Aleacion
Mezclas y Aleaciones
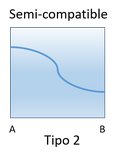
Razones del mezclado
El número de polímeros que pueden servir de base para las mezclas es extenso y por lo tanto las combinaciones posibles son innumerables. Dicha abundancia no sólo refleja la complejidad de los problemas que hay que superar para llegar a crear materiales útiles, sino también revela que estamos en presencia de una disciplina todavía en plena evolución. En general las razones del mezclado pueden ser las siguientes:
• Incrementar el volumen de una resina de ingeniería con un polímero de bajo costo
• Desarrollar materiales con varías propiedades deseadas de los polímeros empleados
• Formar una mezcla de alto desempeño al interactuar los polímeros sinergísticamente
• Ajustar la composición de la mezcla a especificaciones del cliente
• Reciclar desechos plásticos ya sean industríales o municipales
Blends
Alloy
Es posible modificar algunas propiedades de polímeros deficientes en una aleaciones, también llamadas blend o alloy. Cuando los polímeros son compatibles con la matriz, las propiedades resultantes se estudian para aplicaciones especiales. Al controlar la formulación del material, se puede lograr una propiedad equilibrada con efecto sinérgico. Las mezclas, también se llama aleación, alloy o blend, en comparación con los procesos de síntesis y modificación química, presentan una grande ventajas, por eso proliferan los trabajos de investigación sobre mezclas, en la actualidad existen miles de patentes registradas y cientos de mezclas en desarrollo. Los Blends son desarrollo de formulaciones para predecir el comportamiento de la capacidad de combinarse de dos o más polímeros. Las mezclas de polímeros permiten la obtención rápida y económica de nuevos materiales con mejores características que los materiales individuales.
La mezcla puede mejorar el rendimiento de la resina o del producto al:
- Producir materiales que tengan un conjunto completo de las propiedades deseadas al menor costo.
- Ampliar el rendimiento de las resinas de ingeniería mediante la incorporación de polímeros menos costosos.
- Mejora de propiedades específicas.
- Endurecimiento de polímeros frágiles, eliminando así la necesidad de usar aditivos de bajo peso molecular (por ejemplo, plastificante en el material flexible).
- La mezcla con resina más rígida y más resistente al calor puede conducir a un módulo mejorado y una estabilidad dimensional.
- Incorporación de polímero semicristalino en una resina amorfa para mejorar el solvente y resistencia química (p. ej., en mezclas de PC con PEST).
- La incorporación de resina no inflamable en una resina inflamable mejora la resistencia al fuego (por ejemplo, estirénicos o acrílicos con PVC).
- Mezclas con polímeros que tienen –OH o - La funcionalidad SH conduce a mezclas permanentemente antiestáticas (por ejemplo, óxido de etileno-coepiclorhidrina con mezcla ABS / PC).
- Materiales biodegradables producidos mediante la incorporación de una resina biodegradable.
- La fusión permite producir estructuras integradas de múltiples capas.
- Proporcionar medios para el reciclaje de residuos plásticos industriales y / o municipales.
- La tecnología de mezcla permite reconstruir altos pesos moleculares de polímeros parcialmente degradados, para así producir artículos de alto rendimiento a partir de los residuos plásticos.
La mezcla puede conducir a una procesabilidad mejorada:
- La incorporación de una resina miscible con una temperatura de transición vítrea (Tg) más baja permite procesar la alta Tg resina a temperaturas muy por debajo del límite de degradación térmica (p. ej., mezclas de PS / PPE).
- La incorporación de una resina inmiscible de baja viscosidad permite reducir la caída de presión a través de matrices o guías, aumentando así la productividad (por ejemplo, mezclas LCP / PEEK).
- La mezcla con resina que por sí sola muestra un alto endurecimiento por deformación (SH) (p. Ej., LDPE en mezclas con otro PO), o cuando se mezcla reactivamente forma ramas de cadena larga (p. Ej., PS en mezclas con PO) da como resultado mezclas que tienen un control grado de SH. Estos materiales muestran una mejor procesabilidad en tecnologías.
- donde el campo de flujo extensional es importante, a saber, soplado de película, moldeo por soplado, recubrimiento de alambre, espumado, etc.
- La incorporación de partículas elastoméricas mejora la nucleación de las burbujas de gas, por lo tanto, estabiliza el proceso de formación de espuma, reduce el tamaño de la burbuja y la densidad final de la espuma.
- La incorporación de una resina degradable en una ingeniería o especialidad proporciona los medios para generar una cantidad controlable del gas espumante durante las siguientes etapas de procesamiento, a saber, moldeo por inyección.
- La mezcla de diferentes grados de la misma resina amplía la distribución del peso molecular, lo que a su vez resulta en un procesamiento más fácil y estable (así como un mejor rendimiento mecánico).
- La mezcla mejora la uniformidad del producto (reducción de chatarra) y la economía de la planta.
- La mezcla determina cambios rápidos de formulación, por lo tanto, flexibilidad y productividad de la planta.
- La mezcla reduce la cantidad de calificaciones que necesita ser fabricado y almacenado.
- La tecnología de mezcla ofrece métodos para producir materiales de mayor valor estético, por ejemplo, películas o recubrimientos sin partículas de gel (o “Ojos de pescado”), molduras con acabado superficial sin rayas, etc.La mezcla reduce la cantidad de calificaciones que necesita ser fabricado y almacenado.
- La tecnología de mezcla ofrece métodos para producir materiales de mayor valor estético, por ejemplo, películas o recubrimientos sin partículas de gel (o“Ojos de pescado”), molduras con acabado superficial sin rayas, etc.
- El flujo de masa fundida puede incrementarse agregando un polímero más fluido, o algunas veces un polímero inmiscible.
- La resistencia a la fusión y la elasticidad pueden incrementarse agregando un polímero de alto MW o uno con ramificación de cadena larga. El módulo de caucho se puede aumentar agregando un plástico rígido miscible. El módulo de un plástico rígido puede reducirse agregando un caucho miscible para que actúe como plastificante polimérico.
- La resistencia del caucho se puede aumentar agregando un plástico rígido.
- La resistencia a la abrasión se puede aumentar agregando polvo de PTFE o mezclando con caucho de poliuretano.
- La temperatura de deflexión térmica se puede aumentar al mezclar con un polímero miscible de mayor HDT.
- El retardo de la llama se puede aumentar al mezclarlo con un polímero halogenado como el PVC.
Propriedades
La blends de PC/ABS han pobre resistencia química y la estabilidad térmica son los principales inconvenientes. El caucho de butadieno en ABS sufre un envejecimiento químico bajo radiación UV que disminuye las propiedades mecánicas y cambia el color. El terpolímero ASA en el que el caucho de butadieno en ABS se reemplaza con caucho acrílico resuelve el problema de la degradación del butadieno.
Compatibilidad
Son las que presentan una fase finamente dispersa y buena adhesión entre las mismas, normalmente son homogéneas a nivel macroscópico y comercialmente atractivas. Básicamente hay tres tipos diferentes de mezclas dependiendo de la miscibilidad.
- Mezclas compatibles
- Mezclas parcialmente compatibles
- Mezclas incompatibles
Las mezclas de polímeros pueden ser clasificadas desde el punto de vista termodinámico siguiendo el criterio de energía libre ΔG en :
Mezclas miscibles ΔG < 0
Involucran solubilidad termodinámica y se caracterizan por la presencia de una fase y una sola temperatura de transición vitrea. Las propiedades de la mezcla corresponden, a grandes rasgos, a la adición de las propiedades de los polímeros de partida.
Mezclas miscibles ΔG > 0
Son de dos o más fases separadas, exhibiendo las temperaturas de transición vitrea y/o las temperaturas de fusión de cada componente de la mezcla. El desempeño no es predecible con facilidad.
Mezclas compatibles
Son las que presentan una fase finamente dispersa y buena adhesión entre las mismas, normalmente son homogéneas a nivel macroscópico y comercialmente atractivas. Las mezclas completamente miscibles tienen ΔH** m <0 debido a interacciones específicas. La homogeneidad se observa al menos a escala nanométrica, si no a nivel molecular. Este tipo de mezclas muestra solo una temperatura de transición vítrea (Tg), que está en entre las temperaturas de transición vítrea de los componentes de la mezcla en estrecha relación a la composición de la mezcla. Un ejemplo conocido de una mezcla que es miscible en un rango de temperatura muy amplio y en todas las composiciones es PS / PPO.
**ΔH (entalpía) es independiente del peso molecular y es una medida del cambio de energía asociado con las interacciones intermoleculares.
Mezclas parcialmente compatibles
Parcialmente compatible donde solo una pequeña parte del componente de mezcla se disuelve en la otra parte. Este tipo de mezcla, que presenta una morfología de fase fina y propiedades satisfactorias, se conoce como compatible. Ambas fases de mezcla son homogéneas y tienen su propia Tg. Ambas Tg se desplazan de los valores para componentes de mezcla puros hacia la Tg del componente de mezcla. Un ejemplo son las mezclas de PC / ABS. En estas mezclas, la fase PC y SAN del ABS se disuelve parcialmente entre sí. Esta interfaz es amplia y la adhesión interfacial es buena.
Mezclas incompatibles
Son mezclas con una marcada separación de fases y con propiedades muy pobres que no tienen aplicación comercial directa. Son blends con una marcada separación de fases y conpropiedades muy pobres que no tienen aplicación comercial directa. Interfaz nítida y poca adhesión entre las fases de mezcla. Sé que estas mezclas no sirven de nada sin compatibilización. Las mezclas exhibirán diferentes Tgs correspondientes a la Tg de los polímeros componentes. Ejemplos de mezclas completamente inmiscibles son PA / ABS, PA / PPO, PA / EPDM y PA / PP. Ahora estas mezclas se han vuelto comercialmente exitosas, después de ser eficientemente compatibles usando compatibilizadores adecuados.
Mezclas compatibilizadas
Son también llamadas aleaciones, y resultan de las mezclas incompatibles que mediante otro compuesto o una técnica de procesado se obtiene una morfología estable la cual puede ser aplicada comercialmente.
Compatibilización
La compatibilización es muy útil para mejorar la dispersión en mezclas de polímeros, reduce la tensión interfacial, facilita la dispersión, estabiliza la morfología contra tensiones y tensiones abusivas (que surgen del procesamiento), mejora la adhesión entre fases y mejora las propiedades mecánicas generales de los productos. Las fuerzas impulsoras para la segregación de fase de los componentes de la mezcla son la gravedad y la tensión interfacial. Son también llamadas aleaciones, y resultan de las mezclas incompatibles que mediante otro compuesto o una técnica de procesado se obtiene una morfología estable la cual puede ser aplicada comercialmente. En el caso de las mezclas de PC y estireno-acrilonitrilo (SAN), se requiere compatibilidad para las mezclas de PC/ABS, PC/PET, PA/ABS, PET/PE y PC/ASA para mejorar la energía de interacción. La PC y el ABS no son miscibles y requieren grupos de polarización para disminuir la tensión interfacial entre las fases.
Propriedades
- Incrementar el volumen de una resina de ingeniería con un polímero de bajo costo
- Desarrollar materiales con varías propiedades deseadas de los polímeros empleados
- Formar una mezcla de alto desempeño al interactuar los polímeros sinergísticamente
- Ajustar la composición de la mezcla a especificaciones del cliente
- Reciclar desechos plásticos ya sean industríales o municipales
Gama de productos
- PC/ABS
- PC/PET
- PC/PBT
- PA/PP
- PA/PE
- PET/PE
- PC/ASA
- PBT/ASA
Métodos de preparación de mezclas
La preparación de las mezclas de polímeros puede ser llevada a cabo mediante diferentes técnicas, algunas de las cuales se discuten a continuación
Mezclado mecánico
los materiales, ya sea en polvo o en gránulos, se alimentan a un equipo de mezclado el cual ejerce esfuerzos de corte asegurando una distribución uniforme a temperaturas superiores a las de fusión de los polímeros involucrados y posteriormente la mezcla resultante se granula. Éste es el método comercial predominante para la preparación de mezclas.
Mezclado en solución
Los polímeros se disuelven en un cosolvente y posteriormente por evaporación del disolvente se forma una película. El mezclado en solución reduce la probabilidad de degradación térmica de los polímeros, ya que se lleva a cabo en un disolvente a bajas temperaturas y bajos esfuerzos de corte. La contaminación de la mezcla con disolvente residual y la separación potencial de fases o la precipitación selectiva, son algunos de los riesgos de este método de preparación.
Coprecipitación de los polímeros
Los polímeros se disuelven en un cosolvente como en el mezclado en solución y después se coprecipitan al agregarlos en un recipiente que contiene otro compuesto (no solvente). Al obtenerse mezclas por medio de coprecipitación se obtiene un producto bastante homogéneo, ya que se promueve el entrelazamiento entre las moléculas de los polímeros.
Compatibilización
Pocos pares de polímeros forman mezclas miscibles y la razón de por qué no se mezclan es la entropía. La entropía gobierna ampliamente en un polímero amorfo. Entropía es el nombre que los científicos le dan al desorden. Por las bajas entropías de mezclado, la mayoría de los polímeros son inmiscibles, la clave para realizar mezclas exitosas de este tipo, es el empleo de la compatíbilización. La compatíbilización puede involucrar la adición de otro componente, usualmente un polímero bi-funcionalizado o la aplicación de un proceso o una técnica deprocesado. Sólo unos pocos pares de polímeros se mezclan la mayoría no. Pero también existen pares de polímeros que a veces se mezclan y a veces no. Las variables que uno puede controlar para hacer que se mezclen o no, son generalmente la temperatura y la composición.
Compatibilización Física
En la mezcla física, el agente de compatibilidad se sintetiza químicamente antes de la operación de mezcla, y posteriormente se agrega a los componentes de la mezcla como un componente no reactivo. Debido a sus características químicas y moleculares, tiene un efecto emulsionante y promueve la adhesión entre las fases.
Compatibilización reactiva
Es posible distinguir clases principales tales como polimerización en masa, compatibilización reactiva, degradación controlada, acoplamiento, injerto y funcionalización. Todos los tipos de reacciones se pueden clasificar en procesamiento reactivo. En la compatibilización reactiva, los copolímeros pueden formarse in situ a través de la fusión por fusión de la duración de la unión covalente o irónica. En este tipo de reactivo compatibilización, generalmente una fase contiene grupos reactivos inherentes al polímero, mientras que la otra no tiene una funcionalidad inherente. Los grupos reactivos se pueden incorporar a la segunda fase añadiéndola al polímero funcionalizado, que es miscible. En algunos casos, ambos polímeros tienen que funcionalizarse.
Efectos compatibilizante
Reduce la energía interfacial.
Permite una dispersión más fina durante el mezclado.
Proporciona estabilidad contra La separación gruesa de fases durante el procesamiento.
Mejora la adhesión interfacial.
Una compatibilización exitosa de mezclas de polímeros es necesario:
- Que los polímeros posean suficientes grupos funcionales reactivos
- Que la reacción sea rápida, selectiva y preferentemente irreversible
- Que las condiciones de mezclado sean tales
- Que minimicen las limitaciones de transferencia de masa
Transparencia
Una aleacion binaría, si es miscible y amorfa será homogénea y presentará un solo índice de refracción intermedio al de los polímeros puros, al no tener partículas dispersas será transparente. Sin embargo si es inmiscible dependiendo del tamaño de las partículas dispersas el sistema dispersará la luz.
Aplicaciones
Estos alloys se podrían aplicar en la manufactura de componentes para automóviles y aparatos electrónicos tambien las aplicaciones más importantes se encuentran en artículos domésticos como cubetas, tinas, platos y vasos; en envases como botellas para jugos, productos químicos, productos farmacéuticos y depósitos de agua. También se fabrican cajas para refrescos, contenedores industriales, tarimas, juguetes, tapas y tubería.
Blends comerciales principales
- Se agrega polietileno de baja densidad al polietileno lineal de baja densidad para producir la sensibilidad al corte no neutoniana necesaria para la producción de película soplada. El caucho EPDM se agrega a polietileno y polipropileno de alta densidad para proporcionar resistencia al estrés ambiental. Está injertado en polipropileno para aumentar la resistencia al impacto a baja temperatura. Se injerta con anhídrido maleico (maleado) y luego injertado en nylon para aumentar su resistencia al impacto. Comunicados de prensa recientes sugieren que esta técnica también se está aplicando a otros termoplásticos de ingeniería.
- El polibutadieno se injerta en poliestireno y SAN para producir poliestireno de alto impacto y ABS.
- El caucho de nitrilo se usa para aumentar la resistencia al impacto de las resinas epoxi. Está hecho como un oligómero líquido de bajo peso molecular con grupos terminales carboxi (CTBN) y se utiliza como agente de curado para la resina epoxi.
- Se agrega poliestireno al éter de polifenileno para mejorar la capacidad de procesamiento del fundido y disminuir el costo. Cuando se usa el estireno de impacto, también aumenta la resistencia al impacto.
- Se agrega ABS al cloruro de polivinilo rígido para aumentar la capacidad de procesamiento y la resistencia al impacto. Se agrega al policarbonato para aumentar la procesabilidad del fundido y la resistencia al agrietamiento por estrés ambiental y para disminuir la sensibilidad y el costo de la muesca.
- Se agrega politetrafluoroetileno al acetal, policarbonato y nylon para disminuir la fricción y aumentar la resistencia a la abrasión.
- El acetato de polivinilo se agrega como resina de bajo perfil en poliéster termoestable insaturado para disminuir la contracción y evitar que sobresalgan las fibras de refuerzo. Da así una superficie mejorada.
- Se agrega acrilato de polietileno al cloruro de polivinilo rígido para mejorar la capacidad de procesamiento de la masa fundida. Se compatibiliza injertando sobre él metacrilato de polimetilo.
- Se agrega acrilato de polibutilo al cloruro de polivinilo rígido para aumentar la resistencia al impacto. Se compatibiliza injertando sobre él metacrilato de polimetilo.
- El tereftalato de polietileno y el tereftalato de polibutileno se agregan al policarbonato para proporcionar resistencia al agrietamiento por estrés ambiental.
- Se agrega nylon al polietileno de alta densidad para hacerlo impermeable para el uso en tanques de gasolina.
"No es posible que dos cosas estén bastante unidas sin una tercera, ya que necesitan un vínculo entre ellas que las unirá a ambas"
Keyword
Blends, lega, mechanical mix, mezclas, aleacion, compound, compounds, alloyes, alloy, blend, comaptibilizer, compatibilizante, agente acoplamento, energía interfacial