Rigidez dieléctrica
Laboratorio > ► Ensayos eléctricos
Rigidez dieléctrica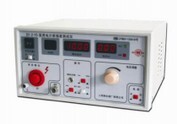
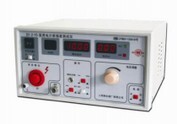
Las propiedades dieléctricas más importantes son la constante dieléctrica, ε, y el factor de pérdida dieléctrica, tan δ. La resistencia dieléctrica es una medida de la resistencia eléctrica de un material como aislante. La resistencia dieléctrica se define como el voltaje máximo requerido para producir una ruptura dieléctrica a través del material y se expresa en voltios por unidad de espesor. Una mayor resistencia dieléctrica representa una mejor calidad de aislante. Estas propiedades son de interés para corrientes alternas; ε indica la polarización en un campo eléctrico y, por lo tanto, gobierna la magnitud de la corriente alterna transmitida a través del material cuando se usa en un condensador. Para la mayoría de los polímeros, ε está entre 2 y 5, pero puede alcanzar valores de hasta 10 para sistemas llenos. De mayor importancia es el factor de pérdida, tan δ, que denota la fracción de la corriente alterna transmitida perdida por la disipación en el material. Parece que los polímeros con la resistencia específica más alta también muestran las pérdidas dieléctricas más bajas. Cabe señalar que los valores dados son muy esquemáticos; Las pérdidas dependen en gran medida de la frecuencia y la temperatura. La mayoría de los polímeros son aislantes eléctricos, ya que los electrones externos de los átomos están localizados, formando enlaces covalentes y no dan lugar a corriente eléctrica cuando se someten a un campo eléctrico. El test de rigidez dieléctrica es un test obligatorio y exigido por múltiples estándares, y es uno de los ensayos indispensables para el marcado CE. El medidor de rigidez dieléctrica aplica alta tensión durante un tiempo programable entre la masa y determinados la corriente de fuga y dictaminándose si Pasa o No Pasa, en base a los límites establecidos en dicha corriente de fugas. Los ensayos de rigidez dieléctrica, son habitualmente con tensión alterna, aunque también hay equipos en DC. Cuando el campo eléctrico supera los 100 KV en los polímeros se produce una descarga eléctrica, es decir, se causa la ruptura dieléctrica y el material se vuelve conductor con el consiguiente deterioro. El valor de la intensidad del campo al que se produce la ruptura depende del espesor de la muestra por lo que se describe a través de la denominada rigidez dieléctrica que se expresa en KV por unidad de espesor, usualmente cm . La rigidez dieléctrica depende de las imperfecciones presentes en el material, al aumentar el espesor de la muestra la probabilidad de existencia de defectos aumenta y por ello la rigidez dieléctrica disminuye, por la misma razón las muestras sometidas a cargas mecánicas pueden presentar valores menores de la rigidez dieléctrica. La rigidez dieléctrica de un material aislante se define como el voltaje máximo requerido para producir una ruptura dieléctrica. La rigidez dieléctrica se expresa en voltios por unidad de espesor, como V / mL. Todos los aisladores permiten que una pequeña cantidad de corriente se filtre a través o alrededor de ellos mismos. Solo un aislante perfecto, si existe tal aislante, puede estar completamente libre de pequeñas fugas de corriente. La pequeña fuga genera calor, lo que facilita el acceso a más corriente. El proceso se acelera lentamente con el tiempo y la cantidad de voltaje aplicado hasta que ocurre una falla en términos de ruptura dieléctrica, o lo que se conoce como perforación. Obviamente, la rigidez dieléctrica, que indica la fuerza eléctrica de un material como aislante, es una característica muy importante de un material aislante. Cuanto mayor sea la rigidez dieléctrica, mejor será la calidad de un aislante. Se han desarrollado tres procedimientos básicos para determinar la rigidez dieléctrica de un aislante. Normalmente se emplean un transformador variable y un par de electrodos. Se utilizan muestras de cualquier espesor deseable preparadas a partir del material a ensayar. Espesor de la muestra de 1/16 pulg. es bastante común. El primer procedimiento se conoce como método de corta duración. En este método, el voltaje se incrementa desde cero hasta la ruptura a una tasa uniforme. La tasa de aumento es generalmente de 100, 500, 1000 o 3000 V / seg hasta que ocurre la falla. La falla se hace evidente por la ruptura o descomposición real de la muestra. A veces, se emplea un disyuntor u otro dispositivo similar para señalar la ruptura de voltaje. Esto no se considera una indicación positiva de ruptura de voltaje debido a que otros factores, como una descarga, la corriente de fuga, la corriente de corona o la corriente de magnetización del equipo, pueden influir en dichos dispositivos indicadores. El segundo método se conoce como método de tasa de aumento lenta. La prueba se lleva a cabo aplicando el voltaje inicial aproximadamente igual al 50 por ciento del voltaje de ruptura, según lo determinado por la prueba de corta duración o según se especifique. A continuación, se aumenta el voltaje a un ritmo uniforme hasta que se produce la ruptura. El método de prueba paso a paso requiere aplicar un voltaje inicial igual al 50 por ciento del voltaje de ruptura, según lo determinado por la prueba de corta duración, y luego aumentar el voltaje en incrementos iguales y mantenerlo durante períodos de tiempo especificados hasta que la muestra se descomponga. En casi todos los casos, los valores de rigidez dieléctrica obtenidos por el método paso a paso se corresponden mejor con las condiciones de uso reales. Sin embargo, las fallas del servicio generalmente ocurren a un voltaje por debajo de la rigidez dieléctrica nominal debido al factor de tiempo involucrado. La rigidez dieléctrica de un material aislante se calcula de la siguiente manera:
Tensión de ruptura (V)
Rigidez dieléctrica (V/mm) = --------------------------------
Espesor (mm)
Factores que afectan los resultados de la prueba
Espesor de la muestra. La rigidez dieléctrica de un aislante varía inversamente con la potencia fraccional (generalmente 0.4) del espesor (3). La muestra más gruesa requiere un voltaje más alto para lograr el mismo gradiente de voltaje. A mayor voltaje, se observa una reducción en los enlaces intermoleculares, como resultado de la expansión térmica creada por la generación de calor. Las secciones más gruesas también tienen vacíos internos, fallas, humedad, falta de uniformidad y una mayor fuga de corriente, lo que provoca una falla temprana de la muestra (4). Las películas delgadas con un valor de rigidez dieléctrica más alto se han utilizado con éxito en muchas aplicaciones críticas que ahorran espacio. La curva de rigidez dieléctrica frente a espesor está disponible de los proveedores de materiales.
Temperatura. La rigidez dieléctrica disminuye con el aumento de la temperatura de la muestra. Si el diseño requiere el uso del producto a varias temperaturas, se deben evaluar cuidadosamente los valores de rigidez dieléctrica a las temperaturas previstas. Curiosamente, la rigidez dieléctrica del material por debajo de la temperatura ambiente es constante e independiente del cambio de temperatura.
Humedad. La humedad afecta la rigidez dieléctrica del material. La humedad de la superficie, así como la humedad absorbida por el material higroscópico, afecta los resultados.
Electrodos La rigidez dieléctrica de un material se ve afectada por la geometría del electrodo, el área del electrodo y la composición del material base del electrodo. Generalmente, el voltaje de ruptura disminuye al aumentar el área del electrodo.
Tiempo. La tasa de aplicación de voltaje altera significativamente los resultados de la prueba. Como se mencionó anteriormente en este capítulo, los valores de rigidez dieléctrica obtenidos usando el método paso a paso son más bajos que los obtenidos por la prueba de tiempo corto.
Esfuerzo mecánico. El esfuerzo mecánico tiende a reducir sustancialmente los valores de rigidez dieléctrica
Los defectos de procesamiento tales como líneas de soldadura deficientes, huecos, burbujas y líneas de flujo provocadas por prácticas de procesamiento deficientes tienden a reducir la rigidez dieléctrica en cualquier lugar de 30 a 60 por ciento, dependiendo de la gravedad del defecto.
Limitaciones e interpretaciones de las pruebas
Al diseñar piezas de plástico para aplicaciones eléctricas, los valores de rigidez dieléctrica deben estudiarse en detalle. Si las piezas se diseñan en base a valores derivados de la literatura publicada sin la debida atención a los efectos del grosor, la humedad, la temperatura, el estrés mecánico y las condiciones reales de uso, los resultados podrían resultar desastrosos. Las condiciones reales de uso de los materiales aislantes son bastante diferentes a las condiciones de la prueba de rigidez dieléctrica y, por lo tanto, el énfasis real debe estar siempre en el rendimiento del material en servicio real.
Procedimiento de prueba
Existen tres procedimientos básicos que se pueden usar para determinar la resistencia dieléctrica de un aislante. Cada uno de estos tres métodos tiene la misma configuración básica, que consiste en la muestra de prueba colocada entre dos electrodos en aire o aceite. Estos procedimientos son:
- método de tiempo corto
- método de tasa de aumento lento
- método paso a paso
Método de tiempo corto
Para la prueba más común, el método de tiempo corto, el voltaje se aplica a través de los dos electrodos y se eleva desde cero hasta la descomposición dieléctrica a una velocidad uniforme. La descomposición ocurre cuando un quemado eléctrico perfora la muestra o se produce descomposición en la muestra. La tasa de aumento de voltaje está determinada por el tiempo que tarda la muestra en alcanzar la ruptura dieléctrica.
Método de tasa de aumento lento
El método de velocidad de subida lenta comienza con el 50% del voltaje de ruptura según lo determinado por el método de tiempo corto y se incrementa a una velocidad uniforme.
Método paso a paso
El método paso a paso comienza con el 50% de la prueba de tiempo corto y luego el voltaje se incrementa en incrementos iguales durante un período de tiempo específico hasta la ruptura. La prueba a veces se realiza en aceite para evitar el arco eléctrico desde el electrodo hasta el suelo.
Procedimiento de test de tracking index según IEC60112
En una placa de material plasticos , se aplican 2 electrodos con una tensión de prueba ajustable entre 100 y 100 KV. Se aplican 50 gotas de una solución de agua con cloruro amónico 0.1% entre los electrodos y se la aumenta tensión gradualmente. El criterio de fallo es una corriente de corte ≥0,5 A durante un tiempo> 2s. El grosor de 3 mm se considera representativo del rendimiento del material en cualquier grosor.
Rendimiento (PLC)
El índice de seguimiento comparativo o CTI se utiliza para medir las propiedades de corte eléctrico (seguimiento) de un material aislante. Es una falla eléctrica en la superficie de un material aislante en una exposición inicial al calor del aislante original, que produce más flujo de corriente, más calor y, finalmente, falla completa. Expresado como voltaje que causa seguimiento después 50 gotas de solución de cloruro de amonio al 0,1%
Normas : Rigidez dieléctrica ASTM D149, IEC 60243, Dielectric strength EN60065, EN60204-1,EN60335-1,EN60598-1,EN60601-1,EN60950,EN61010-1,CE