Cauchos > ► Grupo R
Cauchos (SBR) son copolímeros de estireno y butadieno
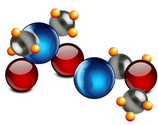
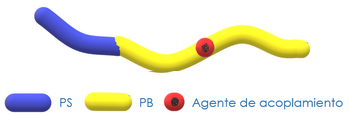
- Emulsión SBR (e-SBR): SBR caliente o SBR frío
- Solución SBR (s-SBR)
Diferencia entre los grados E-SBR y S-SBR
Existe una creciente competencia entre los grados E-SBR y S-SBR. Y desde el comienzo de su desarrollo, los S-SBR sufrieron problemas de procesamiento debido a su estrecha MWD. De hecho, el principal problema que debe superar el S-SBR siempre ha sido la no intercambiabilidad con los E-SBR comúnmente utilizados por los productores de neumáticos: el número limitado de grados provenientes del proceso de emulsión hace que sea más fácil cambiar de un proveedor al otro, sin ninguna reconfiguración de las máquinas y procedimientos de procesamiento. Por lo tanto, uno de los principales esfuerzos de los productores de S-SBR ha sido la búsqueda de una mejor procesabilidad, que se obtiene modificando la macroestructura del polímero (es decir, MWD y LCB). En este sentido, el uso de agentes de acoplamiento como SiCl4 y SnCl4 en la síntesis aniónica por lotes proporcionó una forma de ampliar el MWD agregando una estructura en forma de estrella al mismo tiempo. Para maximizar la participación en el mercado, las compañías automotrices han desarrollado continuamente vehículos con un rendimiento y durabilidad superiores (mayor kilometraje). El caucho de copolímero de estireno-butadieno (SBR) es representativo de los cauchos sintéticos utilizados para neumáticos, y el nombre generalmente indica una SBR en emulsión obtenida a través de una polimerización redox de estireno y butadieno en una solución acuosa de un agente emulsionante. Debido a factores técnicos como su adecuación para la producción en masa, los grados de polímeros se han unificado internacionalmente, tienen una capacidad de trabajo superior entre los cauchos sintéticos y exhiben un agarre de alto nivel. Rendimiento (fuerza de agarre en la carretera en condiciones húmedas) que no se puede obtener con caucho natural, la emulsión SBR tiene una historia de ser ampliamente utilizada como polímeros de la banda de rodadura. Por el contrario, la solución SBR es un polímero sintetizado en una reacción de polimerización aniónica viva en la que se utiliza un compuesto de litio orgánico como iniciador de la polimerización en un disolvente de hidrocarburo, y se ha dicho que su capacidad de procesamiento y resistencia inferiores en la etapa de formación son sus puntos débiles. Sin embargo, posteriormente ha habido avances en el desarrollo y estudios que hacen uso de las propiedades superiores de diseño estructural de las reacciones de polimerización aniónicas vivas, y en la actualidad, varios grados de polímeros nuevos donde los elementos estructurales moleculares, como la distribución del peso molecular, la microestructura del butadieno y los productos químicos la modificación de los extremos de las cadenas moleculares ("modificación del extremo de la cadena" en lo que sigue) se controla con precisión, por lo que la idea de utilizar el diseño estructural molecular en el desarrollo de materiales para neumáticos ha llegado a nuestro pensamiento.
Estructura de SBR
En virtud de su polimerización por radicales libres, SBR es un copolímero aleatorio. Se encuentra que las unidades de butadieno son aproximadamente el 20% en la configuración 1,2, el 20% en el cis-1,4 y el 60% en el trans-1,4 para el polímero elaborado a 50°C, con el porcentaje de tmns -1,4 que se convierte en polímero de fbr más alto elaborado a temperaturas más bajas Como consecuencia de su estructura irregular, el SBR no cristaliza Las reacciones de ramificación debido a la transferencia de cadena al polímero y a la polimerización de ambos enlaces dobles de una unidad de dieno se vuelven extensas si se permite que la conversión demasiado alto o no se usa un agente de transferencia de cadena en la polimerización de SBR Sin embargo, se ha demostrado que SBR tiene exactamente un doble enlace por unidad de butadieno. Por tanto, no se producen reacciones secundarias extensas durante su formación, al menos hasta aproximadamente un 75% de conversión.
Propiedades SBR
Los cauchos SBR necesitan la presencia de cargas reforzantes para alcanzar un nivel satisfactorio de resistencia mecánica. Con las cargas se logra una resistencia a la abrasión que frecuentemente supera al caucho natural a un precio competitivo. En comparación con el caucho natural, el SBR presenta una mejor resistencia al envejecimiento y un rango más amplio de temperatura de trabajo de -50 a 110ºC. Presenta una moderada resistencia al ozono e intemperie debido a la presencia de cadenas moleculares insaturadas. La resistencia a los productos químicos inorgánicos es bastante buena, pero no presenta un buen comportamiento frente a ácidos oxidantes. De forma general, no es adecuado para aplicaciones que impliquen el contacto con líquidos orgánicos. La principal aplicación de los cauchos SBR se encuentra en la fabricación de neumáticos, donde prácticamente ha desplazado al caucho natural. Se emplea también en la fabricación de artículos técnicos, como bandas transportadoras, correas de transmisión o mangueras, en artículos de uso doméstico como juguetes, y en usos sanitarios como guantes. Cabe destacar su aplicación en la industria del calzado como componente de las suelas. La temperatura de transición vítrea (Tg) es la temperatura a la que un polímero viscoso suave cambia a una dureza similar al vidrio. Termodinámicamente es una transición de segundo orden, caracterizada por pequeños cambios en el índice de refracción, volumen específico, coeficiente de expansión térmica, velocidad del sonido, etc. Además de la determinación de Tg mediante la medición de estas cantidades, se encontró una relación simple entre la temperatura de transición vítrea y la prueba de flexión de torsión a baja temperatura de Gehman (ASTM D 1053). La Tg depende de la estructura y el orden del polímero. Para copolímeros SBR preparados por polimerización en emulsión a 50°C, la temperatura de transición vítrea se puede calcular a partir del contenido de estireno unido (S = fracción en peso de estireno) por:
Tg = (- 87 + 135S) / (1 - 0.5S)
Polimerización
Los copolímeros tribloque de estireno-butadieno se obtienen por polimerización aniónica iniciada por alquilos de litio en medios cicloalifáticos como disolvente (generalmente ciclohexano, ciclopentano). Los extremos de la cadena polimérica sobreviven incluso cuando el monómero se agota por completo y reinician la reacción de polimerización cuando el monómero se agrega nuevamente. Debido a la ausencia de reacciones de terminación, los extremos de la cadena activa del polímero no terminan inherentemente, creciendo continuamente hasta el agotamiento de los monómeros completos. El disolvente, el estireno y el iniciador se alimentan al reactor. Luego comienza la polimerización, que es básicamente adiabática, y se forma el bloque de poliestireno. Cuando se completa la polimerización de estireno, se alimenta butadieno y luego se genera el segundo monómero de bloque. Cuando el segundo monómero se convierte por completo, se agrega un agente de acoplamiento para crear la estructura deseada de polímero que será lineal o radial dependiendo de la funcionalidad del agente de acoplamiento. Algunas calidades, con un alto contenido de polímero SB sin acoplar, también requieren un agente de terminación para la terminación final de los extremos de la cadena activa a fin de evitar el amarilleo cuando se agregan los antioxidantes. Durante la polimerización, los parámetros como la temperatura, la velocidad de flujo y la agitación se controlan para obtener la conversión correcta. Normalmente se permite que la polimerización proceda a una conversión de aproximadamente el 60% en la polimerización en frío y el 70% en la polimerización en caliente antes de que se detenga con un agente de detención corta que reacciona rápidamente con los radicales libres. Los E-SBR producidos a bajas temperaturas de polimerización tienen menos ramificación de cadena que los producidos a temperaturas más altas. A una viscosidad equivalente, el E-SBR polimerizado en frío es normalmente más fácil de procesar que el E-SBR polimerizado en caliente, y esto se aplica particularmente a una mejor banda en los molinos, menos contracción después del calandrado y una superficie superior de compuestos de neumáticos verdes. Las gomas calientes dan una mejor resistencia verde porque tienen más ramificaciones de cadena. Los tipos especiales de E-SBR son los llamados cauchos con extensión de aceite (OESBR) en el caso de polímeros con aceite extendido o masterbatches de negro de carbón, estos materiales se agregan como dispersiones al látex despojado.
Polimerización en emulsión (E-SBR)
El proceso de polimerización radical en emulsión tiene varias ventajas. Normalmente se usa en condiciones de reacción leves que son tolerantes al agua y solo requiere la ausencia de oxígeno. El proceso es relativamente robusto a las impurezas y susceptible de utilizar una gama de monómeros funcionalizados y no funcionalizados. Los beneficios adicionales incluyen el hecho de que la polimerización en emulsión proporciona altos contenidos de sólidos con baja viscosidad de reacción y es un proceso rentable. El estado físico del sistema de emulsión (coloidal) facilita el control del proceso. Los problemas térmicos y de viscosidad son mucho menos significativos que en la polimerización en masa. La polimerización de E-SBR, que incluye monómeros (estireno y butadieno), agua, emulsionante, sistema iniciador, modificador, campo corto y un sistema estabilizador. Se puede producir por polimerización en emulsión de radicales libres de estireno y butadieno a una temperatura entre 50 y 60°C (emulsión SBR caliente) o aproximadamente a 5°C (emulsión SBR fría). El proceso SBR de emulsión caliente, conduce a un polímero más ramificado que el proceso de emulsión fría. Las calidades SBR producidas usando este proceso exhiben características de procesamiento excepcionales tales como baja contracción del molino, buena estabilidad dimensional y buenas características de extrusión. Por otro lado, el proceso SBR de emulsión en frío tiene una mejor resistencia a la abrasión y, en consecuencia, ofrece un mejor desgaste de la banda de rodadura y propiedades dinámicas. También tiene propiedades mecánicas superiores, como resistencia a la tracción en comparación con los grados producidos por la ruta de polimerización de la emulsión caliente. El butadieno y el estireno pueden copolimerizarse mediante radicales, iones y mecanismos de coordinación. Hoy en día, el más utilizado es la copolimerización de radicales libres en emulsión y la copolimerización de aniones en solución. La copolimerización por radicales libres de butadieno y estireno en emulsión (E-SBR) tiene lugar a temperaturas de alrededor de 50°C (cauchos calientes) o 5°C (cauchos fríos). En ambos casos, los sistemas de emulsión utilizados son prácticamente idénticos (emulsionantes aniónicos, mercaptanos como agentes de transferencia de cadena, ditiocarbamatos como agentes de parada de la copolimerización); usan diferentes tipos de iniciadores. Mientras que a temperaturas de 50°C son principalmente peroxodisulfatos, a 5°C son sistemas de iniciación de reducciónoxidación que consisten en hidroperóxido (hidroperóxido de p-mentano o hidroperóxido de pinano) y un componente redox, generalmente en forma de quelato (sal de sodio del ácido etilendiaminotetraacetato y sodio formaldehído sulfoxilato). La alimentación de monómero usualmente contiene 23.5% en peso de estireno y 76.5% en peso de butadieno; sin embargo, la composición también puede ser diferente.
Propriedades E-SBR
E-SBR está disponible comercialmente en viscosidades Mooney que varían de 30 a aproximadamente 120 (ML1 + 4 @ 125°C). Los grados E-SBR de viscosidad Mooney más baja se unen más fácilmente en el molino, incorporan rellenos y aceite más fácilmente, muestran menos generación de calor durante el mezclado, se calandran más fácilmente, se encogen menos, dan tasas de extrusión más altas y tienen una apariencia de extruido superior que la viscosidad Mooney más alta grados. Por otro lado, los SBR de alta viscosidad Mooney tienen una mejor resistencia al verde, menos porosidad en el vulcanizado y aceptan cargas de aceite y relleno más altas. E-SBR tiene altos pesos moleculares, amplia distribución, alto nivel de ramificación y, por lo general, también contiene gel. La disminución de la temperatura de polimerización reduce la velocidad de las reacciones elementales que conducen a la ramificación y transferencia; por lo tanto, los E-SBR fríos son menos ramificados, tienen una distribución más estrecha y menos contenido de gel. La formación de gel y la ramificación de la cadena también se reducen mediante la terminación de la copolimerización a una conversión del 60 al 70%. Los SBR de tipo emulsión tienen buenas propiedades de procesamiento, sin embargo, los posibles restos de emulsionantes (que pueden contener) deterioran sus propiedades de histéresis. A medida que aumenta el peso molecular del SBR, mejoran la resistencia a la vulcanización y las propiedades mecánicas, particularmente la resistencia a la tracción y el conjunto de compresión. La capacidad de procesamiento de SBR mejora a medida que se amplía su distribución de peso molecular. Formación de fracciones de alto peso molecular con el aumento de la media sin embargo, el peso molecular puede evitar mejoras en la procesabilidad. Esto se debe al hecho de que la tendencia a la formación de gel también aumenta a pesos moleculares más altos. Dado que el SBR carece de las cualidades de autorrefuerzo del caucho natural debido a la cristalización inducida por el estrés, las vulcanizadas de goma de SBR tienen propiedades de tracción más bajas. La propiedad de tracción de los vulcanizados E-SBR depende en gran medida del tipo y la cantidad de carga en el compuesto. Las existencias de goma curada tienen solo una resistencia a la tracción de 2.8 a 4.2 MPa, mientras que las cargas de partículas de negro de humo pueden producir una resistencia a la tracción de 27.6 Mpa. Aunque el conjunto de compresión de algunos de los compuestos E-SBR comunes es alto, mediante una composición adecuada y mezclando, es posible obtener vulcanizados E-SBR con un conjunto de baja compresión.
Características clave
- Baja resiliencia y baja resistencia a la tracción.
- Resistencia excepcional a la abrasión
- Baja resistencia al aceite, otros fluidos de hidrocarburos y al ozono
- Los polímeros calientes son difíciles de procesar con baja resistencia en verde
- Poca resistencia al desgarro
- Las resinas con alto contenido de estireno tienen buenas propiedades a bajas temperaturas pero endurecen
Propiedades electricas
SBR es un polímero no polar y sus vulcanizados son malos conductores de la electricidad. Las propiedades eléctricas de E-SBR dependen en gran medida de la cantidad y tipo de emulsionante y agente (s) de coagulación utilizados.
Resistencia a los fluidos
Si bien los vulcanizados E-SBR son resistentes a muchos solventes polares como ácidos y bases diluidos, se hincharán considerablemente cuando entren en contacto con gasolina, aceites o grasas. SBR no se recomienda para la exposición a aceites de petróleo, la mayoría de los hidrocarburos, ácidos fuertes o ozono. Debido a esta limitación, SBR no puede usarse en aplicaciones que requieren resistencia al hinchamiento en contacto con solventes de hidrocarburos.
Propiedades de curado
El SBR se puede curar con una variedad de sistemas de curado que incluyen azufre (aceleradores y azufre), peróxidos y resinas fenólicas. El procesamiento de los compuestos SBR se puede realizar en un molino, mezcladores internos o extrusoras mezcladoras. Los compuestos SBR se curan de varias maneras mediante compresión, moldeo por inyección, autoclaves de aire caliente o vapor, hornos de aire caliente, hornos de microondas y combinaciones de estas técnicas.
Polimerización en emulsión (S-SBR)
La solución SBR se produce por polimerización en solución aniónica "sin terminación" de estireno y butadieno con un iniciador de alquil litio (por ejemplo, butilio) en un disolvente hidrocarbonado, generalmente hexano o ciclohexano. Permite la síntesis de polímeros con una distribución de peso molecular muy estrecha y menos ramificación de la cadena. Los cauchos de solución de butadieno estireno (S-SBR) se fabrican por copolimerización aniónica de butadieno y estireno, o por polimerización aniónica viva, durante la cual el primer monómero está presente en el sistema de polimerización y cuando finaliza la polimerización, se agrega el segundo monómero. Una polimerización de anión secuencial produce polímeros en bloque, y los bloques no contienen unidades estructurales del otro polímero. Su longitud está dada solo por la relación de iniciador de monómero; dependiendo del tipo de agente de terminación se pueden preparar copolímeros lineales, ramificados o en estrella. Son representantes típicos de los cauchos termoplásticos.
Propriedades S-SBR
Los grados S-SBR tienen mayor flexibilidad, rendimiento, propiedades mecánicas superiores, como resistencia a la tracción, baja resistencia a la rodadura, etc., especialmente cuando se usan en neumáticos. La solución de SBR tiene una distribución de peso molecular más estrecha, un peso molecular más alto y un mayor contenido de cis-1,4-polibutadieno que la polimerización en emulsión de SBR. S-SBR rara vez tiene más del 2% de materiales no de goma en su forma terminada, mientras que E-SBR puede tener un contenido de emulsionante (jabón) de hasta 5% y materiales no de goma a veces superiores al 10%. Caucho de estireno butadieno funcionalizado (SSBR) con alto contenido de vinilo, reduce la pérdida de rodadura, reduce el consumo de combustible y las emisiones contaminantes y mejora la tracción de los neumáticos y las características de resistencia al desgaste. La resistencia al ozono de el SBR es superior a la del' caucho natural, pero cuando las grietas o cortes comienzan en SBR, crecen mucho más rápidamente. Sin embargo, el defecto más grave de ambos tipos de neumáticos SBR fbr es su menor resiliencia y mayor acumulación de calor. El desgaste de la banda de rodadura del material sintético es al menos tan bueno como el del caucho natural. La resistencia a la intemperie del SBR es mejor que la del 'caucho natural "Cold" SBR es superior al producto estándar porque contiene menos caucho de bajo peso molecular (no reforzable), menos ramificación y reticulación de la cadena, y una proporción más alta (70%) de la configuración trans-1,4 alrededor del doble vínculo.
Características clave
- Buena resistencia y resistencia a la tracción
- Excepcional resistencia a la abrasión y fatiga
- Baja resistencia al aceite, otros fluidos de hidrocarburos y ozono
- MWD estrecho, poca ramificación
- Microestructura: Cis 35%, - Trans 2%, - Vinilo 13%
- Tg: -98°C Tm: nulo
- Control de estructura polimérica Gran variación
Cuándo no usar elastómero SBR:
No se recomienda usar el elastómero SBR en aplicaciones eléctricas o aplicaciones expuestas a aceite, ozono y condiciones climáticas extremas. ¿Está buscando un elastómero que cumpla con estos criterios? Contáctenos y lo ayudaremos a seleccionar el elastómero adecuado para su aplicación.
SBR vs. caucho natural
SBR es un sustituto del caucho natural cuando se busca una solución económica. Los elastómeros SBR se degradan con el tiempo si se exponen al oxígeno y al ozono y se hinchan si se exponen a aceites de hidrocarburos. Pero a diferencia del caucho natural, el elastómero SBR tiende a endurecerse con el tiempo en lugar de suavizarse.
Aceite diluyente
Agregndo aceite diluyente, se reduce significativamente la viscosidad de un caucho con un peso molecular muy elevado añadiendo, aproximadamente, un 28 % de aceite compatible. Para ello, se prepara una emulsión de aceite que se coagula con el látex de caucho. En el momento en que se rompe la emulsión, el aceite se transfiere cuantitativamente al caucho (sin que se detecte ningún aceite libre en ningún momento). El caucho con aceite diluyente permite mezclar fácilmente compuestos con cargas muy altas y mantener un elevado porcentaje de las propiedades finales.
Vulcanización por curativos fenólicos, derivados de benzoquinona o bismaleimidas
Los cauchos de dieno como el caucho natural, SBR y BR pueden vulcanizarse por la acción de compuestos fenólicos, que son (generalmente disustituidos por grupos -CH2-X donde X es un grupo -OH o un sustituyente de átomos de halógeno. el caucho de dieno también puede vulcanizarse por la acción de un dinitrosobenceno que se forma in situ por la oxidación de una quinonedioxima, que se había incorporado al caucho junto con el agente oxidante, peróxido de plomo. Otro agente vulcanizante para cauchos con alto contenido de dieno es la m-fenilenbismaleimida. Una fuente catalítica de radicales libres como el peróxido de dicumilo o el disulfuro de benzotiazilo (MBTS) se usa generalmente para iniciar una reacción de radicales libres. Aunque con frecuencia se usa una fuente de radicales libres con un agente de vulcanización maleimida, a temperaturas de vulcanización suficientemente altas, las maleimidas reaccionan con el caucho sin la necesidad de una fuente de radicales libres.
Designación
- Designación ASTM D1418: SBR
- ASTM D2000 / SAE J200 Tipo, clase: AA, BA
- Designación del Compuesto de Apple: SB
Mezcla de SBR
En general, las diferencias en la masticación y vulcanización entre el SBR y el caucho natural son menores. Un relleno de refuerzo es esencial para lograr buenas propiedades físicas en el SBR. Sin embargo, algunas cargas distintas del negro de humo lo refuerzan moderadamente bien. El SBR es compatible con los demás elastómeros principales y se puede utilizar en mezclas. Las técnicas de extensión de aceite y masterbatching se emplean ampliamente. Estas técnicas, así como el procesamiento de SBR en general. Las existencias de bandas de rodadura de llantas hechas de SBR regular son inferiores en resistencia a la tracción a las de caucho natural (3000 contra 4500 psi), mientras que las de "caucho frío" son casi equivalentes a Hevea (3800 psi). Sin embargo, a temperaturas elevadas, regular y "frío7 'SBR pierde casi dos tercios de su resistencia a la tracción mientras que el caucho natural pierde solo el 25%. La combinación de cauchos de estireno-butadieno para productos finales se analiza con más detalle en otras secciones de este manual. El caucho de estireno-butadieno moderno ya no requiere los repetidos ciclos de mezcla de productos anteriores. Sus propiedades de extrusión son superiores a las del caucho natural y sus cepas tienen menos tendencia a quemarse durante el procesamiento. El SBR frío es a menudo preferible al SBR caliente para obtener propiedades físicas óptimas debido a su menor peso molecular y menor grado de ramificación. No obstante, el uso de tipos ESBR calientes, cuando sea posible, puede contribuir tanto al procesamiento como a las mejoras del producto. Una mayor histéresis y acumulación de calor, una mala resistencia a la abrasión y al crecimiento de cortes, así como un mayor costo, disminuyen la utilidad del ESBR caliente, pero los materiales altamente cargados que no se utilizan en aplicaciones dinámicas pueden beneficiarse de sus ventajas de procesamiento. Para muchos usos, se fabrican mezclas de SBR y cauchos como caucho natural o cispolibutadieno. Las recetas de compuestos deben proporcionarse para equilibrar los requisitos para cada tipo de caucho utilizado. En la evolución hacia polímeros de rendimiento aún mejor, los polímeros de estireno-butadieno con la distribución de peso molecular más lineal y más estrecha se pueden producir solo mediante polimerización en solución. La macroestructura que le da a la solución SBR propiedades dinámicas tan útiles también da como resultado compuestos que son más difíciles de procesar. La solución SBR tiende a aumentar la viscosidad del compuesto Mooney y produce un compuesto con poca recuperación. Una variación de la solución SBR es la estructura acoplada al final de la cadena. Este procedimiento introduce una configuración en "estrella", que puede actuar como una ramificación de cadena larga en su efecto sobre la recuperación y el procesamiento. Estos polímeros parecen funcionar mejor en compuestos con bajos niveles de cargas. Se deben realizar cambios en las condiciones de procesamiento para obtener un procesamiento óptimo con la solución SBR.
Procesamiento de los compuestos de SBR
El procesamiento de los compuestos de SBR es similar al del caucho natural (u otro). Se utilizan los rellenos, plastificantes, antioxidantes y activadores normales. El SBR requiere menos azufre que el caucho natural y un poco más de acelerador. La emulsión SBR tiene un curado más lento que la solución SBR; por lo tanto, a menudo requiere el uso de un acelerador secundario, lo que puede no ser el caso con la solución SBR. El contenido de vinilo de la microestructura de butadieno también afecta la velocidad de curado. En la emulsión SBR, el contenido de vinil butadieno se fija al 23%. En solución SBR, el contenido de vinil butadieno puede variar desde el 10% hasta casi el 100%. El mayor contenido de vinilo retarda el curado y reduce la resistencia a la tracción, al alargamiento y al desgarro. Un vinil butadieno más alto en solución SBR aumentará la histéresis a la misma viscosidad de Mooney del polímero en bruto. Los sistemas de curado EV y semi-EV se utilizan a menudo con SBR. Estos tipos de sistemas de curado proporcionan excelentes propiedades envejecidas, pero no penalizan las propiedades de flexión no envejecidas, como es el caso del caucho natural. Los ingredientes para los compuestos de SBR se pueden mezclar en mezcladores internos o en molinos abiertos, y luego se pueden extruir, calandrar, moldear y curar en un equipo convencional. Los procedimientos de mezcla varían según el compuesto. El caucho natural a menudo se plastifica mecánica o químicamente para ayudar a su procesabilidad. Los peptizantes químicos tienen poco o ningún efecto sobre el SBR. La emulsión SBR a veces se mastica previamente en un mezclador interno antes de agregar otros ingredientes. Esto reducirá la viscosidad Mooney de la emulsión SBR, pero no tendrá ningún efecto sobre la solución SBR. Aunque los procedimientos de mezcla varían, el procedimiento general es mezclar caucho, óxido de zinc, antioxidante y ácido esteárico, luego agregar el negro de carbón en porciones con el suavizante o aceite (esto se considera un masterbatch negro). En este punto, puede ser deseable volcar, cubrir y enfriar el masterbatch. La segunda fase ahora incluye mezclar todos los demás ingredientes, y el acelerador y el azufre se agregan al final. Luego se continúa mezclando hasta que el azufre esté bien disperso.
Hay poca diferencia entre el SBR en emulsión y el SBR en solución con respecto a los tiempos de mezcla, temperaturas o niveles de dispersión. Remilling puede reducir la viscosidad Mooney de la emulsión SBR, pero tiene un efecto mínimo sobre la solución SBR. Tanto la emulsión como la solución SBR tienen versiones con aceite extendido que se pueden usar para ayudar a ajustar las viscosidades. La procesabilidad de los compuestos de SBR depende en gran medida de la fórmula. En muchos casos, el polímero en emulsión de peso molecular más amplio es útil para transportar el polímero en solución a través del sistema. Generalmente, cuanto mayor es la viscosidad Mooney del compuesto, más difícil es procesarlo. En los molinos de descomposición y calentamiento, estos compuestos pueden acumular calor muy rápidamente. Se recomienda un tiempo de quemado adicional del 10% al 25% para compuestos de mayor viscosidad. Estos compuestos también tienen tendencia a formar bolsas. Esto se puede aliviar ajustando el agua de enfriamiento al molino, ajustando la relación de fricción o reduciendo el espacio del molino. Las extrusoras de alimentación en frío se están volviendo muy populares porque evitan las dificultades de molienda. La velocidad de extrusión y el aspecto del extruido también dependen de la fórmula. Los ácidos grasos son excelentes agentes de liberación de metal a caucho, y pequeñas cantidades agregadas al compuesto pueden mejorar el proceso de extrusión. La extrusión dual de dos o más componentes se está volviendo popular como un medio para superar la baja pegajosidad verde de los compuestos SBR. La adición de pequeñas cantidades de caucho natural también mejorará la adherencia en verde. SBR no tiene la combinación de resistencia verde y adherencia verde del caucho natural. Aunque se ha desarrollado alguna solución SBR para abordar este problema, todavía se requiere algo de caucho natural para las carcasas de neumáticos radiales. Algunos SBR tienen la capacidad de conservar una forma excelente en productos extruidos y se utilizan en aplicaciones de vulcanización continua, como mangueras. El moldeo y la vulcanización se pueden lograr mediante métodos de compresión, transferencia o inyección. Los tres métodos producen productos satisfactorios. Los tiempos de moldeo son generalmente cortos en comparación con algunos polímeros especiales, pero son aproximadamente iguales o un poco más largos en comparación con el caucho natural. Otros tipos de procedimientos de vulcanización satisfactorios son el curado con vapor abierto, los sistemas de curado continuo (como el vapor continuo) y los trenes de sal líquida. También se utiliza el curado por microondas.
Aplicaciones de SBR
Originalmente, el SBR se usaba en neumáticos solo por necesidad, pero el SBR "frío" parece igual en la mayoría de los aspectos al caucho natural, especialmente para neumáticos de uso más ligero. Es inferior al producto natural para llantas de camión.Para muchos productos mecánicos, el SBR es superior al caucho natural y se usa preferentemente debido a su procesamiento más fácil y producto final de buena calidad.Estos artículos incluyen bandas, mangueras, productos moldeados, láminas no vulcanizadas, goma de mascar, y pisos Las suelas de caucho para zapatos están hechas de SBR Los productos extruidos y las telas revestidas son otros campos en los que el SBR ofrece ventajas en la procesabilidad Se usa ampliamente para aislamiento eléctrico, aunque sus propiedades no son tan buenas como las del caucho butílico.