Poliamidas aromáticas
Termoplàsticos > ► Poliamidas > ► Poliamidas aromáticas
Poliamidas aromáticas
Las poliamidas aromáticas o también llamadas poliaramidas se caracterizan por poseer una elevada rigidez
esqueletal debido a los grupos aromáticos que contienen. Los puntos de fusión de estas poliamidas se
encuentran frecuentemente por encima de la temperatura de descomposición y son menos inflamables que las
poliamidas alifáticas.
Se han desarrollado poliamidas aromáticas (o aramidas) a base de ácidos iso y tereftálico y fenilendiaminas, que
se condensan por polimerización interfacial (las aminas disueltas en agua, los cloruros de acilo en un disolvente
orgánico, reaccionando en la interfase) y disponen de un grado de cristalinidad muy elevado, no predecible en el
caso de la m-fenilenisoftalamida, dada su asimetría molecular.
Lo que distingue a las poliamidas aromáticas de las alifáticas (nylons tradicionales) es, naturalmente, su
composición química y sus propiedades. A continuación se muestran en la tabla siguiente las temperaturas de
transición vítrea y de descomposición de algunas poliamidas alifáticas y aromáticas, donde se observa la gran diferencia de estabilidad térmica de ambas familias. Hay que añadir que las poliamidas aromáticas presentan
además mejores niveles de resistencia mecánica y química.
Poliaramidas
La poliamida aromáticas se prepara cuando los grupos aromáticos están presentes a lo largo de la columna vertebral. Esto imparte una gran rigidez a la cadena polimérica. Una dificultad encontrada en esta clase de materiales es su tendencia a descomponerse antes de fundirse. Sin embargo, ciertas poliamidas aromáticas han ganado importancia comercial. Las poliamidas aromáticas se pueden clasificar en tres grupos: copolímeros amorfos con una alta Tg, polímeros cristalinos que se pueden usar como termoplásticos y polímeros cristalinos que se usan como fibras. Los copolímeros son no cristalinos y transparentes. La estructura rígida de la cadena aromática da a los materiales una alta Tg. Uno de los tipos más antiguos es la poli(trimetilhexametileno tereftalatamida) PA63T. Este material tiene una estructura de cadena irregular, lo que restringe la cristalización del material, pero con una Tg cercana a los 150°C. Otras poliamidas transparentes incluyen Hostamid con una Tg también cercana a los 150°C, pero con mejor resistencia a la tracción que PA63T. PA 12/MACM es un tercer copolímero de poliamida con una Tg de aproximadamente 160°C y la absorción de agua y la densidad más bajas de los tres. Las poliamidas aromáticas son materiales duros y compiten con el policarbonato, el poli(metacrilato de metilo) y la polisulfona. Estos materiales se utilizan en aplicaciones que requieren transparencia. Se han utilizado para recipientes de disolventes, piezas de caudalímetros y carcasas transparentes para equipos eléctricos. Un ejemplo de poliamida aromática cristalizable es la poli-m-xilileno adipamida. Tiene una Tg cercana a los 85 a 100°C y una Tm de 235 a 240°C. Para obtener una alta temperatura de deflexión térmica, normalmente se venden los grados rellenos. Las aplicaciones incluyen engranajes, enchufes eléctricos y componentes de máquinas cortadoras de césped. Las poliamidas aromáticas cristalinas también se utilizan en aplicaciones de fibras. Un ejemplo de este tipo de material es el Kevlar, una fibra de alta resistencia utilizada en chalecos antibalas y en estructuras compuestas. Un material similar, que se puede procesar más fácilmente, es la fibra meta aramida, que se puede usar para dar retardo de llama a la tela cuando se usa como revestimiento. Tanto las poliamidas aromáticas (aramidas) como las alifáticas (nailon) se consideran materiales de ingeniería. Sin embargo, las aramidas superan ampliamente las propiedades mecánicas y la resistencia térmica y química de las medias de nailon, y las diferencias son consecuencia de la naturaleza de la estructura aromática de las aramidas. Según la definición dada por la Comisión Federal de Comercio de los Estados Unidos (FTC), las poliamidas totalmente aromáticas son poliamidas sintéticas en las que al menos el 85% de los grupos amida están unidos directamente a dos anillos aromáticos. Debido a su estructura química, las poliamidas totalmente aromáticas exhiben una serie de características sobresalientes, como alta resistencia química y térmica, excelentes propiedades mecánicas y baja inflamabilidad, que las califican para ser clasificadas como materiales de alto desempeño. Estos materiales son útiles en tecnologías avanzadas, donde se utilizan cada vez más para reemplazar la cerámica y los metales. La poli (p-fenilen tereftalamida) (PPTA) y la poli (m-fenilen isoftalamida) (MPIA) son las aramidas comerciales más conocidas. También son los más simples y fueron los primeros en sintetizarse. En solución, se pueden transformar en fibras sintéticas resistentes a las llamas y al corte, de alta resistencia a la tracción. Los materiales transformados son ampliamente utilizados en aplicaciones tecnológicas, como tejidos protectores y deportivos; armadura corporal a prueba de balas; revestimientos, rellenos o compuestos avanzados en las industrias aeroespacial y de armamento; filtros industriales; y aislamiento eléctrico. Sin embargo, debido a su estructura química, su solubilidad en la mayoría de los solventes orgánicos comunes es muy pobre y sus temperaturas de transición son más altas que sus temperaturas de descomposición. Por tanto, son difíciles de procesar, lo que limita su uso en algunas aplicaciones. Como resultado, la investigación básica y aplicada se realiza con dos objetivos: (1) superar los problemas asociados con las dificultades de procesamiento y la escasa solubilidad sin cambiar sus propiedades de alto rendimiento y (2) ampliar el alcance de su uso como alto rendimiento. materiales de alto rendimiento a campos nuevos o prometedores de investigación de materiales, como ósmosis inversa (RO), membranas de intercambio iónico o de gas, nanocompuestos con rendimiento térmico y mecánico avanzado, materiales ópticamente activos y materiales electroluminiscentes o fotoluminiscentes. A finales de la década de 1950, el nailon y el poliéster eran los materiales sintéticos más avanzados tecnológicamente. Para lograr la máxima tenacidad, las cadenas de polímero tuvieron que extenderse y asumir un empaquetamiento cristalino casi perfecto, lo que requirió estirar mecánicamente la fibra después del hilado por fusión. La tenacidad y el módulo de elasticidad del poliéster y las medias de nailon estaban lejos de los teóricamente posibles. En 1965, se una aramida totalmente paraorientada, poli (p-benzamida) (PBA), comercializada con el nombre de Fibra B. Su producción duró solo unos pocos años, probablemente debido a razones económicas. Esta fibra fue reemplazada por PPTA, que se comercializó con el nombre comercial de Kevlar, en 1971. La policondensación de PPTA se realizó inicialmente a baja temperatura en una solución de dicloruro de tereftaloilo (TPC) y p-fenilendiamina (PPD) en hexametilfosforamida (HMPA). Posteriormente, el disolvente se reemplazó por N-metil-2-pirrolidona (NMP) con CaCl2. Para procesar el PPTA, debe transformarse en fibras hilando a partir de soluciones liotrópicas en ácido sulfúrico concentrado a altas temperaturas debido a su insolubilidad en disolventes orgánicos. Al mismo tiempo, DuPont produjo una alternativa a la fibra totalmente para-aramida, MPIA, que originalmente se llamaba HT-1 y estuvo disponible comercialmente en 1967 con el nombre comercial de Nomex. La estructura de esta fibra es menos lineal que la de PPTA, lo que resulta en una disminución de su energía cohesiva y tendencia a cristalizar, pero aún presenta buenas propiedades mecánicas y tiene una mayor resistencia térmica al fuego. Una fibra de para-aramida muy fuerte fue desarrollada y producida por Teijin Limited y estuvo disponible bajo el nombre comercial Technora en 1987. Esta fibra se obtuvo copolimerizando TPC, PPD y 3,4-oxidianilina (ODA), produciendo un polímero, ODA/PPTA, con mayor solubilidad. Debido a la asimetría del monómero ODA, este material está menos ordenado y tiene una energía cohesiva más baja que PPTA y MPIA. Sin embargo, sigue siendo una fibra de alto rendimiento con buena resistencia a la fatiga, alta resistencia a la tracción, estabilidad dimensional a largo plazo y excelente resistencia a la corrosión, el calor y los productos químicos. Las poliamidas aromáticas, a menudo llamadas aramidas, tienen una mayor resistencia al calor en solventes a la llama y una mayor estabilidad dimensional que todas las poliamidas alifáticas, pero son mucho más caras, más difíciles de producir y de trabajar. Las poliamidas tienen varias ventajas sobre otras plásticos de ingeniería. Por ejemplo, son más resistentes a la hidrólisis alcalina que los poliésteres pero no resisten la hidrólisis ácida. También tienen una mejor resistencia al solvente líquido orgánico que el PET y la PC. Estos monómeros ahora están ampliamente disponibles a un costo medio. Las dos primeras empresas, DuPont y Teijin, tienen una posición dominante en el mercado de las aramidas. Las poliamidas aromáticas se preparan comúnmente de acuerdo con los dos métodos siguientes: (1) reacción entre cloruros de diácido y diaminas a bajas temperaturas y (2) policondensación directa de diácidos aromáticos con diaminas en solución a altas temperaturas. En ambos casos, se utilizan disolventes apróticos polares, como HMPA, NMP, N, N-dimetilformamida (DMF) o N,N-dimetilacetamida (DMA). Para aumentar la solubilidad al disminuir la fuerza de los enlaces de hidrógeno entre cadenas, se añaden sales de LiCl y CaCl2 o una combinación de estas sales a la mezcla, particularmente en la síntesis del para-aramida PPTA. Los factores importantes en el proceso de polimerización incluyen la estequiometría del monómero, la pureza del disolvente y los monómeros, la intensidad de la agitación, las condiciones anhidras, la concentración de monómero y la temperatura. Para la preparación de MPIA a baja (a) y alta (b) temperaturas se usa trifenilfosfito (TPP) como promotor de condensación. A escala de laboratorio, los disolventes se secan con pentóxido de fósforo, por ejemplo, y se destilan dos veces. Todas las sales añadidas a la reacción de polimerización deben secarse cuidadosamente para mantener las condiciones anhidras. El ácido isoftálico y el ácido tereftálico se purifican mediante cristalización en agua. El dicloruro de isoftaloílo (IPC) y el TPC se preparan haciendo reaccionar sus ácidos con SOCl2 y luego cristalizándolos en heptano seco. La metafenilendiamina (MPD), PPD y 3,4'-oxidianilina se purifican mediante sublimación al vacío doble.
Métodos de solución a baja temperatura
A escala de laboratorio, generalmente se prefiere el método de solución a baja temperatura cuando el cloruro de diácido puede obtenerse fácilmente del diácido aromático. Desde un punto de vista comercial, los métodos de solución a baja temperatura se utilizan para condensar PPD y TPC en NMP con CaCl2 o MPD e IPC en DMA como promotor de solubilidad para la síntesis de PPTA y MPIA, respectivamente. ODA/PPTA se prepara comercialmente mediante la policondensación de PPD y ODA (50% cada uno) con dicloruro de isoftaloílo en NMP sin promotores de solubilidad, y el HCl desprendido se neutraliza con Ca(OH)2. El principal inconveniente de este método es que se necesita una pureza de monómero extremadamente alta para obtener materiales de alto peso molecular. El peso molecular medio numérico (Mn) que se obtiene típicamente para los polímeros de condensación y, por tanto, las poliamidas aromáticas, es de 10 x 10e3 a 30 x 10e3 g/mol. Este método produce polímeros con una polidispersidad entre aproximadamente 2 para polímeros de menor peso molecular y 3 para polímeros con pesos moleculares promedio en peso superiores a 35 × 103 g/mol. A escala de laboratorio, el procedimiento de síntesis puede modificarse sililando el diaminas, lo que aumenta la reactividad del grupo amino. Las diaminas sililadas son sensibles a la humedad y, para evitar la necesidad de pasos de aislamiento y purificación, este procedimiento se realiza in situ. Algunos de los primeros informes de síntesis de aramidas empleaban un sistema de policondensación de dos fases a temperatura ambiente, a saber, polimerización interfacial. En este método, la diamina y el cloruro de diácido se disuelven en agua y un disolvente con solubilidad en agua limitada, respectivamente. La solución acuosa normalmente contiene un tensioactivo y una base para neutralizar el HCl generado. Tras agitar vigorosamente, se forma un precipitado de polímero. La reacción ocurre en segundos en el solvente orgánico en la interfaz. Esta técnica tiene algunos inconvenientes que dificultan su desarrollo a escala comercial: la estequiometría en la interfaz es difícil de controlar porque la concentración instantánea depende de la difusión y tiene una dependencia limitada de las concentraciones de monómero y la precipitación del polímero en crecimiento. Las cadenas generalmente producen aramidas con una amplia distribución de peso molecular que no son adecuadas para fibras o materiales formadores de películas. Las películas se pueden moldear a partir de soluciones con propiedades químicas deseables. Además, se pueden utilizar como monómeros derivados de dihidrocloruro solubles en agua de diaminas insolubles en agua.
Métodos de solución a alta temperatura
Si el cloruro de diácido no puede obtenerse del diácido aromático correspondiente o es de baja calidad, lo que significa que es probable que se produzcan reacciones secundarias o es sensible al calor o la humedad, las diaminas aromáticas y los diácidos pueden reaccionar mediante policondensación directa. Este método fue desarrollado por Yamazaki e Higasi a mediados de la década de 1970, pero actualmente no se utiliza comercialmente. En este método de fosforilación, los diácidos y diaminas se condensan directamente a 110°C en NMP en presencia de agentes promotores de la condensación, como TPP y piridina (Py), y sales, como LiCl, CaCl2 o una mezcla de los dos. . Además del requisito de monómeros de alta pureza, otro inconveniente de este método es que pueden producirse reacciones secundarias debido a las condiciones de alta temperatura. Por lo tanto, los compuestos modelo a menudo se preparan primero para verificar la ausencia de reacciones secundarias en las condiciones de polimerización cuando se usan monómeros con grupos funcionales sensibles. Recientemente, se ha desarrollado una nueva técnica para la síntesis de polímeros que implica la policondensación asistida por microondas de diácidos aromáticos y diaminas en condiciones de Yamazaki. La radiación de microondas (MW) es una fuente de energía no convencional ampliamente utilizada capaz de promover reacciones químicas de una manera extremadamente rápida y poco convencional. El sistema MW reemplaza los sistemas convencionales de calefacción y control de temperatura, reduciendo el tiempo de reacción de aproximadamente 4 ha 2 min, manteniendo las viscosidades inherentes obtenidas con los métodos convencionales y suprimiendo las reacciones secundarias. 17-20 MW también ha demostrado ser efectivo para el policondensación de diisocianatos aromáticos o alifáticos y diácidos para producir poliamidas semiaromáticas. Se obtienen viscosidades inherentes entre 0,51 y 0,2 dL/g de la reacción, que se completa en menos de 5 min. Los esfuerzos recientes también se han dirigido al desarrollo de métodos de policondensación más limpios y eficientes al disminuir el uso de disolventes orgánicos volátiles y tóxicos tradicionales. Para evitar el uso de disolventes nocivos como piridina o NMP en el método de poliamidación de Yamazaki, o DMF, DMA y NMP en la policondensación a baja temperatura, se han preparado aramidas respetuosas con el medio ambiente utilizando líquidos iónicos. Los líquidos iónicos son sales que existen en el fase líquida a temperatura ambiente y son capaces de disolver poliamidas aromáticas debido a su alta polaridad, alta constante dieléctrica, alta estabilidad térmica y baja presión de vapor. En consecuencia, se han preparado poliamidas respetuosas con el medio ambiente con TPP para promover la condensación directa de diácidos y diaminas y la reacción de dicloruros de diácidos y diaminas a bajas temperaturas. En resumen, métodos tanto convencionales como de alta temperatura que utilizan TPP como promotor de condensación o la policondensación asistida por MW para reducir los tiempos de reacción se puede emplear en un procedimiento de policondensación porque se obtienen viscosidades inherentes y pesos moleculares comparables para polímeros con estructuras químicas idénticas.
Métodos alternativos de polimerización
Está fuera del alcance de este capítulo cubrir todos los métodos sintéticos proporcionados por la química orgánica para obtener los enlaces amida aromáticos o semiaromáticos utilizados para preparar poliamidas. Estos métodos incluyen, entre otros, la reacción de diácidos y diisocianatos para sintetizar poliamidas total y parcialmente aromáticas, policondensación directa usando cloruro de tionilo como agente activador, condensación de diácidos con las sales de formamidinio de diaminas aromáticas, uso de diaminas y CS2, reacción de ésteres de fenil diácido aromático con aminas, reacción de haluros de diácido y diaminas activadas mediante sililación in situ, carbonilación catalizada por paladio - policondensación a partir de compuestos de dihaloarilo y diaminas aromáticas, etc.
Policondensación de cadena de crecimiento
Los resultados experimentales en los que se obtuvieron algunos polímeros de condensación de alto peso molecular con bajas conversiones allanaron el camino para los métodos de policondensación de crecimiento de cadena. Estos métodos implican suprimir la reacción entre monómeros activando selectivamente el terminal de propagación del polímero, obligando al monómero a reaccionar solo con el iniciador y el grupo terminal del polímero. Yokoyama y col. publicó una revisión detallada de la policondensación de crecimiento de cadena que discute su teoría, estructuras y aplicaciones. Una forma de obtener polímeros con estructuras controladas es activar selectivamente los grupos terminales del polímero cambiando los efectos sustituyentes entre los grupos funcionales del monómero. Por ejemplo, en un monómero AB, el efecto sustituyente del sitio B disminuye la reactividad del sitio A, suprimiendo así la reacción de crecimiento escalonado entre los monómeros. El efecto sustituyente cambia cuando el monómero reacciona con el sitio reactivo de un iniciador. Si el enlace recién formado aumenta la reactividad del grupo terminal del polímero, el siguiente monómero solo reacciona con el extremo que se propaga del polímero. Sin embargo, esta polimerización no puede controlarse completamente, debido a la baja solubilidad del polímero resultante, reacciones secundarias o inhibición insuficiente de la policondensación de crecimiento escalonado. Sin embargo, la polimerización por condensación se puede controlar completamente cambiando la resonancia o los efectos inductivos de los sustituyentes en las condiciones de reacción. Por ejemplo, la policondensación de fenil-4-octilaminobenzoato en presencia del iniciador fenil-4-nitrobenzoato y una base (una combinación de N-octil-N-trietilsililanilina, CsF y 18-corona-6) en condiciones suaves produce un polímero (I) con una estructura bien definida. El peso molecular de la poliamida se puede controlar mediante la relación de alimentación del monómero al iniciador hasta Mn = 22.000, y se puede lograr una polidispersidad de (Mw / Mn) ≤ 1,1. En esta polimerización, la reactividad está controlada por la diferencia en los efectos de resonancia del anión aminilo y el enlace amida del polímero como sigue: la desprotonación del monómero AB (2) en presencia de una base produce el anión aminilo (4), que es capaz de desactivar el resto fenil éster de (2) mediante el efecto de resonancia (re). Específicamente, el anión amida disminuye la electrofilicidad del resto fenil éster en la posición para porque es fuertemente donador de electrones.
Poliamidas aromáticas como biomateriales y para uso en medicina
Es importante señalar que las para-aramidas se pueden utilizar en aplicaciones médicas, reemplazando las aleaciones metálicas en implantes y prótesis artificiales y previniendo problemas asociados con la radiación dispersa en los exámenes de diagnóstico. Trabajos recientes han reportado el uso de poliamidas en cabello y pelucas artificiales porque imitan estos materiales debido al enlace amida. En otro trabajo, Ahamad exploró la formación de complejos entre dendrímeros de poliamida y Pd (II) o Pt (II) (metalodendrímeros ) y estudiaron su actividad antibacteriana frente a bacterias grampositivas y gramnegativas. Los ensayos de citotoxicidad de los dendrímeros y metalodendrímeros mostraron que los dendrímeros de segunda generación eran activos contra todas las cepas bacterianas patógenas. Otra posible aplicación biomédica es el uso de aramidas para estudiar las interacciones entre el ADN y los aglutinantes artificiales para comprender los procesos y mecanismos en el contexto de la terapia génica.
PPA
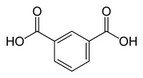
Poli(m-fenilenisoftalamida), MPIA
Poli(p-fenilenetereftalamida), PPTA
HT-1 nailon o PMPI
Alta rigidez de la cadena y alta Tgresistencia a la temperatura y al fuego, buenas propiedades eléctricas (aislamiento eléctrico, motores eléctricos, generadores, cintas transportadoras, ropa de protección resistente al fuego y a la temperatura, guantes, etc.)
Propiedad | PA6 | PA66 | PA46 | PA6T/6 | PA6T/6I | PA9T | SPS |
Tg (°C) | 47 | 47 | 75 | 100 | 100 | 125 | 100 |
Tm (°C) | 225 | 265 | 295 | 300 | 290 | 300 | 270 |
HDT a 0,45 MPa, (°C) | 165 | 235 | 280 | 100 | — | — | 110 |
HDT @ 1.8 MPa, (°C) | 66 | 70 | 190 | 120 | 140 | 120 | 99 |
Densidad (g/cm3) | 1,13 | 1,14 | 1,18 | 1,16 | 1,21 | 1,34 | 1,01 |
Módulo de tracción (MPa) | 2944 | 3300 | 3300 | 3200 | 2440 | 2206 | 3440 |
Resistencia a la tracción (MPa) | 76 | 86,0 | 100 | 100 | 108 | 55 | 41 |
Izod con muescas (J/m) | 53 | 59 | 96 | 70 | 49 | — | 11 |