Materiales para engranajes
Aplicaciónes > ► Industrial
Materiales para engranajes
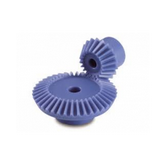
Aditivos
lubricantes
Entre
los
lubricantes
ampliamente usados
tenemos
el
polvo de
PTFE (polytetrafluoroethylene) y
fluido
de silicona. Las
partículas de PTFE manchan el contacto entre las superficies de
desgaste dando como resultado
una película
de PTFE
que se transfiere
a la superficie
de desgaste del
acoplamiento. Esta película
de
PTFE contra PTFE resulta
en coeficientes de
fricción
y regímenes de desgaste significativamente
reducidos Por
ejemplo,
cuando el PES
(polyethersulfone)
es lubricado con un 20% de PTFE, el coeficiente
dinámico de fricción disminuye de 0,37 a 0,11 y el factor
de desgaste baja
de 1500 a 32.
Con un factor de desgaste muy por debajo
de 200 esta resina amorfa
puede
ser
considerada
ahora
como
un
candidato
potencial
para engranajes. Las resinas amorfas son
importantes porque tienen una relación de contracción
en el molde más baja que las resinas cristalinas y
puede moldearse para
producir engranajes más exactos. Otro lubricante popular, el fluido de
la
silicona, emigra a la interfase
de desgaste y está
presente en el
arranque. Este lubricante
se emplea solo o junto con el PTFE para
reducir aún más el
factor de desgaste. El factor
de desgaste de un Nylon 6/6 lubricado
con un 2%
de silicona, Una
combinación
de
18%
PTFE
y
2%
de
silicona
reduce
el
factor
de
desgaste, más
allá,
hasta 6.
La combinación
de
PTFE/silicona
ofrece
mejoras
a
altas
velocidades
y
a
menudo
se
selecciona
para
las
aplicaciones
donde ocurren
oscilaciones
de velocidad
o en el
movimiento.
Refuerzos
El
refuerzo con
fibras
de carbono proporciona
la
mayor mejora
en
la
fuerza mecánica y
rigidez
seguidas por las
fibras de vidrio y
por
último las fibras del aramid. Con solo la adición de refuerzos de fibras
disminuye significativamente el factor
de
desgaste
de
la
mayoría los
sistemas de
resinas. La combinación
de PTFE y los
refuerzos de fibra
producen una reducción extensa en el factor
de desgaste. Para un Nylon 6/6 lubricado con
un15% PTFE y reforzado con
fibras
típicas (30% para vidrio y carbono,
10% para el
aramid) los factores
de desgaste se
reducen a menos de 20. La desventaja principal
de las fibras de vidrio
y carbono es que ellos
inducen una contracción
anisotrópica
en el molde, lo que
podría producir
engranajes menos precisos.
Las
fibras
de Aramid
se
comportan
más
isotrópicamente, con un
pequeño
diferencial
entre contracción en la
dirección del
flujo y transversal a él. Las
formulaciones
compuestas con
un
mínimo
de
fibras
de refuerzo
pueden
mejorarse con rellenos como
vidrio
molido o rosarios de
vidrio
que no aumentan la contracción diferencial. Sin embargo,
estos materiales
generalmente tendrán más bajas
propiedades
mecánicas y los
regímenes de desgaste más
altos. Uno de los progresos
en compuestos reforzados
que ofrecen un potencial
para el crecimiento
de la
sustitución de engranajes de metal es el empleo
de la
tecnología de
fibra
larga. Una comparación de las propiedades
del uso de las
fibras vidrio largas y
cortas para el poliamida 6.6 con un 40% fibras de
vidrio
y 10% PTFE revela mejoras
significativas
en los
esfuerzos de flexión
e impacto para el
refuerzo de fibra
larga.
El
régimen
de
desgaste
no
aumenta
dramáticamente
ya
que
el
número de extremos de fibra
se reduce.
Los altos
esfuerzos y propiedades de impacto se traducen
en la
mejora de la fuerza del
diente y resistencia a
la
fatiga bajo un alto torque logrado
en algunas
aplicaciones
del engranaje.
Efecto del Material sobre la Precisión del Engranaje
La selección del
material puede tener
un efecto apreciable sobre
precisión del engranaje.
Las
resinas
amorfas
tienen
características
de
contracción
que
tienden
a
ser más isotrópicas
que las resinas
cristalinas,
y los rellenos particionados se
comportan
más
isotrópicamente
que
los
fibrosos.
Si
se conoce
bien
el comportamiento de contracción de un material,
entonces la cavidad
del molde puede
ser
tallada
para moldear
un
engranaje
preciso,
para ese
material.
No obstante,
la contracción isotrópica es más fácil
de compensar al
tallar una cavidad para
engranajes. Para evaluar los
efectos de diferentes
resinas
y sistemas de
relleno
sobre la
precisión
de engranajes
moldeados
fueron
inyectados
varios
compuestos termoplásticos
para obtener un engranaje
cilíndrico de dientes rectos con 32 de diametral pitch, 20° de
ángulo
de presión, 1.25" de
diámetro de paso, y 0.125" de ancho,
integralmente
moldeado con
un
piñón
más pequeño. El
engranaje
tenía una sola entrada fuera de centro,
en la trama del
engranaje. Las resinas
bases seleccionadas
fueron poliamida 6.6 y
el
policarbonato. Estos materiales
para engranajes,
que son comúnmente usados, representan
a los
dos
tipos
principales
de
resinas
termoplásticas:
los
materiales
cristalinos
de alta contracción
(nylon, acetals,
y olefins) y
a los compuestos amorfos de baja contracción
(polycarbonates,
polysulfones,
ABS y
SAN).
Las
condiciones de moldeo
usadas
fueron
las
típicas
para
cada
resina
y
se
mantuvieron
constantes sin
tener
en cuenta el
tipo de relleno
o contenido. Para
cada
una
se
moldearon
formulaciones
con un
40%
de
fibras
de
vidrio
reforzado,
un 30% de rosarios de
vidrio
redondeados y un 30% fibras
de vidrio lubricados con
un15% PTFE. Para
ambas
resinas
bases,
las
formulaciones
con
fibras
de vidrio
reforzadas mostraron
una
sola
cresta
grande.
Esta cresta
es
una
gran mancha
en el
engranaje, y es el
resultado de una gran orientación de la fibra
en el lado del engranaje
opuesto a la
entrada. Los
compuestos de Nylon 6/6 rellenos
con rosarios
de vidrio
también mostraron una
sola cresta, pero la
magnitud de la cresta
es menor comparada con la
de relleno con
fibra
de vidrio reforzada. Esto
es que porque los
rellenos particionados se
contraen
isotrópicamente
y
su
alineación
en
el
lado
más
lejano
del
engranaje es irrelevante.
La cresta en este compuesto se debe a la
naturaleza anisotrópica
de
los
materiales
cristalinos.
Los compuestos
de
policarbonato
rellenos
con rosarios
de
vidrio
se
contrajeron
esencialmente
de
forma
isotrópica
y
dan
una curva
plana.
Este compuesto produjo
el
engranaje más preciso. La gráfica de
TCE para los
compuestos con un 30% fibra
de vidrio, lubricados con
un15%
PTFE mostraron una sola cresta, similar los compuestos
con un 40% de fibras
de vidrio
reforzado.
La adición del
PTFE a un compuesto reforzado
con vidrio tiene
poco efecto sobre el
runout. Dos
aspectos
importantes
a
tener
en
cuenta
además
de
las
propiedades mecánicas
para
la
selección de
un
material
plástico
son
la
absorción
de
humedad y
el
efecto de la temperatura.
La firma Intech ha investigado
la influencia de estos parámetros
en la
resistencia de los dientes,