
Posibles problemas de proceso
El manejo inadecuado de la temperatura puede provocar el reflujo del material durante la extrusión o el moldeo, con la posible formación de gas. El porcentaje y las temperaturas de uso se establecerán en la máquina y en el proceso involucrado.
Gama productos
Nuestra experiencia en tecnologías de proceso nos convierte en uno de los principales proveedores de agentes en expansión. Esto se debe a que los agentes en expansión tienen un gran compromiso con el desarrollo y la producción debido a su tendencia latente a descomponerse cuando no se manipulan adecuadamente en forma de polvo. Nuestras soluciones de agentes de expansión exotérmica y / o endotérmica pueden prepararse individualmente para satisfacer cualquier deseo de modificación. Además de las combinaciones de agentes de expansión exotérmicos y endotérmicos, también podemos proporcionar agentes de expansión química como agentes nucleantes para la expansión física y química. Si se requieren expansiones muy finas y regulares, un agente nucleante es la mejor solución.
- ADC azodicarbonamida
- ADC azodicarbonamida Activada
- 5-PT 5-Phenyltetrazole
- OBSH 4,4'-Oxidi(bencenosulfonohidracida)
- TSH P-Tolueno Sulfonil Hidrazida
- (Blowing agent)Sodium bicarbonate(citric acid)
Agentes de soplado físicos
Los agentes de soplado físicos tienen un costo relativamente bajo y no dejan residuos sólidos, pero su uso requiere un equipo especial. No son reactivos en el sentido químico, y pueden consistir en líquidos volátiles (orgánicos o inorgánicos, por ejemplo, agua) o en gases comprimidos, como dióxido de carbono o nitrógeno, que se disuelven bajo presión en el polímero para formar una espuma. cuando se libera la presión. Los agentes de expansión físicos generalmente disminuyen la viscosidad de la mezcla de reacción si está presente en cantidades apreciables. La solubilidad de un gas en un polímero depende en gran medida de la presión y la temperatura. Cuando cae la presión, el gas se vuelve mucho menos soluble y se produce una separación de fases, con el gas formando células. El proceso de evaporación contrarresta el calor producido por el proceso de polimerización exotérmica. La aplicación más importante de la tecnología de gas comprimido es probablemente la formación de productos espumados durante el moldeo por inyección de termoplásticos. Cuando el agente de expansión es sólido o líquido, la cantidad de agente de expansión utilizada varía de menos del 1% hasta aproximadamente el 15%, dependiendo de las circunstancias.
Agentes de soplado líquidos
Una gama de clorofluorocarbonos (CFC) solía emplearse con éxito en espumas rígidas de poliuretano; no solo generaron una estructura de espuma, sino que también mejoraron las propiedades finales. En los últimos años, sin embargo, se ha producido un rápido alejamiento de los CFC debido al problema de la capa de ozono. Suecia prohibió los CFC en 1991, seguido de Suiza, EE. UU., Etc., y ahora está prohibido el uso de CFC. Los hidroclorofluorocarbonos (HCFC) se han adoptado ampliamente, aunque todavía tienen un grado finito de potencial de agotamiento del ozono (ODP), típicamente en el rango de cero a 0.05, en comparación con los CFC típicamente en el rango de 0.2 a 1. Hidrofluorocarbonos (HFC) como el hexafluorobutano También se están utilizando en el momento de la redacción de este documento, pero se están aplicando más restricciones sobre la elección de sustancias disponibles, lo que resulta en la eliminación de muchos otros productos químicos en los próximos años. Por otro lado, la lista de sustancias prohibidas puede podarse ocasionalmente; La acetona se retiró de una lista de agentes de soplado regulados por la Agencia de Protección Ambiental de EE. UU., y se demostró que tiene poco o ningún impacto en los problemas de smog y ozono. Cuando se sustituye un nuevo agente de expansión por uno que se ha retirado, las propiedades físicas del producto terminado se alterarán, y se pueden invocar aditivos como tensioactivos y agentes suavizantes para modificar propiedades como las características de aislamiento. El cloruro de metileno se usa ampliamente como agente de soplado físico. Al igual que con muchos otros agentes, ha habido problemas para lograr la velocidad de volatilización correcta, pero tiene la gran ventaja de que no es inflamable, a diferencia de los agentes de soplado de hidrocarburos alifáticos. Tiene una de las conductividades térmicas más bajas, a 0.0063 W / m / K, en comparación con 0.0259 W / m / K para aire y 0.0168 W / m / K para dióxido de carbono, impartiendo así mejores calidades de aislamiento a la espuma. (Cuando las celdas de una espuma son de la variedad cerrada, retienen gran parte del agente de expansión original, y esto contribuye significativamente a las características de aislamiento de la espuma). El pentano, el cidopentano y el isopentano normales han demostrado ser útiles, bajos costo, agentes de soplado físicos fácilmente disponibles, dando espumas con buenas propiedades térmicas. Sin embargo, los pentanos forman mezclas potencialmente explosivas con el aire. Esto significa que los procesos de fabricación deben modificarse para hacer frente a los riesgos, un factor que ha limitado su atractivo.
Agentes de soplado químicos
Los agentes de soplado químicos producen gases por una reacción química que ocurre al mismo tiempo y en el mismo rango de temperatura que la operación de procesamiento. La mayoría de los agentes de expansión químicos son líquidos y las reacciones de descomposición son usualmente pero no invariablemente exotérmicas. Los agentes de soplado químicos son preferidos para la producción de espuma de PVC. Es esencial que cualquiera que sea la reacción de producción de gas, ocurra dentro del rango de temperatura de la operación de procesamiento de plásticos. En algunas circunstancias, esto significa agregar una segunda sustancia química como "pateador" para reducir la temperatura de descomposición del agente de expansión principal. (...) también pueden ser, por cierto, como pateadores. El producto final de una reacción de descomposición del agente de expansión se altera significativamente por la inclusión de los pateadores, y pueden promover en exceso la descomposición del agente de soplado, lo que lleva a la necesidad de amortiguar la reacción del pateador con modificadores adecuados, como ácidos dicarboxílicos o anhídridos. Los agentes de expansión químicos más importantes son los compuestos azoicos, como la azodicarbonamida (AZDC) y el azoisobutironitrilo. El azoisobutironitrilo se descompone al calentarse, para producir radicales libres y gas nitrógeno, dióxido de carbono y amoníaco. Otros agentes de expansión químicos incluyen derivados de hidrazina, semicarbazidas, tetrazoles, benzoxazinas y sustancias inorgánicas como el bicarbonato de sodio junto con ácido cítrico. Sistemas mixtos inorgánicos y orgánicos, p. los que involucran también se han utilizado 1,1azobisformamida y bicarbonato de sodio. En general, los agentes de expansión químicos orgánicos ofrecen un mejor control que los inorgánicos. Pero el número de factores que deben tenerse en cuenta es grande: la toxicidad; el efecto sobre el color y la durabilidad del molde; la volatilidad de cualquier agente de soplado residual, y la posibilidad de efectos adversos sobre el rendimiento del fuego del polímero o su estabilidad térmica o fotooxidativa. La facilidad de adición a la mezcla de polímeros es un problema práctico. Los agentes de expansión químicos se pueden agregar directamente como polvo, como gránulos sólidos o como líquidos concentrados, pero necesitan una medición precisa.
Agentes de soplado químico (CBA)
Los agentes de soplado químicos generan un gas, típicamente nitrógeno, agua, monóxido de carbono o dióxido de carbono, mediante una reacción química que puede ser exotérmica (es decir, el sistema genera químicamente calor y lo libera el sistema, lo que resulta en un aumento de la temperatura) o endotérmico (El sistema absorbe el calor). El amoníaco se puede formar con ciertos agentes de expansión, pero esto puede tener desventajas, ya que conduce a la degradación del policarbonato. La temperatura a la que se generan los gases debe ser coherente con la ventana de temperatura de procesamiento para el polímero utilizado. La reacción de descomposición no debe ser autocatalítica, de lo contrario se acelera, causando sobrecalentamiento. El agente de expansión debe ser lo suficientemente compatible como para no separarse del polímero.
La azodicarbonamida (AZC) es, con el CBA el más utilizado. Este compuesto fue sugerido como un agente espumante para plásticos en Alemania durante los años '50, siendo hoy en día uno de los agentes espumantes más utilizado del mercado. La azodicarbonamida (ADC) se prepara haciendo reaccionar la hidrazina con la uréa, bajo condiciones controladas, para producir el intermedio hidrazodicarbonamida, la cual se oxida a azodicarbonamida. Oxidantes efectivos son los dicromatos, nitratos, dióxido de hidrógeno, cloro, etc. La ADC es un compuesto cristalino sólido, de color amarillo que descompone produciendo una gran cantidad de gas (220-240 cm3 /g). Al contrario que otros agentes espumantes, la azodicarbonamida no soporta la combustión y se autoextingue, siendo su descomposición no-tóxica y no-decoloranteò. Las reacciones involucradas en la descomposición térmica de la azodicarbonamida son complejas y dependen de la velocidad de calefacción y del entorno en el que transcurre la descomposición. Es generalmente aceptado, que en primer lugar se produce una descomposición primaria mediante las reacciones con una reacción secundaria que tiene lugar a partir de la generación del ácido isociánico (HNCO) por parte de las dos reacciones primarias i e ii. El ácido isociánico puede tomar parte en otras reacciones secundarias para dar lugar a unos productos sólidos de descomposición, o puede reaccionar con trazas de mezcla para dar dióxido de carbono y amoniaco. Otros mecanismos de descomposición menos aceptados indican la producción de biurea (H2NCONHCONH2) como un componente de los residuos sólidos. La composición de los gases varía con la temperatura de descomposición y el entorno, pero normalmente estos gases están compuestos de un 62 % de N2, un 35 % de CO y un 3 % de otros componentes (entre los que se incluye al amoniaco). El rendimiento total de gas representa entre un 32 y un 34 % del peso de la azodicarbonamida. La descomposición y la consecuente generación de gas a partir de la azodicarbonamida en un ensayo de descomposición térmica es función tanto del tiempo como de la temperatura. Así, en un ensayo isotermo, tanto la velocidad de descomposición como el volumen de gas generado aumentan a medida que se aumenta la temperatura. Puede espumar el PVC, incluido el PVC plastificado, así como las poliolefinas, los estirénicos, las poliamidas, el PPO y algunos elastómeros termoplásticos. AZC se descompone exotérmicamente a alrededor de 210°C para dar nitrógeno gas, junto con otros productos de degradación como urea, ácido cianúrico y ciamelida como subproductos sólidos. También se puede formar monóxido de carbono y ácido isocianúrico, y si la descomposición la temperatura es lo suficientemente alta, el amoníaco puede ser detectable. La temperatura a la cual la azodicarbonamida descompone puede ser reducida desde los 200-220°C hasta los 170-190°C, e incluso a temperaturas más bajas, mediante la adición de activadores. Los activadores más efectivos incluyen compuestos de metales de transición, aminas, amidas y glicoles. Por ejemplo, los compuestos que contienen Zn, Cd y Pb son activadores que se utilizan generalmente en forma de óxidos, sales (normalmente de un ácido graso, por ejemplo, estearatos) u otros compuestos organometálicos. De estos compuestos metálicos, aquellos que están basados en Cd o Pb, son más efectivos que los compuestos de Zn, cuando la descomposición tiene lugar en el rango de temperaturas de 160-180°C, mientras que los compuestos de Zn son más efectivos a partir de 180°C. La temperaturas más bajas de descomposición producen una reducción en la cantidad de gas generada y, consecuentemente, los activadores que contienen Zn proporcionan sólo 190 cm3 /g; por otro lado, los activadores de Pb pueden reducir el rendimiento de gas hasta 160 cm3 /g.
El bicarbonato de sodio, con o sin ácido cítrico, es un agente de expansión que se descompone endotérmicamente a 150-230°C. Es adecuado para poliestireno, ABS, poliamidas, poliolefinas y PVC rígido, pero no para PVC plastificado. Los gases desprendidos incluyen dióxido de carbono y agua, por lo que puede haber un problema de oxidación con los moldes de metal. El tipo de espuma obtenida con bicarbonato de sodio generalmente tiene una estructura gruesa, aunque las pruebas con productos de diferentes fabricantes, todos con bicarbonato / ácido cítrico como ingrediente activo, muestran diferencias considerables en la densidad celular y de espuma.
El derivado de hidrazina 4, 4´-oxi-bis (bencenosulfonilhidrazida) o OBSH se descompone exotérmicamente a 150°C y se utiliza para hacer aislamiento de cables y alambres espumados.
Para-tolueno sulfonil semicarbazida (TSSC) es estable hasta aproximadamente 230°C, cuando comienza a emitir nitrógeno y agua. (En la práctica, la descomposición puede comenzar antes, dependiendo de la influencia del resto de la mezcla). TSSC se usa en estirénicos, poliolefinas, PVC rígido y poliamidas también se usan tetrazoles como el 5-fenil tetrazol, que genera nitrógeno, y compuestos nitrosos de bajo costo como el dinitrosopentametilen tetramina.
Azobis(isobutironitrilo). Este compuesto fue descubierto como agente de espumación en Alemania, se obtenie a partir de hidracina, acetona, cianuro sódico y medio ácido, usando cloro para oxidar el compuesto intermedio (hidrazo bis(isobutironitrilo)) y fue introducido para la producción de artículos de caucho esponjosos, aunque más tarde fue recomendado para el PVC expandido. Este compuesto es no decolorante y proporciona al PVC una estructura celular uniforme. La descomposición del azobis(isobutironitrilo) ocurre rápidamente a temperaturas por encima de los 100°C y más lentamente a temperaturas inferiores. La completa descomposición proporciona 137 mL de gas por gramo (medido en condiciones normales). El residuo de la descomposición (tetrametilsucciononitrilo) es una sustancia tóxica y se deben tomar medidas de precaución para eliminarla. No se recomienda este producto para su uso en Estados Unidos, pero en Europa si se utiliza en el PVC expandido, siempre y cuando las condiciones de ventilación sean las adecuadas.
Dinitrosopentametilentetramina. Este compuesto se prepara mediante la nitrosación de la heximetilentetramina (producto de la reacción del formaldahído y amoniaco). Este producto, cuando se calienta solo o en presencia de diluyentes inertes, descompone cerca de los 200°C; pero cuando se utiliza en cauchos o plásticos en presencia de ciertos activadores, puede producir gases en el rango de temperaturas entre 130 y 195°C. La cantidad de gas producida a partir de material no diluído está cerca de los 2 moles por mol de agente espumante (cerca de 265 mL/g medido en condiciones normales). Los productos de descomposición de este compuesto todavía no han sido totalmente dilucidados, pero se ha descubierto que se produce nitrógeno y formaldehido. La temperatura de descomposición de este agente espumante puede ser substancialmente reducida y acelerada mediante la adición de sustancias ácidas, tales como el ácido salicílico y el anhídrido ftálico. La dinitrosopentametilentetramina se utiliza en cauchos pero no mucho en plásticos, debido al olor que deja el residuo, siendo este agente espumante no decolorante.
Bencenosulfonilhidrazida. La bencenosulfonilhidrazida es el compuesto aromático más simple dentro de la clase de las sulfonilhidrazidas. Se prepara a partir del cloruro de sulfonilbenceno con hidrazina en presencia de una base (i.e., amoniaco). El producto es un sólido cristalino blanco que funde y empieza a descomponer cerca de los 105°C. Desafortunadamente, el olor residual es fuerte y desagradable, debido a las reminiscencias de tiofenol o de disulfuro de difenilo. La descomposición implica una oxidación-reducción interna del grupo sulfonilhidrazida. Un mecanismo posible para la descomposición, donde el intermedio hipotético, el ácido bencenosulfénico, aparentemente es incapaz de existir, e inmediatamente reacciona para dar difenil disulfuro y fenil bencenotiosulfonato. El fuerte olor de este compuesto cuando reacciona en PVC, desaparece cuando se utiliza en cauchos expandidos debido a que los residuos que contienen sulfuro reaccionan con el caucho, dejando una combinación inodora.
p-Toluensulfonilhidrazida. El comportamiento general de la p-toluensulfonilhidrazida es similar a la bencenosulfonilhidrazina (incluidos los mecanismos de descomposición y olores), excepto que el punto de fusión y de descomposición son superiores (por encima de 120°C). La descomposición de la p-toluensulfonilhidrazida, cuando aislaron el ditolil disulfuro y el p-tolil ptoluentiosulfonato como productos principales de descomposición.
p,p’-oxibis(bencensulfonilhidrazida). Este agente espumante no presenta el olor cuando se aplica en plásticos. Se prepara por clorosulfonación del difenileter con ácido clorosulfónico y la subsecuente reacción con hidrazina en presencia de una base. El producto es un sólido cristalino blanco que funde descomponiendo a 164°C (e incluso a temperaturas menores), en presencia de cauchos o plásticos. La descomposición de la p,p’-oxibis(bencensulfonilhidrazina) se produce igual que lo hace la bencensulfonilhidrazina, proporcionado 125 cm3/g de gases, proporcionando un residuo casi sin olor. Este agente se usa ampliamente en la industria del caucho y del plástico, y más concretamente en la extrusión de PE para el aislamiento de cables, en la expansión de plastisoles de PVC, en resinas fenólicas y epoxi, en cauchos expandidos y en mezclas de caucho-resina.
Espumas de soplado: agentes químicos versus agentes físicos
No todos los tipos y grados de polímeros se espuman fácilmente o con las mismas cualidades de tamaños y estructuras de celda soplada. Esta variabilidad es una ventaja en cierto modo, ya que permite soplar diferentes tipos de espumas poliméricas para diferentes propósitos. Las espumas de tipo esponja de Opencell son útiles en aplicaciones de absorción de impactos, por ejemplo, mientras que una estructura de celda de espuma cerrada es eficaz para el aislamiento de tuberías y cables, por ejemplo. Las poliolefinas amorfas, altamente ramificadas y de alta resistencia a la fusión, son generalmente más fáciles de espumar que las poliolefinas cristalinas de alto flujo. El LDPE, en particular, puede espumarse para reducir la densidad a niveles extremadamente bajos con reducciones de 0,92 g / cc para LDPE sin espuma a 0,03 g / cc en extrusiones altamente espumadas. Estas espumas ligeras proporcionan aislamiento térmico y acústico, amortiguación de impactos y flotabilidad del agua para envases de protección, productos de construcción y productos de consumo. A menudo, los materiales de polietileno (PE) espumado se entrecruzan con agentes de peróxido o tratamientos con haz de electrones para aumentar su resistencia. Las espumas más densas y rígidas hechas de poliolefinas más rígidas ofrecen resistencia y rigidez en piezas gruesas pero de bajo peso. Sin embargo, el polipropileno cristalino (PP) puede ser más difícil de espumar porque la nucleación y formación de sus regiones cristalinas se produce al mismo tiempo que la nucleación de la célula soplada. Esto inhibe la formación de células y hace que la elección de los aditivos espumantes y las condiciones del proceso sean críticas. Los agentes espumantes o espumantes (materiales que provocan la formación de espuma en un plástico) se pueden agregar al polímero como aditivo interno (agentes espumantes químicos (CFA)) o inyectarse como gases o líquidos volátiles durante el procesamiento de la masa fundida con equipo especial (agentes espumantes físicos). Ambos tipos de agentes crean y expanden burbujas a lo largo de la matriz del polímero formando una red celular interna de células abiertas o cerradas. Los agentes químicos se descomponen por el calor del procesamiento en gases que nuclean y expanden las células, mientras que los procesos físicos de formación de espuma expanden las células utilizando la energía o el cambio de fase del agente inyectado.
Keywords: Agente de Expansión, Agente Espumante
Espuma en el moldeo rotacional
Dadas las grandes dimensiones de muchas piezas rotomoldeadas, no es sorprendente que la espuma se utilice para reducir la masa de las piezas y el consumo de materia prima. Al ofrecer relaciones más altas de rigidez a peso, la espuma puede permitir futuras oportunidades de crecimiento potencial en este sector. Por ejemplo, se dice que mejores agentes espumantes hacen que el PE espumado rotomoldeado sea más competitivo con las espumas de poliuretano de dos componentes. Además, las piezas rotomoldeadas a menudo no siempre necesitan satisfacer los altos requisitos de propiedades de ingeniería de las aplicaciones técnicas; por lo tanto, los efectos negativos de la espuma en estas propiedades pueden no ser una limitación. Los rotomoldeadores han utilizado ADCA en forma de polvo en sus formulaciones para crear productos espumados. Sin embargo, los masterbatches de micropellet se han vuelto más populares y ofrecen una calidad de espuma mejorada. Como en otros procesos, el control del proceso es importante en las espumas de rotomoldeo, ya que la descomposición prematura del agente espumante puede resultar en un escape de gas entre las partículas de resina no consolidada durante el moldeo.