Inyección
Procesos > ► Inyección
Moldeo por inyección de tecnopolímeros
El moldeo por inyección es una tecnología vital en la fabricación de automóviles, ya que ofrece alta precisión, rentabilidad y escalabilidad para producir piezas de automoción complejas. El moldeo por inyección se utiliza en la producción de piezas de automoción para crear componentes duraderos y de alta calidad. Sus ventajas son la rapidez de producción, la reducción de costes y la uniformidad. Es ideal para producir piezas de plástico, metal y materiales compuestos para diversos modelos de vehículos. Comprender las ventajas y las posibles limitaciones del moldeo por inyección en la producción de automóviles es clave para optimizar el diseño de las piezas y minimizar los costes. Profundice para explorar cómo esta tecnología puede mejorar sus operaciones de fabricación.El moldeo por inyección mejora la eficacia de la producción de piezas de automoción.Verdadero El moldeo por inyección permite producir piezas de automoción a alta velocidad con menos mano de obra y menos desperdicio de material. El moldeo por inyección es la mejor opción para todas las piezas de automoción. Aunque el moldeo por inyección es adecuado para muchas piezas de automoción, otros métodos como la fundición a presión o la estampación pueden ser mejores para piezas metálicas específicas o geometrías complejas.
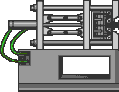
Inyeccion
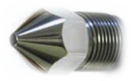
Moldeo por inyección de termoplástico
El moldeo por inyección de termoplásticos es la tecnología más extendida en la transformación de estos materiales. Las piezas de diferentes formas y tamaños se producen de forma cíclica (discontinua), con un peso de unos pocos gramos a varios kilogramos. Algunas ventajas de esta tecnología son:
- la posibilidad de producir piezas con geometrías complejas
- alta productividad
- bajos costos de producción
- alta automatización de procesos
- la posibilidad de producir piezas de muy pequeñas dimensiones
- los moldes y prensas se pueden usar con diferentes materiales plásticos
- la posibilidad de imprimir en combinación con inserciones metálicas
- producción de productos con diferentes colores y materiales
Las principales desventajas son:
- el costo de moldes y prensas
- poco conocimiento de la relación entre proceso y propiedad
- alta competitividad
El moldeo por inyección se lleva a cabo utilizando prensas de moldeo por inyección; En la base de la operación de estas máquinas hay un proceso térmico que hace que el material sea fluido (laminación) seguido de una inyección a alta presión en una cavidad de molde; entonces el componente se extrae después de la solidificación enfriando en forma del molde mismo. Básicamente, hay dos componentes esenciales de una prensa de moldeo.
Fase 1 - inyección: llenado parcial del molde
Fase 2: presión de retención y laminación: llenado completo enfriamiento de moldes y piezas
Fase 3 - extracción: apertura del molde y expulsión de la pieza
El tornillo que en la fase 1 avanza como un pistón empujando el material en el cilindro de plastificación, que está envuelto en bandas de calentamiento eléctrico. En la fase 2, el tornillo, puesto en rotación, lleva el material hacia adelante gracias a su movimiento que genera presión en el frente. Un sistema particular, llamado válvula de retención, es funcional para estas dos fases diferentes que requieren que el flujo de material fundido vaya en dos direcciones opuestas.
La rotación del tornillo produce una redistribución continua de las partículas de plástico transportadas para obtener una buena homogeneidad de calentamiento por transferencia térmica y por fricción interna. La operación de plastificación solo puede comenzar al final de la fase de mantenimiento de la presión, una fase necesaria para compensar la contracción debido a las contracciones térmicas causadas por el enfriamiento de la pieza en el molde, y debe finalizar antes de abrir el molde para no tener fugas de polímero de la boquilla.
La tercera fase se puede llevar a cabo solo cuando la pieza se ha enfriado al menos hasta una rigidez suficiente para no deformarse. Para la separación del canal de conexión en frío (zanahoria) entre la boquilla de la prensa y la pieza, y en cualquier caso, no estresar la mitad del molde de la mesa fija con la presión de contacto de la boquilla, antes de abrir del molde, el conjunto plastificante generalmente se separa del molde.
La física del proceso
- Fase 1 - llenado. El llenado total de la cavidad del molde termina idealmente en el momento exacto de finalización de la cavidad para evitar un aumento incontrolado de la presión. El control de esta fase es volumétrico: la prensa ajusta las velocidades de alimentación de los tornillos y, por lo tanto, los caudales.
- Fase 2 - Compensación "C" o presurización. Fase corta de rápido crecimiento de la presión dentro de la cavidad, obtenida al final del flujo después de que el control de este último ya se ha cambiado al nivel de presión.
- Fase 3 - mantenimiento. Fase de mantenimiento de presión para introducir otro material en la cavidad para compensar las contracciones térmicas debido al enfriamiento que, de lo contrario, generaría succiones y vacíos internos.
- Fase 4 - enfriamiento sin flujo. El enfriamiento del polímero en el molde frío ocurre a partir del mismo instante en que el material comienza a fluir hacia la cavidad. Sin embargo, en la fase de llenado, este fenómeno es contrarrestado por el calor generado por la disipación del flujo que llena rápidamente el molde. Por esta razón, el final de la fase de inyección tiende a considerarse como el comienzo del tiempo de enfriamiento total.Fase 5 - extracción. Una vez que el producto se ha enfriado lo suficiente y la presión interna se ha puesto a cero, puede ser expulsado al molde. La temperatura debe ser tal que evite la deformación durante la extracción y el enfriamiento posterior en el aire. La forma final de la pieza, con contracción y cualquier deformación, tarda un tiempo en completarse debido a los fenómenos de retraso de la cristalización y el reequilibrio de las tensiones internas.
Estrés residual
Las tensiones residuales son tensiones mecánicas presentes dentro de una pieza en ausencia de cargas externas. El conocimiento del alcance de estas tensiones es esencial para predecir la forma y el tamaño final de un producto. Para los polímeros, el término esfuerzo residual se usa para indicar el estado de las cadenas después del proceso de producción. Una pieza obtenida por moldeo por inyección contiene tensión residual si las cadenas de polímero no están en una configuración de equilibrio debido a la desviación de las posiciones de equilibrio de los átomos y las variaciones en las distancias entre los segmentos en las moléculas.
Estrés inducido por flujo
Durante la fase de llenado, las moléculas se orientan y estiran, como ya se discutió, en la dirección del flujo, con una orientación máxima en las capas más externas y con las consiguientes deformaciones elásticas dentro de la pieza. Con la relajación de estas deformaciones cambian las dimensiones de las diferentes capas que conforman el grosor de la pieza. Estas modificaciones están directamente relacionadas con el diferente grado de orientación de las cadenas de estas capas. Las cadenas de las capas más externas tenderían a relajarse más, estando más orientadas, pero están parcialmente impedidas por las de las capas más internas que están menos orientadas. Por esta razón, las tensiones residuales derivadas del relleno solo son la tracción en las áreas más externas y la compresión en el corazón de la pieza.
Estrés inducido por el calor
La aparición de tensiones térmicas en piezas moldeadas por inyección se puede dar una primera explicación de la siguiente manera: cuando el polímero toca el molde y se adhiere a él, la capa externa solidificada no puede contraerse completamente y esto induce una tensión de tensión en el polímero. Este mecanismo se repite para la solidificación de las capas internas, de modo que al final hay un estado tensional de tensión en todo el espesor. Este estado permanece hasta que la pieza se libera del molde. El momento en que ocurre esta liberación es un factor crítico para determinar la distribución del estrés. Si la pieza se separa de las paredes del molde justo después de la solidificación de las capas externas, la distribución de tensiones será similar a la de una pieza que se enfría libremente. Si el desprendimiento ocurre después de la solidificación completa, hay tracción en todo el espesor. Por otro lado, se produce una distribución más compleja si el desprendimiento tiene lugar en una situación en la que la solidificación es intermedia entre las dos situaciones que acabamos de describir.
Factores adicionales que afectan la adhesión
- Los niveles de producción son muy altos, incluso con formas complicadas.
- Los costes son más bajos, sobre todo si se externaliza el proceso de inyección.
- Las piezas fabricadas requieren de pocos acabados.
- El manejo de material es reducido.
- El coste inicial en moldes es elevado
- Altos niveles de producción y bajos costos
- Moldeo de piezas con geometrías muy complicadas
- Alta o baja automatización, esto depende del valor de la pieza.
- Las piezas una vez acabadas requieren de poco acabado, son terminadas con la rugosidad deseada, color y transparencia.
- El manejo de material está reducido a causa de la tolva de prensa contendrá usualmente suficiente material para moldear piezas por un período extendido.
- Las espigas de núcleo con diámetro más largo y pequeño pueden ser usados porque pueden ser sostenidos en ambos extremos.
- Tras haber sido cerrado el molde antes de inyectar en él cualquier material adentro, las piezas que contienen inserciones de metal pueden ser moldeadas sin tener rebabas de material en las inserciones.
- Las tolerancias relativamente más apretadas a través de las líneas de separación son posibles.
- La rebaba en la línea de separación puede ser mantenida a un grosor mínimo si el molde está diseñado apropiadamente y bien mantenido.
- El moldeo por inyección de materiales termoendurecidos es apto para automatizar el proceso lo que puede resultar en bajos precios por pieza.
- La deformación puede ser problema en el moldeo por inyección porque los materiales de inyección tienen flujos más suaves y más encogimiento. Introducir por la fuerza el material por el bebedero, canal y entrada, puede orientar el material produciendo encogimiento no uniforme.
- El llenar de las piezas por una de las dos entradas produce piezas que tienen líneas de punto. Estas líneas de punto son las más débiles áreas en la pieza.
- La cantidad de chatarra en total producida durante moldeo por inyección será usualmente más superior que la de moldeo por compresión a causa de la chatarra adicional creada por el bebedero y canal. En el pasado, la chatarra termoendurecida tenía que ser tirada en un vertedero de basuras. Sin embargo, ahora están siendo reciclados con éxito algunos materiales termoendurecidos.
Contrapresión
La contrapresión (de inglés back pressure) es la resistencia a la viscosidad de un material al flujo continuo. En el moldeo por compresión, la contrapresión es la resistencia del material cuando se cierra el molde. En extrusión, es la resistencia al flujo hacia adelante de material fundido. Al aumentar la contrapresión, la cantidad de trabajo que soporta el plástico puede regularse para causar más cizallamiento, temperaturas más altas y un mayor grado de plastificación. Sin embargo, esto suele ir acompañado de un ciclo más lento. Estos ajustes son particularmente importantes para los plásticos sensibles al calor.
Puerto de alivio de contrapresión
El puerto de alivio de contrapresión es una abertura en una matriz de extrusión que permite que escape el exceso de material.