Automotriz
Ignífugos > ► Aplicaciones
Automoción y transporte
Dado que los vehículos de transporte como aviones, barcos, trenes, autobuses y automóviles utilizan una gran cantidad de materiales inflamables y, por lo tanto, están sujetos a riesgos de incendio, pinfa ha compilado este folleto para explicar cómo sus tecnologías ignífugas pueden contribuir a la seguridad de materiales y vehículos. Después de muchos años de investigación y desarrollo, el ingeniero de materiales dispone ahora de una caja de herramientas completa de productos químicos sin halógenos. Las principales áreas de aplicación de los retardantes de llama en los vehículos de transporte son los polímeros para piezas eléctricas o estructurales, cables, alfombras, textiles decorativos y de tapicería y espumas poliméricas para aislamiento y tapicería. Abordando la necesidad de una mayor seguridad contra incendios, Mexpolimeros ofrece al mercado más de 1000 compounds retardantes de llama para las diversas aplicaciones de plástico en la automoción y el transporte. En la automoción, los retardantes de llama desempeñan un papel crucial para las piezas funcionales y estructurales de termoplásticos de ingeniería debajo del capó. Seguridad contra incendios para baterías fabricadas con poliolefina o estireno encuentre soluciones con retardadores de llama de Mexpolimeros. En las industrias de transporte masivo, camiones, aviones y marinos, los retardantes de llama también juegan un papel muy importante para proporcionar un buen aislamiento térmico. Los principales productos utilizados para este fin son las espumas de poliuretano rígido, poliolefinas reticuladas o mezclas plastificadas reticuladas de PVC con caucho de nitrilo. Vale la pena mencionar también el uso de tela recubierta de PVC plastificado para la producción de cubiertas para camiones y botes. El transporte juega un papel importante en nuestra sociedad moderna. Los diferentes tipos de transporte implican diferentes riesgos de incendio y diferentes escenarios de incendio. Por lo tanto, una variedad de diferentes estándares de incendios refleja diferentes escenarios de incendios. En los materiales de transporte se utilizan varios tipos de retardadores de llama según el tipo de material y su aplicación final. Los materiales utilizados en aplicaciones automotrices deben cumplir una amplia gama de requisitos de funcionalidad específica, bajas emisiones y desempeño frente al fuego. Los vehículos eléctricos y los autobuses necesitan materiales retardadores de llama que cumplan con requisitos de seguridad contra incendios cada vez más altos que en el pasado. Existen regulaciones estrictas con respecto a la seguridad contra incendios de los vehículos ferroviarios en la mayoría de los países del mundo. Un gran número de pasajeros en un espacio confinado con posibilidades de escape limitadas, como en un túnel, requieren propiedades especiales del material. Además de la inflamabilidad de los materiales, también deben tenerse en cuenta los efectos secundarios del fuego, como la densidad del humo y la toxicidad del humo. Estos estrictos requisitos limitan enormemente la selección de productos. En particular, los productos a base de fósforo sin halógenos ayudan a cumplir los requisitos impuestos a las piezas de goma y plástico para vehículos ferroviarios. Una aeronave es claramente un entorno de alto riesgo y, como tal, los requisitos de protección contra incendios en la aviación son particularmente estrictos.
Parte del coche ignífuga (interior)
Asiento, cinturón de seguridad, tela para techo, techo convertible, reposabrazos, molduras de puertas, molduras delanteras, molduras traseras, molduras laterales, bandeja de paquete trasera, dispositivo de control de inclinación de la cabeza hacia atrás, alfombra, tapete, visera parasol, parasol, cubierta de la caja de ruedas, etc.
Prueba de llama externa
UN ECE R100-02. Parte del reglamento del acuerdo de las Naciones Unidas sobre vehículos eléctricos a batería. Vehículos eléctricos, etc.
Prueba de llama de materiales de batería
Estándar actual No. UN R100-03 GB / T 31467.3 Estándar futuro GTR(Global Technical Regulations) 5.4.12
Flame retardancy to external flame
Flame retardancy for internal hot gas

Prueba de llama de materiales de batería
Estándar actual No. UN R100-03 GB / T 31467.3 Estándar futuro GTR(Global Technical Regulations) 5.4.12






Interiores
Las partes interiores para aplicaciones de transporte, es decir, automóviles, aviones, barcos, son sistemas complejos que incluyen elementos visibles, como pisos, textiles, asientos, lavabos, techos, paredes laterales, compartimientos de estiba, estantes para bolsas. , armarios, tableros de instrumentos y ventanas, y elementos que no sean visibles para los pasajeros, como conductos, cableado (capítulo 6), componentes eléctricos y electrónicos, mantas aislantes, revestimientos, selladores y adhesivos. Las propiedades de los materiales deben abordar las necesidades de los usuarios de los materiales. Estas necesidades incluyen las capacidades de procesamiento y producción de los proveedores y fabricantes de materiales; la capacidad de satisfacer las demandas de diseño, rendimiento, comodidad y estética de las aplicaciones interiores; y el cumplimiento de las normativas medioambientales, de salud y seguridad Los plásticos han revolucionado el diseño interior de los medios de transporte. Han demostrado ser materiales ideales para crear interiores cómodos, duraderos y estéticamente agradables, al tiempo que reducen el ruido, la aspereza, la vibración y el peso. Los plásticos ofrecen una flexibilidad de diseño que ayuda a los fabricantes a crear componentes innovadores, integrales, de una sola pieza y livianos, al tiempo que reduce costos, ahorra tiempo y ayuda a disminuir los problemas asociados con el rediseño interior. La elección correcta del material más adecuado depende en gran medida de los requisitos de la aplicación final. Por ejemplo, los paneles de instrumentos se hacían tradicionalmente con varios componentes separados que debían pintarse y que se mantenían unidos por una viga de soporte de acero que se encontraba detrás del panel. Hoy en día, gracias a la moderna tecnología de plásticos, los paneles de instrumentos están hechos de aleaciones de acrilonitrilo-butadieno-estireno (ABS), ABS / policarbonato (PC), PC, polipropileno (PP), polifenileno éter modificado (m-PPE) y SMA (estireno). anhídrido maleico) resinas. Estos plásticos permiten diseños complejos de elementos, como carcasas de bolsas de aire, soportes centrales para paneles de instrumentos y piezas grandes integradas en el panel de instrumentos. También se utilizan en la fabricación del resto del revestimiento interior del automóvil. Estos plásticos también son capaces de eliminar la necesidad de una viga de soporte de acero, lo que permite a los fabricantes ahorrar drásticamente los costos del panel de instrumentos al tiempo que reducen sustancialmente su peso. Los materiales poliméricos son predominantes y aparecen en una amplia gama de formas de productos, incluidas láminas o formas moldeadas, sándwiches de nido de abeja con cara compuesta, fibras textiles (telas o alfombras), espumas, selladores y adhesivos. Los interiores contienen actualmente materiales que tienen diferentes inflamabilidades. Se seleccionan de acuerdo con su aplicación particular y una variedad de factores adicionales, como disponibilidad, costo y procesabilidad. La mayoría de los polímeros utilizados necesitan FR para cumplir con los estándares actuales contra incendios. Los sistemas intumescentes, por ejemplo, son retardadores de llama muy eficaces, que pueden cumplir con los más altos estándares en cuanto a retardo de llama, densidad de humo y toxicidad del humo según sea necesario. La elección adecuada del retardante de llama ecológico depende en gran medida de la aplicación y del estándar de fuego requerido.
Cables
El transporte moderno es impensable sin cables. Los cables transmiten energía y cantidades de datos cada vez mayores. Un gran número de ellos se instalan en vehículos como automóviles, trenes, barcos o aviones. Se instalan en dirección horizontal debajo de pisos u horizontal y verticalmente entre paredes y techos. Por lo tanto, las pruebas de fuego para dichos cables también incluyen diferentes escenarios. Los cables generalmente contienen una cantidad sustancial de materiales poliméricos inherentemente inflamables como compuestos de aislamiento, revestimiento o cama. Debido a su presencia en todo el vehículo y la naturaleza de su instalación, un cable ardiendo puede causar incendios dramáticos y el fuego puede extenderse a grandes distancias. Las causas típicas de incendios en vehículos son contenedores de desechos encendidos o fugas de combustible o aceite. Dependiendo de las dificultades de las personas para escapar de un vehículo en llamas, los estándares de resistencia al fuego son más o menos severos. Dado que la fuga de aviones, barcos o trenes suele ser más difícil que desde un automóvil, los materiales utilizados en los primeros deben ser más resistentes al fuego de acuerdo con varias normas nacionales e internacionales. Los compuestos poliméricos retardadores de llama sin halógenos (HFFR) o libres de halógenos con bajo contenido de humo (LSFOH) se pueden utilizar de muchas formas para producir cables seguros y funcionales. Polímeros seleccionados y los correspondientes retardadores de llama, junto con algunos datos generales sobre los sistemas retardadores de llama (FR). Dependiendo del uso de un cable en un vehículo, se deben cumplir diferentes estándares y los materiales deben elegirse de acuerdo con las tensiones mecánicas y térmicas durante la instalación y la vida útil. No solo el cable, sino toda la construcción del vehículo debe ser ignífugo. Cabe mencionar en particular los conductos de cables que se utilizan a menudo para alojar cables y protegerlos de daños. Estos conductos deben tener un nivel de retardo de llama comparable al de los cables, pero no necesitan tener la flexibilidad de un cable y suelen estar fabricados con materiales termoplásticos como PVC o poliolefinas, principalmente PE o PP, como matriz polimérica. Una formulación para un conducto de cable basada en poliolefinas podría ser más o menos comparable a las formulaciones de compuestos de cable con una cantidad relativamente alta de hidróxido de aluminio o hidróxido de magnesio, así como a los sistemas FR intumescentes como se menciona a continuación. Se necesitan altos niveles de llenado de> 50% en peso de un retardante de llama mineral para garantizar las propiedades FR relevantes, p. Ej. buenas clasificaciones UL 94V. El mecanismo de trabajo de los FR minerales se basa en fenómenos físicos. Por lo tanto, se necesitan cantidades relativamente altas de estos materiales para alcanzar una alta resistencia a las llamas en comparación con los sistemas FR que funcionan a través de rutas químicas específicas. Para TPE-S, TPE-V, TPE-O y poliolefinas, los sistemas intumescentes se pueden usar a niveles de carga moderados para pasar el cable vertical UL-94, UL-62 (VW-1, cables y cordones flexibles de EE. UU.) (UL 1581), o pruebas de cable de 45° (ISO 6722/1). La nueva familia de TPE retardantes de llama sin halógenos, por ejemplo, es una alternativa al revestimiento y aislamiento de vinilo flexible tradicional para, por ejemplo, aplicaciones de electrónica de consumo, cf. capítulo 6 de este folleto. Se pueden utilizar, entre otros, para extrusión de cables, tubos corrugados y conductos de cables. El mecanismo intumescente asegura un alto rendimiento de FR y una densidad / toxicidad de humo muy baja. Los sistemas intumescentes modernos basados en partículas tratadas en la superficie incluso pasan las exigentes pruebas de almacenamiento de agua requeridas en la industria del cable. Debido a una carga de FR moderada, la tecnología TPE HFFR alcanza un rendimiento de FR muy bueno combinado con una excelente estética y propiedades hápticas. Los siguientes capítulos describen con más detalle algunos compuestos de cables para su uso en vehículos. En los vehículos de carretera, los cables se utilizan en gran número, principalmente bajo el capó. El uso en constante crecimiento de dispositivos electrónicos en dichos vehículos generó una gran demanda de, p. Ej. cables de bus de datos para sensores y sistemas de monitorización durante las últimas décadas. En 1955, un automóvil de pasajeros típico contenía 45 m de cables. En la década de 1960, se instalaron aproximadamente 200 m de cables. Hoy en día, se instalan hasta 1500-5000 m de cables diferentes en un vehículo de carretera según el tipo y el equipamiento. El enfoque actual se centra en un aislamiento y revestimiento de cables más delgados y en compuestos de cables menos densos del mismo nivel de rendimiento para reducir el peso de esta parte integral de un automóvil. Dependiendo de su uso, p. Ej. su distancia al motor, los cables de los automóviles deben soportar ciertos rangos de temperatura que se clasifican desde la clase A a la H (T1 a T8). De acuerdo con estas clases de temperatura, se pueden utilizar diferentes polímeros (productos halogenados y libres de halógenos) para producir compuestos de aislamiento y revestimiento de cables. Los cables de los automóviles no solo tienen que ser resistentes a un amplio rango de temperaturas, sino también a diferentes medios como aceites, ácido de batería o combustibles para evitar grandes daños después de un derrame de una pequeña cantidad de fluidos tan agresivos.
Trenes
Es importante tener en cuenta que también en los sistemas de transporte público masivo como trenes, barcos y aviones, los incendios no se pueden evitar por completo. Por lo tanto, la propagación de la llama debe ser lenta y el desarrollo de humo debe ser lo más bajo posible para que las personas puedan escapar de manera segura. Esto se refleja en normas más estrictas en comparación con los vehículos de transporte por carretera. En los últimos años, se han realizado esfuerzos para desarrollar estándares comunes para los materiales que se utilizarán en los trenes en Europa; el CEN/TS 45545 los describe. Los detalles se darán en el capítulo sobre normas de este folleto. Entre otros, se requieren pruebas para la propagación vertical de la llama, la densidad del humo o la toxicidad del humo. Se instalan numerosos cables en los trenes para diferentes propósitos. En cada vagón, se requieren diferentes cables, p. Ej. para iluminación, paneles de control y para información y entretenimiento de los pasajeros. En la locomotora se instalan cables de motor, paneles de control y diferentes cables de comunicación con el tren. Entre los vagones individuales, los cables de puente garantizan la transmisión de datos y energía. Como se mencionó anteriormente, los cables para trenes deben cumplir con estrictos estándares de resistencia al fuego y bajo desarrollo de humo. Por esta razón, aquí se utilizan normalmente mayores cantidades de retardantes de llama minerales en comparación con los cables para automóviles. Esto conduce a un retardo de llama mejorado y al mismo tiempo a una densidad de humo reducida. Un contenido típico de ATH en tales cables es de alrededor del 60% en peso, pero puede variar según la formulación detallada. De acuerdo con su instalación y uso, las propiedades mecánicas y la resistencia de los cables frente a los impactos ambientales deben ajustarse, p. Ej. Los cables que estén cerca de instalaciones que contengan fluidos deben ser resistentes a estos medios.
Enchufes y cargador en movilidad eléctrica
Requisitos clave:
- Buena estabilidad dimensional
- Excelentes propiedades de alto impacto
- UL 94 V-0
- Productos: mezcla de PA/ABS y PBT no reforzado
- PA/ABS, no reforzado, alto impacto, V-0 @ 0,8 mm
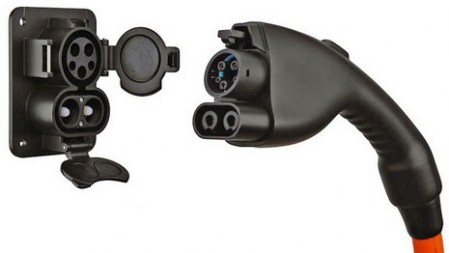
Carcasa de la batería / Conector de la batería / Caja de fusibles
Requisitos clave
- Buena estabilidad dimensional
- Buenas propiedades mecánicas
- UL 94 V-0
- Ferrocarril: cumple con la norma EN 45545-2 en términos de LOI, densidad de humo y toxicidad.
- Productos: PP-FR
- PP copo, sin relleno, V-0 a 0,75 mm, sin halógenos
- Copo de PP, relleno de talco al 25%, V-0 a 1,5 mm
- Copo de PP, relleno de mineral al 25%, V-0 a 1,5 mm
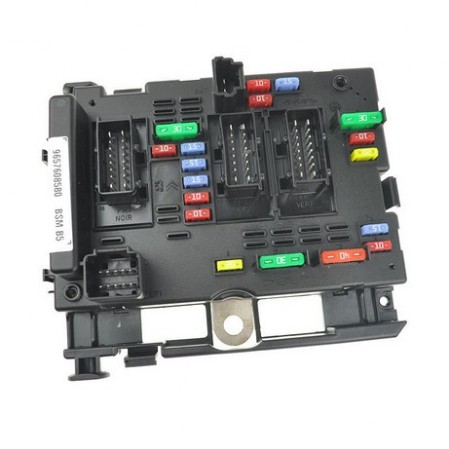
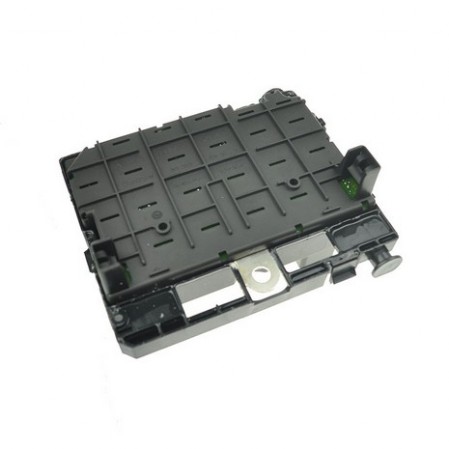
Unidad de control de potencia
Requisitos clave :
- Buena estabilidad dimensional
- Baja deformación
- Buenas propiedades mecánicas
- UL 94 V-0
- Productos: PBT / ASA-FR, reforzado
- Mezcla de PBT / ASA, 20% reforzado con vidrio, V-0 a 0,75 mm
- Mezcla de PBT / ASA, 30% reforzado con vidrio, V-0 a 0,75 mm
Tubería corrugada
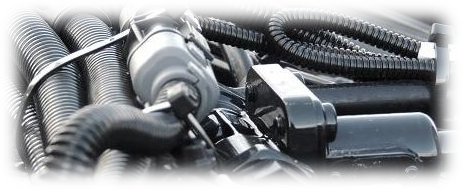
Solicitud: Aprobación Norm T3B (125°C), V2 @ 1.6 mm
Producto: Mexplen M 0023 O V2 T
Requerimientos del proyecto:
Altas propiedades mecánicas;
Estabilidad dimensional alta;
Resistencia a altas temperaturas.
Tubería corrugada
Solicitud: Aprobación Norm T3B (125°C), V2 @ 1.6 mm
Producto: MEXPLEN 0024 V2 NATURAL LH C E
Requerimientos del proyecto:
Altas propiedades mecánicas;
Estabilidad dimensional alta;
Resistencia a altas temperaturas.