Parachoques
Aplicaciones > ► Automotiriz > ► Exterior vehículo
Parachoques
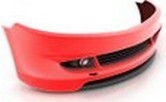
Historia
Frederick Simms inventó el parachoques de automóvil en 1901. Los primeros parachoques de automóvil estaban hechos de vigas metálicas unidas tanto a la parte delantera como a la trasera de un automóvil con el propósito de protegerlo en una colisión a baja velocidad.En ninguna parte se ha expresado mejor el potencial de diseño de los plásticos que en los parachoques de los automóviles. A principios de la década de 1970 se hizo evidente un importante rediseño y, a partir de entonces, el sector atrajo un mayor esfuerzo de desarrollo. Los cambios de estilo han sido bastante fundamentales, pero además de verse mejor, los vehículos de hoy son más eficientes aerodinámicamente y muestran una mayor tolerancia a los daños. Los componentes exteriores menores aparecieron por primera vez en plásticos durante la década de 1960. En 1925, los parachoques delanteros y traseros se convirtieron en equipamiento estándar en todos los coches. Lo que eran simples vigas de metal en ese momento se convirtieron en componentes de ingeniería complejos que son parte integral de la protección de vehículos en colisiones de baja velocidad. Los plásticos entraron en estas aplicaciones en la década de 1980 debido a ventajas como su apariencia estéticamente agradable, resistencia a la corrosión, ligereza de peso y facilidad de diseño. La tasa de expansión de los plásticos está delimitada por los metales, pero los diseñadores pueden solucionar esa deficiencia. Los parachoques no tienen que incluirse en la línea de ensamblaje con metales y, por lo tanto, se pueden pintar por separado y luego ensamblar en el vehículo más tarde. Los parachoques moldeados en color también se han considerado en el pasado, pero eran difíciles de combinar con el color del resto de los paneles exteriores de la carrocería. Versiones reformuladas con alto contenido de relleno de poliolefina termoplástica (TPO), acrilonitrilo-butadieno-estireno (ABS) y mezclas de policarbonato (PC)/ABS se encuentran en aplicaciones de parachoques en todo el mundo. Hoy, TPO domina este mercado en todo el mundo. Aparte de estos polímeros y mezclas, los termoendurecibles a menudo entran en este mercado como productos moldeados por inyección por reacción (RIM). De hecho, RIM fue el primer plástico aprobado para la fascia de parachoques en América del Norte para cumplir con la resistencia a choques a baja temperatura exigida por algunos fabricantes de equipos originales (OEM). Desafortunadamente, debido a la complejidad del proceso, RIM no se pudo fabricar a una velocidad lo suficientemente alta para satisfacer las demandas de las plataformas de automóviles grandes. El tiempo de ciclo más rápido para la producción de piezas está delimitado por la velocidad de la química de curado y la capacidad de la resina para fluir hacia los moldes. Además, la industria automotriz quería alejarse del uso de sistemas de polímeros termoendurecibles que no se pueden volver a fundir. Este atributo de los termoendurecibles fue etiquetado por la industria como no reciclable, y la industria dejó espacio para otros termoplásticos como el TPO que se pueden volver a fundir. Las piezas moldeadas por inyección y reacción están hechas de epoxis de uretano, poliésteres y poliamidas. Un estudio de costo versus desempeño informó que RIM ofrece la mejor característica de costo-desempeño para materiales compuestos y es competitivo con el acero.
Importancia
Los parachoques protegen equipos importantes de su automóvil, como faros, luces traseras, capó y sistemas de escape y enfriamiento. Todos estos componentes son costosos de reemplazar y un parachoques puede eliminar o reducir los costos de reparación.
Atributos
Los atributos de un buen parachoques de automóvil incluyen geometría, absorción de energía y estabilidad. Estos rasgos permiten que un parachoques se alinee al ras con un parachoques opuesto para absorber cualquier impacto y mantener la estabilidad.
Tipos
Si bien la mayoría de los parachoques tienen un diseño estándar para proteger los componentes importantes de un automóvil, algunos están diseñados con estilo. Este énfasis en el estilo a menudo reduce el parachoques, lo que resulta en una menor efectividad para resistir daños durante un choque.
Material de la cubierta del parachoques de plástico
Si va a realizar una reparación en la cubierta del parachoques, debe conocer el tipo de plástico que utiliza el fabricante de automóviles. Los fabricantes de automóviles utilizan una variedad de plásticos diferentes como policarbonatos, polipropileno, poliamidas, poliésteres, poliuretanos y olefinas termoplásticas o TPO para formar sus cubiertas de parachoques. Muchas cubiertas de parachoques contienen una combinación de estos diferentes materiales. Los fabricantes mezclan estos plásticos con fibras de vidrio u otros materiales para fortalecer el parachoques. Algunos plásticos requieren un promotor de adhesión antes de agregar cualquier material de relleno, imprimación o pintura, mientras que otros plásticos se pueden fundir juntos. Dos categorías de plásticos utilizados en parachoques.
Material de parachoques termoplástico
El material termoplástico está hecho de un polímero plástico que se vuelve blando, moldeable y moldeable cuando se calienta y se endurece cuando se enfría. Los materiales termoplásticos se pueden recalentar, reformar y remodelar varias veces sin ningún cambio en sus propiedades químicas o mecánicas. Cuando los termoplásticos se calientan hasta su punto de fusión, se derriten hasta convertirse en un líquido. Generalmente, los parachoques de los automóviles están hechos de una cubierta de plástico reforzada con una barra de acero, compuesto de fibra de vidrio, plástico o aluminio. Las principales resinas utilizadas son olefinas termoplásticas (TPO), policarbonatos, poliésteres, polipropileno, poliuretanos, poliamidas. Además de los soportes aplastables y una barra, los parachoques a veces incorporan espuma de polipropileno o termoplástico formado. Estos componentes adicionales actúan como espaciadores entre el parachoques y la barra, no como absorbentes de energía. Los parachoques modernos están hechos con una combinación de materiales. El primer elemento es un dispositivo de resorte que absorbe los impactos, generalmente cartuchos llenos de gas que montan el parachoques delantero al chasis. Esto permite que el sistema de parachoques absorba pequeños impactos sin ningún daño.
Material de parachoques termoestable
Un material de parachoques termoendurecido se fabrica mezclando dos o más componentes. Los dos componentes se entrecruzan durante el proceso de curado para formar un enlace químico irreversible. Masilla para carrocería (Bondo) y endurecedor y epoxis de dos componentes son ejemplos de plásticos termoendurecidos. Una vez catalizados, los plásticos termoendurecidos no se pueden fundir ni juntar para formar una reparación. En otras palabras, no puede usar solo calor para fusionar una grieta en una cubierta de parachoques de poliuretano termoendurecida. De hecho, si intenta usar calor para derretir y fusionar una grieta en una cubierta de parachoques PUR, el plástico en su lugar se licuará, burbujeará y humeará y se enfriará pegajoso al tacto. Esto se debe a que el material base se ha descompuesto con el calor.
Procesamiento
En cuanto al diseño y el aspecto de procesamiento, los parachoques son de gran tamaño, por lo que se procesan mediante técnicas como moldeo por inyección, moldeo por soplado y rotomoldeo. Teniendo en cuenta las técnicas de procesamiento anteriores, los plásticos son un material de elección adecuado. Teniendo en cuenta los métodos de procesamiento mencionados anteriormente, más comúnmente ABS, PC / ABS está moldeado por inyección y ABS moldeado por soplado se usa en automóviles. Cuando se procesa mediante rotomoldeo, el HDPE pulverizado se procesa fácilmente y se utiliza en la fabricación de parachoques. Los autos de algunas décadas atrás usaban acero y aluminio y usaban resortes o unidades hidráulicas para brindar protección y amortiguación, lo que permite que el parachoques absorba el impacto y permanezca relativamente intacto. En términos de estilo y practicidad, muchos fabricantes utilizaron caucho para absorber el impacto y proteger el parachoques de metal cromado. Preferí mucho esto a la moderna espuma de poliestireno y aluminio cubiertos de plástico. Los nuevos se raspan, agrietan y astillan por algo tan ligero como un coche que lo golpea mientras se estaciona.
Tipos de plásticos más comunes que se utilizan en las cubiertas de los parachoques
Poliuretano (PUR), Moldeo por inyección por reacción (RIM), Moldeo por inyección por reacción reforzada (RRIM), Poliuretano termoestable: más común en vehículos domésticos. De color amarillo o gris. Burbujas y humo cuando intenta derretirse. Las arenas PUR termoendurecibles son pulverulentas y se pueden alisar con un molinillo siempre que no se use alta presión o alta velocidad que haga que el plástico se licue. El PUR y la mayoría de los plásticos termoendurecidos se reparan mediante fusión por calor y esmerilado en una ranura en “V” y llenándolos con material de relleno de uretano y soporte estructural (pantalla de acero inoxidable) en la parte posterior del material agrietado.
Inyección de reacción (RIM)
El parachoques de un automóvil se fabrica mediante un proceso llamado moldeo por inyección de reacción (RIM), que básicamente consiste en fabricar un compuesto especial de poliuretano e introducirlo en una moldura de parachoques grande. RIM es un proceso que conserva las materias primas y reduce los costos. Es similar al moldeo por inyección, excepto que se utilizan polímeros termoendurecibles, que requieren que se produzca una reacción de curado dentro del molde. Los elementos comunes fabricados a través de RIM incluyen parachoques de automóviles, alerones de aire y guardabarros. En cuanto al parachoques del automóvil, es la parte más delantera o más trasera, aparentemente diseñada para permitir que el automóvil aguante un impacto sin dañar los sistemas de seguridad del vehículo. No son capaces de reducir las lesiones a los ocupantes del vehículo en impactos a alta velocidad, pero están cada vez más diseñados para mitigar las lesiones a los peatones atropellados por automóviles. En el proceso de fabricación de parachoques de automóviles, hay dos pasos. El primer paso es hacer un polímero. Los precursores de plástico líquido se mezclan con un catalizador que hace que se combinen y polimericen rápidamente. Luego, los materiales se vierten o inyectan en un molde grande, donde se combinan rápidamente. Y el siguiente paso es usar el molde del parachoques del automóvil. El resultado es un polímero de poliuretano. Con la ayuda de gas, el poliuretano se expande para llenar el molde del parachoques. A continuación, se retira el producto ligero.
Olefina termoplástica (TPO), olefina termo-elástica (TEO)
TPO y TEO son una combinación de polipropileno, un elastómero o caucho y un relleno mineral como el carbonato de calcio o el talco. El material de parachoques de TPO se lija en trozos, se derrite como mantequilla con molinillos de alta velocidad, se siente como cera y se vuelve fibroso cuando está caliente, así que tenga esto en cuenta cuando intente lijar o moler una cubierta de parachoques de TPO. Las cubiertas de parachoques de TPO son las más difíciles de reparar porque contienen de un 3% a un 5% de desmoldante a base de cera dentro del material. La cera incrustada dificulta la adherencia del relleno, el adhesivo, la imprimación y la pintura. Los talleres de carrocería prefieren desechar un parachoques TPO porque la reparación es muy difícil. Sin embargo, TPO ES reparable siempre que sepa cómo prepararlo. Debe usar un limpiador y promotor de adherencia antes de agregar cualquier material de relleno. TPO se usa ampliamente en el mercado automotriz: a medida que las capacidades de TPO crecen, las aplicaciones en las que se usa han seguido su ejemplo. El TPO se ha adaptado ampliamente para su uso en aplicaciones automotrices tanto exteriores como interiores, reemplazando materiales más tradicionales como el metal y otros termoplásticos de ingeniería. La fuerza impulsora detrás de este cambio de material es reducir el peso del automóvil.
Sin embargo, la estética siguen siendo una alta prioridad para aplicaciones de automoción, que a su vez ha dado lugar a mejoras de polímero con el fin de satisfacer el requisito de una superficie de clase A . Para satisfacer este requisito, las empresas de resinas han creado grados de polímero con un atractivo estético mejorado. La modificación de TPO con plastómeros a base de metaloceno en lugar de cauchos convencionales hace más que mejorar el impacto a baja temperatura y la fluidez: los plastómeros también pueden mejorar la adhesión de la pintura. Ahora, con las nuevas innovaciones de polímeros, los consumidores de la industria automotriz pueden aprovechar las propiedades de este polímero sin sacrificar el atractivo estético.
TPO está estabilizado a los rayos UV:
TPO necesita soportar cualquier cosa que la Madre Naturaleza le arroje, y en la parte superior de esta lista está la exposición a la luz ultravioleta. Hoy en día existen muchos grados de TPO disponibles que brindan esta protección UV. Los grados parabumpers, tienen paquetes de aditivos especiales que evitan que los colores personalizados se desvanezcan debido a la exposición al sol durante un período prolongado de tiempo. Estos avances en la tecnología de polímeros hacen de TPO la solución incomparable para piezas de exterior. Además de los grados estabilizados a los rayos UV, también se encuentran disponibles paquetes de aditivos que se pueden agregar durante la extrusión para mejorar aún más la longevidad del material.
basta de la estética de TPO; ahora vayamos al meollo de la cuestión y la única razón por la que TPO es el mejor material para los mercados que requieren durabilidad. TPO está diseñado para proporcionar el equilibrio óptimo de rigidez, impacto de temperatura fría y baja expansión térmica. Es ideal para aplicaciones donde la resistencia a la intemperie y la durabilidad en todas las condiciones es crucial. Estas cualidades son quizás la razón principal por la que este polímero ha encontrado un hogar en los mercados automotriz e industrial.
En ambos mercados, la pieza terminada estará expuesta al calor y al frío, y deberá mantener su forma al tiempo que permite una expansión o contracción térmica limitada. ¡Imagínese si en un caluroso día de verano el parachoques del automóvil comenzara a expandirse y agrietarse! ¡Eso sería completamente inaceptable! Entonces, a medida que las empresas automotrices comenzaron a pasar de los materiales metálicos tradicionales a materiales como TPO, evitar problemas como este estaba en la parte superior de su lista de requisitos al calificar los materiales de reemplazo.
Para darle una idea de si el TPO realmente puede competir con los metales en términos de durabilidad, esta prueba de Ford debería darle confianza: "La estricta especificación de impacto de baja temperatura de Ford requiere que el pilar no se agriete cuando se deja caer una bola de 10 libras sobre él desde 6 pies a -30°C".
El TPO se puede colorear durante la extrusión:
como se mencionó, el TPO está diseñado para soportar condiciones difíciles mientras mantiene el rendimiento. Si bien estas condiciones pueden exponer el material al desgaste, la estética, como los colores personalizados, sigue siendo una prioridad. Durante el proceso de extrusión, el TPO se puede colorear con cualquier color personalizado de su elección. Ya sea que tenga un objetivo de color que le gustaría combinar o un color PMS, uno de nuestros proveedores de color asociados superará las expectativas de cualquier mercado.
El TPO es retardante de llama:
debido a las dos aplicaciones más grandes de servicios de TPO (automotriz y techado), es esencial que este material sea retardante de llama. Aunque este polímero no es tan inherentemente resistente al fuego como los materiales de la competencia, esto se puede modificar agregando químicos y aditivos retardadores de fuego durante el proceso de composición.
¿El TPO es un polímero amorfo o cristalino?
Pensarías que esta sería una respuesta simple, pero no lo es. Debido a que la TPO es una olefina compuesta de caucho, esta pregunta se vuelve difícil y la respuesta depende de una variedad de factores, como el contenido de caucho, por ejemplo:“Si PP y PE son el componente dominante de una mezcla de TPO, entonces la fracción de caucho se dispersará en una matriz continua de polipropileno" cristalino ". Sin embargo, si la fracción de caucho es superior al 40%, la inversión de fase puede ser posible cuando la mezcla se enfría, lo que da como resultado una fase continua amorfa y una fase dispersa cristalina ".
El TPO es reciclable: el
TPO es un material 100% reciclable, pero debido a la naturaleza del material y a las aplicaciones de ciclo de vida prolongado en las que normalmente se utiliza, el flujo de reciclaje no es tan fuerte como debería ser. Sin embargo, ciertos mercados parecen estar descubriendo una forma de reciclar y reutilizar este material mientras ahorran dinero en el camino. En los últimos años, muchos fabricantes de TPO han iniciado programas para educar tanto a los contratistas de techos como a los propietarios de edificios sobre los beneficios y el proceso del reciclaje de TPO. El reciclaje de TPO no solo salva nuestro medio ambiente al reducir nuestra huella de carbono, sino que también ofrece incentivos financieros.
Polipropileno termoplástico
El PP es semiflexible, se derrite y mancha al moler, se siente ceroso o grasoso. Se repara mediante fusión por calor y esmerilado en una ranura en "V" y se rellena con material de relleno de polipropileno y soporte estructural (pantalla de acero inoxidable) en la parte posterior del material agrietado.
Los requisitos para el desempeño de los parachoques (de inglés "Bumpers"), parecerían dividirse en tres áreas de desempeño técnico separadas:
- Norteamericano - MVSS 215 / Part 581
- Europeo - EC42 sin daños a baja velocidad más seguridad para peatones, pruebas legislativas y de compañías de seguros
- Asiático - Legislativo para el hogar requisitos de mercado más exportación
En el contexto de los criterios técnicos, la parte delantera del parachoques integrado se está convirtiendo cada vez más en un problema de diseño y estilo. El front-end, en este contexto, no se refiere a los temas cubiertos, ya que son partes estructurales no cosméticas. Los ejemplos que demuestran la línea de estilo integrada en los modelos actuales. Técnicamente, Estados Unidos sigue comprometido filosóficamente con el espíritu de los requisitos de noMamage de 5 mph (8 kph). Debido a los grandes volúmenes involucrados en muchos de los modelos estadounidenses, una viga de metal con espumas de PP o PU que absorben energía siguen siendo los materiales de elección. Queda en duda si Estados Unidos hará un uso sustancial del potencial de ahorro de peso de los compuestos a largo plazo. Tanto los parachoques basado en SMC como en PP se utilizan, en general, para un volumen inferior (menos de 200.000 coches al año) como vigas de parachoques. Hasta finales de 1999 en Europa, podrá existir una diversidad de enfoques dado que los requisitos legislativos son mínimos. Sin embargo, a partir de este momento, la legislación sobre seguridad de los peatones tendrá un efecto dramático en toda la parte delantera de los vehículos, incluido el parachoques. En general, los sistemas de parachoques sobresalen menos de los automóviles europeos en comparación con sus homólogos estadounidenses o asiáticos. La dinámica de las diversas pruebas de impacto de peatones propuestas bajo las directivas europeas sugiere que la profundidad del parachoques para un sistema de parachoques europeo actualmente no conforme tendrá que aumentar al nivel de un sistema conforme (es decir 60-80 mm de aumento de sección) y, adicionalmente, esa cantidad aproximada de profundidad de material deberá agregarse, o incorporarse, en las áreas del capó y del alerón delantero. El potencial de los sistemas GMT e híbridos en la próxima generación de vigas de parachoques parece prometedor, ya que es posible ajustar las propiedades de la armadura para adaptarse a las características de impacto específicas necesarias para cada uno de los requisitos de protección de peatones, conservando la característica de no- dañar el sistema de parachoques a bajas velocidades. El uso de sistemas de parachoques de una pieza moldeados por soplado no ha tenido un éxito duradero. Sin embargo, existe un interés considerable en las aleaciones moldeables por inyección más nuevas, como PC / PBT, PPO / PA, porque tienen potencial para pintarse en línea, con la tendencia de poder pasar por el proceso de recubrimiento electrónico.