Front end
Aplicaciones > ► Automotiriz > ► Bajo el capó
Front end modulus (FEM)
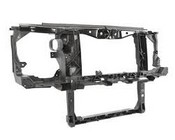
Las partes visibles son, según el modelo, los faros, la parrilla delantera y los parachoques. Detrás de estas piezas se encuentran el soporte frontal, los componentes del aire acondicionado del vehículo y el sistema de refrigeración del motor y de gestión de colisiones. La parte delantera de un vehículo es el conjunto de componentes ubicados en su parte delantera que realizan muchas funciones (estéticas, estructurales, aerodinámicas, refrigeración del motor, seguridad) y que se preensamblan como subconjunto listos para ser instalados en el vehículo. El Front end se basa en un portador estructural (en plástico con refuerzos metálicos locales) sobre el que se ensamblan los siguientes componentes principales:
- faros
- bloqueo del capó
- cuernos
- cubierta del ventilador
- radiador de agua
- condensador
- ventilador
- arnés de cableado
- viga de caja de choque
Además, para las versiones superiores, se pueden agregar los siguientes componentes:
- intercooler
- enfriador de aceite
- sensor de control de crucero
- sensor de choque
La parte delantera es una parte básica del chasis del vehículo y del estilo externo y debe cumplir las siguientes funciones:
- Estilo para hacer agradable la vista y el tacto de las diferentes superficies y el ajuste y acabado entre los componentes estéticos
- Seguridad activa que permite a través de los faros una visibilidad correcta en todas las condiciones ambientales y a través del sensor de control de crucero para mantener la distancia correcta con el vehículo precedente
- Seguridad pasiva que absorbe energía durante el choque y permite a través del sensor de choque la explosión oportuna de las bolsas de aire
- Protección de los demás usuarios de la vía (peatones, ciclistas) asegurando un espacio adecuado entre las superficies externas del vehículo y los componentes subyacentes
- Rigidez colaborando tanto durante la conducción como durante los choques para la función estructural del chasis del vehículo
- Aerodinámica y refrigeración llevando a cabo un flujo de aire óptimo tanto para el funcionamiento de los componentes del sistema de refrigeración del motor (durante la conducción a velocidad normal como a baja velocidad) y para el aumento de la permeabilidad
Materiales utilizados
Según el fabricante del automóvil, se utilizan diferentes materiales que incluyen:
- Poliamida 6 30% fibra de vidrio corta
- Poliamida 6.6 30% fibra de vidrio corta
- Polipropileno 35% fibra de vidrio corta
- Polipropileno 30% fibra de vidrio larga LFTR
- Poliamida 6 40% fibra de vidrio corta
Con el crecimiento de las plataformas mundiales, existe una divergencia de enfoque entre los europeos y los EE. UU. Y Japón. El diseño europeo clásico se vio a principios de la década de 1990 con respecto al uso de GMT en la gama de productos del Grupo Volkswagen. Esta moldura típica de 4 kg con un 40% de contenido de vidrio GMT se ha refinado y probablemente ahora esté más cerca de los 3 kg que de los 4 kg. Integrará mecanismos de cierre del capó, componentes de HVAC y sistemas de iluminación. La rigidez transversal del automóvil se obtiene mediante un simple prensado de metal que también puede actuar como una viga de parachoques en muchos vehículos pequeños. El SMC todavía se utiliza, especialmente en Francia, aunque las presiones competitivas por el ahorro de costes y peso de este segmento no apuntan a su uso continuo. En los EE. UU., El enfoque es mucho más hacia la extensión del panel de apertura de la rejilla para proporcionar más funciones mientras se retiene un travesaño de metal integrado. Esto se debe en parte a las actitudes estadounidenses hacia los requisitos de los parachoques. Los materiales utilizados en Europa se encuentran actualmente sometidos a un alto grado de presión competitiva. Varias formas de LYF (Termoplástico de Fibra Larga) han entrado en el mercado. Aunque el producto de entrada es diferente, el proceso final es el de moldeo por compresión, lo que permite la sustitución directa de GMT. Sin embargo, el contenido de vidrio parece estático a un máximo del 30%. El motor principal detrás de buscar el reemplazo de GMT por productos LFT es eliminar la forma de producto semi-terminado. La percepción es que GMT es un producto semi-terminado costoso, su tecnología tiene un alto costo de entrada y requiere un proceso de calentamiento secundario, que representa un costo secundario y un paso potencialmente dañino en el procesamiento. En términos simples, la idea es plastificar el polímero y dosificar en fibra de vidrio al final del barril causando el menor daño posible a las fibras. Otro tipo de El proceso LFT ha sido desarrollado por mediante el cual un tipo de pellet moldeado por inyección de fibra larga se plastifica para producir una masa seguida de un moldeado por compresión. El desarrollo, llevado a cabo en los EE. UU., Ha llevado a una pieza sin la función completa de un front-end, 3,2 kg de peso total con 2 kg de polímero. Este es fabricado por Visteon en los EE. UU. Y Dynamit Nobel en Europa. Para el futuro desarrollo de frontales basados en la tecnología de moldeo por compresión GMT, la clave parecería ser una mayor integración para incluir la hibridación como en el uso de componentes metálicos para proporcionar rigidez adicional, o utilizar sistemas híbridos GMT que han comenzado a comercializarse. disponible. El primero de ellos, basado en el hilo de vidrio de polipropileno está disponible y ya ha encontrado uso en sistemas de parachoques. Un área adicional de importancia son los cambios en la legislación europea con respecto a la seguridad de los peatones. Será posible diseñar interfaces, incluidas áreas de absorción de energía, para satisfacer las necesidades legislativas que comienzan en 2002.