Soplado
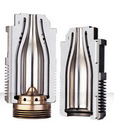
A diferencia de otros procesos de extrusión, no existe un extractor para extraer el producto del extrusor.
En cambio, la formulación plastificada, entregada por la extrusora, ingresa a un acumulador, donde el material se entrega periódicamente a un molde en forma de un tubo largo, hueco y fundido llamado parisón. El molde se cierra alrededor del parisón, y se inyecta aire en el centro del parisón, inflándolo para duplicar la forma del molde. Después de que el polímero se solidifica y se enfría en la herramienta, se libera la presión, el molde se abre y la pieza se expulsa y se retira del molde. El proceso se repite con un nuevo parisón del acumulador. En comparación con otros procesos de extrusión, el moldeo por extrusión-soplado requiere más espacio vertical y menos espacio en el piso para producir piezas terminadas. La altura de la máquina depende de las dimensiones finales de las piezas que se producen. El acumulador y la matriz se asientan sobre la herramienta, permitiendo que el parisón pase entre las dos mitades del molde con un pasador insertado en la parte inferior para inyectar aire en el parisón, expandiéndolo a la superficie del molde. El parisón debe ser lo suficientemente viscoso como para mantener su estabilidad como una estructura vertical libre antes del soplado. Esto se relaciona con la resistencia de la masa fundida "melt strenght" que requiere mayores pesos moleculares que en la inyección, particularmente cuando el parisón se produce por extrusión. El flujo es esencialmente viscoelástico, donde debe tenerse en cuenta la expansión del chorro libre, lo que eventualmente también determina el grosor del producto. Soplar en el molde representa el flujo inducido por tensiones normales (sin tensiones de corte). Esto se caracteriza por la viscosidad elongacional que difiere de la viscosidad convencional. El análisis reológico del flujo, combinado con el estiramiento, es bastante complicado. Existe un proceso de fabricación para cuerpos de diferentes espesores en diferentes zonas (con refuerzo local y ahorro de material). Aquí, el grosor del parisón varía ya sea alterando la velocidad de flujo, lo que afecta el soplado a la salida o directamente de forma mecánica.
Procesos
Hay dos procesos diferentes de moldeo por extrusión-soplado: entrega continua o intermitente de parison. En ambas operaciones, el extrusor funciona continuamente, pero el parison se entrega de una manera diferente a la del proceso cíclico debajo del dado. En el proceso continuo, la extrusora alimenta el polímero al troquel, donde se forma el parisón y se transfiere a moldes rotativos o de lanzadera. El segundo proceso usa un acumulador. Durante el proceso de moldeo, el extrusor rellena el acumulador en preparación para el siguiente disparo. Para aumentar la productividad, se pueden ejecutar dos acumuladores desde una extrusora. La extrusora está montada en una plataforma sobre el molde, con el parisón expulsado del acumulador y la cabeza del troquel directamente en el molde. En la mayoría de las operaciones, se usa una extrusora de tornillo único para suministrar la masa fundida al acumulador. Dependiendo de la resina, la extrusora puede estar equipada con una garganta de alimentación ranurada para aumentar el rendimiento. Dependiendo de la resina, la extrusora puede estar equipada con una garganta de alimentación ranurada para aumentar el rendimiento. En
el moldeo por soplado de coextrusión, se montan dos o más extrusoras en la plataforma sobre el molde, lo que proporciona un fácil acceso de la masa fundida al acumulador y a la matriz. Dependiendo del tamaño de la pieza, se monta una herramienta grande directamente debajo del troquel en una posición vertical entre dos platos horizontales. Durante la operación de formación, la herramienta se cierra alrededor del parisón, con aproximadamente 100 psi de presión de aire inyectado en el parisón, soplando el polímero para tomar la forma del molde. La parte de extrusión de un proceso de moldeo por soplado es continua, y el resto de la operación es cíclica. En la operación continua, se utilizan varios métodos para transportar moldes al troquel parison. Cuando el parisón sale del dado, se coloca entre las dos mitades de una herramienta abierta. Tan pronto como el parisón alcanza la longitud adecuada, el molde se cierra, corta el parisón y, mientras inyecta aire en la herramienta para expandir el parisón, la siguiente herramienta se mueve a la línea con el parisón que cae, mientras el proceso se repite. La relación de expansión del parisón es la cavidad del molde dividida por las dimensiones del parisón. Las relaciones de expansión del orden de 5/6: 1 son comunes. Piezas grandes
El moldeo por soplado de piezas grandes, también conocido como moldeo por soplado industrial o moldeo por extrusión y soplado, es similar al moldeo por inyección y soplado, con la excepción de que el acumulador, el parisón y las piezas son mucho más grandes. El moldeo por soplado se utiliza para producir piezas grandes, irregulares y huecas en una sola operación.
Las ventajas del moldeo por soplado de piezas grandes incluyen el seguimiento:
Los costos de herramientas son bajos en comparación con los de moldeo por inyección o compresión como herramientas puede estar hecho de aluminio y aún proporcionar una larga vida. El proceso de baja presión puede usar compuesto herramientas para prototipos o tiradas cortas de producción.
Son posibles piezas muy grandes, con acumulador:
- Cabezas con cotizaciones de hasta 1000 lb.
- El proceso puede agregar funcionalidad a moldeado partes, con alfombra u otra cubierta de superficie adjunto durante la operación de moldeo
- Piezas de pared delgada y piezas con pared variable
- Se pueden hacer espesores cambiando el perfil de parison
- Las piezas huecas se producen en línea sin necesidad de montaje
- Las piezas son más resistentes a las resinas de bajo flujo de fusión o resinas de alto peso molecular utilizadas para proporcionar mejor resistencia al derretimiento para mantener la forma del parisón
- Partículas de goma agregadas para mejorar el parison la resistencia a la fusión se traduce en una mayor resistencia al impacto
Las desventajas del moldeo por soplado de piezas grandes son como sigue:
- Las esquinas afiladas son difíciles de obtener
- Se requiere desbarbado en todas las partes
- La superficie de alto brillo obtenible con inyección no se puede duplicar
- Las líneas de separación del molde pueden estar presentes
- Pueden aparecer líneas de soldadura en la parte inferior y superior
- Se requiere un perfil de espesor de pared de Parison para mantener un espesor de pared constante.