Conductos de aire
Aplicaciónes > ► Automotriz > ► Bajo el capó

Conductos de aire
En la industria automotriz existe una mayor demanda de sistemas de propulsión para ofrecer una mejor economía de combustible, una mayor eficiencia y reducir las emisiones. La tendencia a mejorar la eficiencia del motor con una mejor economía de combustible y un aumento en la potencia del motor se debe mucho a la tecnología de turbocompresor. El aumento en el rendimiento y la eficiencia del motor da como resultado altas temperaturas y gases más agresivos, a menudo bajo alta presión. Se espera que los sistemas de gestión del aire, como los conductos de aire, las mangueras del turbocompresor y los sellos, resistan estas altas temperaturas hasta un pico de 250°C. Los metales como los aluminios y ciertos tipos de cauchos pueden soportar estas altas temperaturas, pero el diseño asociado con estos materiales a menudo incorpora un mayor peso, parámetros de procesamiento complejos y múltiples números de pieza. Son materiales ecológicos o no ecológicos. Por lo tanto, el desafío radica en los materiales de metal y caucho que pueden ofrecer rendimiento, pero no flexibilidad de diseño ni simplicidad durante el proceso de ensamblaje. Los fabricantes de automóviles se están moviendo rápidamente hacia elastómeros de copoliéster termoplástico para la producción de nuevos conductos de aire resistentes a altas temperaturas. Los elastómeros de copoliéster termoplástico también están facilitando a los fabricantes la producción de conductos de aire (de inglés air ducts) en un solo material y utilizando un solo proceso. El enfoque en la reducción de peso y costos, mientras se mejora la eficiencia del proceso, se encuentran entre los factores clave que continuarán respaldando la adopción de elastómeros de copoliéster termoplástico en las industrias de uso final. Los copoliésteres también están reemplazando rápidamente al caucho y los metales en la fabricación de productos eléctricos, de consumo y médicos. Los copoliésteres también están reemplazando materiales como el PVC y el caucho de silicona en los dispositivos médicos, dijeron las autoridades. La demanda de elastómeros de copoliéster termoplástico probablemente se beneficie de desarrollos más amplios en la industria automotriz, especialmente el creciente enfoque en mejorar la eficiencia del combustible. Una solución de material que puede soportar altas temperaturas y soportar vibraciones, es compatible con el medio ambiente, ayuda a reducir el peso del motor y es ecológico es el material ideal que puede ayudar a los ingenieros a superar los desafíos de diseño que a menudo se enfrentan al trabajar con materiales de metal y caucho. TPC de alta temperatura (copoliéster termoplástico) establecen nuevos estándares en aplicaciones de conductos de aire flexibles de alta temperatura. Los TPC de ingeniería avanzada TPC-ET HT amplían la capacidad de temperatura del TPC tradicional al ofrecer una temperatura máxima de 190°C y una capacidad de temperatura de funcionamiento de 175°C, mucho más allá de la capacidad de los materiales TPC que se colocan tradicionalmente para aplicaciones de conductos de aire. Este material ofrece un rendimiento de envejecimiento por calor a largo plazo y una sólida resistencia química; por lo tanto, los conductos de alta temperatura se pueden hacer a partir de una solución de un solo material. Al usar un material, hay menos posibilidades de fugas debido a que hay menos piezas y áreas de conexión. Una solución de un solo material también hace que sea más fácil y rápido de procesar, lo que equivale a una ventaja de costo del sistema y una reducción de peso de hasta un 50%. TPC-ET HT también ofrece flexibilidad y mecánica incluso a baja temperatura. Este material eleva el punto de referencia de rendimiento de los TPC resistentes a la temperatura que proporcionan:
- Resistencia al calor mejorada
- Flexibilidad para cubrir los movimientos del motor en una solución de una sola pieza
- Peso reducido en comparación con el caucho y el metal.
- Solución de TPC moldeada por inyección / soplado único
Los conductos de aire sucios conducen el aire antes del filtro de aire, mientras que los conductos de aire limpio se encuentran en el motor entre el filtro de aire y el turbocompresor. Un conducto de aire transporta el aire necesario para la combustión del combustible en un automóvil. Es un sistema complejo que transporta el aire a través de un filtro al colector en la parte superior del motor. En el caso de los motores diésel se utilizan un turbocompresor y un enfriador de aire se pueden encontrar tres tipos básicos de conductos:
• Conductos de aire cargados (solo en combinación con turbocompresores) que deben funcionar a 1,8-2,2 bar y 150-175°C con aire contaminado por aceite.
• Conductos de aire cargados que ven la misma presión pero temperaturas más bajas de 60-100°C.
• Los conductos de aire limpios ven a veces picos de alta temperatura. Estos conductos de aire funcionan a una presión de -200 mbar
TPC de alta temperatura (copoliéster termoplástico)
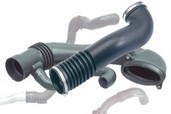
Los elastómeros termoplásticos de copoliéster demandan un crecimiento como sustituto del caucho-plástico y del caucho-metal.
Este material eleva la referencia de rendimiento de los TPC-ET resistentes a la temperatura que proporcionan:
- Resistencia al calor mejorada
- Flexibilidad para cubrir los movimientos del motor en una solución de una sola pieza
- Peso reducido en comparación con el caucho y el metal Solución de TPC moldeada por inyección / soplado único
XFLEX (TPC-ET) se utiliza en el conducto de aire de carga caliente moldeado por soplado y succión 3D. El conducto TPC-ET, tambien reemplazó una manguera de goma termoestable y un conjunto híbrido de plástico rígido, lo que redujo significativamente el peso, el costo y la complejidad del diseño del sistema de turbocompresor del vehículo.
Tecnología de moldeo por soplado
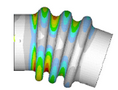
- componentes de plástico del capó
- circuitos de alimentación y refrigeración del motor
- conductos de aire acondicionado
- tubos de ventilación del sistema del motor
- circuitos de enfriamiento de aceite
- tanques y tubos de enfriamiento de motores
- tubo de suministro de combustible
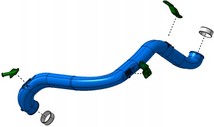
Conducto de aire de carga unido por inyección
A medida que aumentan las temperaturas y presiones debajo del capó, los conductos de aire de carga merecen resinas de mayor rendimiento y una fabricación más eficiente. Un buen ejemplo es un conducto moldeado a partir de dos grados de resina de sulfuro de polifenileno lineal (PPS) reforzado con vidrio corta. Inicialmente hecho en aluminio, las primeras iteraciones de plástico de este conducto de aire de carga involucraron el moldeado por soplado diseñado del complejo tubo de aire de carga en un conjunto de herramientas; luego moldeo por inyección por separado clips, orejetas y soportes de fijación en otro juego de herramientas; y finalmente unir las piezas moldeadas por inyección al tubo moldeado por soplado a través de una placa caliente o soldadura por vibración, lo que requería otro accesorio más. Se desarrolló un proceso híbrido único y ahora patentado de "ensamblaje en molde". Combina tres pasos de producción anteriores (moldeo por soplado, moldeo por inyección y soldadura) en un solo proceso secuencial (usando una o más herramientas, según la complejidad de la pieza). Esto elimina las operaciones de ensamblaje posteriores al molde y los desechos resultantes porque es más fácil mantener las tolerancias de posicionamiento que con las operaciones de soldadura posteriores. El proceso único también aumenta la R&R y mejora la confiabilidad de la unión, haciéndolo un 20 por ciento más fuerte que un ensamblaje soldado convencionalmente.
Proceso de soplado
Esencialmente, el proceso comienza como el moldeo por soplado convencional. Un parisón cae y se infla. Se expande hacia afuera, entra en contacto con las paredes de la cavidad de la herramienta y se congela para formar una estructura hueca. A continuación, una unidad de inyección integrada dispara las lengüetas de sujeción contra el parisón expandido y aún caliente, creando una unión de alta resistencia entre la tubería y sus elementos funcionales antes del desmoldeo. A medida que entran en contacto con el parisón caliente, las orejetas se unen química y mecánicamente con el tubo, produciendo una junta más fuerte y limpia. Dependiendo de la complejidad de la pieza final y la cantidad de integración de piezas secundarias que se desee, existe una variante de proceso que implica el uso de una segunda herramienta de inyección. Por ejemplo, cualquier accesorio agregado al tubo durante el moldeo por soplado inicial debe colocarse en la línea de separación de la herramienta para estar en la línea de dibujo cuando se abre la herramienta. Para moldear componentes adicionales en una orientación fuera del plano de la línea de separación, el tubo portador primero se forma en una herramienta, que luego se abre, y la parte aún caliente se mueve rápidamente a una segunda herramienta de inyección, que cierra e inyecta el componentes funcionales restantes. En esta configuración, la parte portadora debe estar diseñada para permitir la fusión parcial de su superficie en la región donde se inyectan los componentes adicionales para asegurar una fuerte unión. Para situaciones en las que se desea una alta automatización y menos pasos de proceso y herramientas, es preferible la versión más sencilla de una sola herramienta. Sin embargo, cuando una mayor flexibilidad de diseño mejora la funcionalidad de la pieza, la variante con la segunda herramienta de inyección es la mejor opción. Independientemente de la opción que se seleccione, ambas soluciones mejoran la fuerza de unión y ofrecen ahorros de costos en comparación con los métodos de moldeo convencionales con soldadura post-moldeado. Dado que la parte representa el lado caliente del tubo de carga de aire, se usaron dos grados diferentes de PPS reforzado con fibra de vidrio porque cada proceso requiere material con diferentes viscosidades de fusión. El PPS aporta una excelente estabilidad dimensional y una fluencia extremadamente baja, un coeficiente de expansión térmica lineal (CLTE) comparable al del aluminio, retardo de llama inherente, alta dureza y rigidez a temperaturas elevadas (hasta 240°C), excelente resistencia a la corrosión bajo el capó químicos automotrices, baja absorción de humedad y facilidad de procesamiento. El conducto de Mexpolimeros reemplazó una manguera de goma termoestable y un conjunto híbrido de plástico rígido, lo que redujo significativamente el peso, el costo y la complejidad del diseño del sistema de turbocompresor del vehículo.