Polimerización Slurry
Procesos > ► Polimerización
Polimerización de suspensión
Los reactores de suspensión o "slurry", en lugar de los reactores de fase gaseosa, se utilizan en la mayoría de los estudios de laboratorio de polimerización catalítica de olefinas. Los resultados de los reactores de suspensión se utilizan con frecuencia para predecir la actividad de los catalizadores para los reactores de fase gaseosa. Los procesos en fase gaseosa se utilizan cada vez más para la producción comercial de poliolefinas ya que la operación en fase gaseosa tiene ventajas significativas sobre los procesos de suspensión y solución. reactores de polimerización. Los dos principales problemas operativos de los reactores de fase gaseosa son la suspensión adecuada de las partículas sólidas (agitación) y el control de la temperatura. La transferencia de calor desde los sitios catalíticamente activos en el "núcleo" de la partícula de polímero en crecimiento depende de la eficacia con la que la fase gaseosa circundante, que es un agente de transferencia de calor muy pobre, pueda eliminar el calor a la superficie de intercambio de calor del reactor. Como resultado, la temperatura de las partículas de polímero en crecimiento puede ser mucho más alta que la medida por las sondas de temperatura en el reactor. Estas altas temperaturas pueden resultar en una rápida desactivación del catalizador, posiblemente por encapsulación física del catalizador por polímero "fundido". La introducción reproducible del catalizador y el cocatalizador en reactores de fase gaseosa es otro problema. Sin embargo, estos problemas pueden aliviarse en gran medida mediante el diseño adecuado del reactor de fase gaseosa y mediante el uso de condiciones y procedimientos operativos apropiados.
- Purificación
- Reacción
- Purga
- Recuperación de ventilación
- Adición Aditiva
- Peletizado
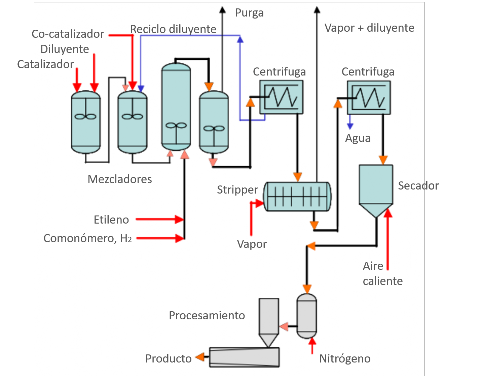
Los procesos en fase de suspensión incluyen 3 fases dentro del reactor: una fase gaseosa, que contiene etileno, hidrógeno y posiblemente comonómero, y una suspensión que contiene catalizador sólido y partículas de polímero y el diluyente líquido. La razón para agregar el diluyente líquido es que operar con etileno líquido no sería práctico. El proceso de polimerización en fase de suspensión más simple incluye una serie de CSTR con la polimerización que ocurre dentro de un catalizador heterogéneo suspendido en un medio inerte (el diluyente). En los primeros procesos comerciales se necesitaba una serie CSTR para compensar la baja actividad del catalizador Ziegler-Natta. También fue necesaria una operación de eliminación de cenizas para eliminar los residuos de catalizador, lo que aumentó en gran medida los costos de capital asociados con dichos procesos. La llegada de catalizadores de alta actividad trajo consigo una mejora significativa en los procesos establecidos y hoy en día es posible producir el polímero en dos reactores sin desashing. El proceso de fase de suspensión fue el primer proceso desarrollado para la polimerización de etileno y sigue siendo hasta el día de hoy una alternativa económicamente viable y competitiva. Cuando se opera en serie, el catalizador solo se alimenta al primer reactor y el resultado es un aumento en la producción de la planta. Sin embargo, si se opera en paralelo, la ventaja es la capacidad de producir diferentes polímeros. En el primer reactor se agrega un catalizador con un perfil de desintegración, produciendo un homopolímero de bajo peso molecular. Dado que el hidrógeno (controla el peso molecular como agente de transferencia de cadena) provoca una disminución en la velocidad de polimerización, debe agregarse cuando el catalizador muestra su mayor actividad intrínseca (por lo tanto, el primer reactor). En el segundo y a veces en el tercer reactor se introduce una pequeña cantidad de un comonómero de α-olefina. Esto aumenta la velocidad de reacción, en cuanto a homopolimerización, y mantiene una buena productividad. Esto se conoce como el retroceso del comonómero. Independientemente de que la polimerización se lleve a cabo en suspensión, fase gaseosa o líquida, este orden de adición (catalizador, hidrógeno y comonómero) se emplea a menudo para lograr mejores resultados.
Reactor de tanque agitado de diluyente pesado de fase de lechada
• Tecnología Amoco que utiliza un sistema catalítico patentado
• Tecnología de Asahi Chemical utilizando un sistema catalítico Ziegler
• Tecnología Hercules que utiliza un sistema catalítico Ziegler
• Tecnología Exxon que utiliza un sistema catalítico Ziegler
• Tecnología Chisso que utiliza un sistema catalítico de Ti/Mg/V
• Tecnología de Dow Chemical utilizando un sistema catalítico Ziegler
• Tecnología DuPont que utiliza un sistema catalítico Ziegler
• Tecnología Hoechst que utiliza un sistema catalítico Ziegler
• Tecnología ICI utilizando un sistema catalítico Ziegler
• Tecnología Hüls que utiliza un sistema catalítico Ziegler
• Tecnología Idemitsu que utiliza un sistema catalítico Ziegler
• Tecnología Montedison usando un sistema catalítico Ziegler
• Tecnología Shell usando un sistema catalítico Ziegler
• Tecnología Sumitomo usando un sistema catalítico Ziegler
• Tecnología Stamicarbon usando un sistema catalítico Ziegler
• Tecnología de Mitsubishi Petrochemical utilizando un sistema catalítico Ziegler
• Tecnología de Mitsui Petrochemical utilizando un sistema catalítico Ziegler
• Tecnología de Mitsubishi Chemical que utiliza sistemas catalíticos de Ti, Cr, V y Ti/V
Reactor de tanque agitado con diluyente liviano en fase de lechada
• Tecnología Sumitomo usando un sistema catalítico Ziegler
• Tecnología Mitsui Toatsu utilizando un sistema catalítico Ziegler
Reactor de bucle de diluyente ligero de fase de suspensión
• Tecnología Solvay que utiliza un sistema catalítico Ziegler
• Tecnología Chemplex que utiliza sistemas catalíticos Cr/Sn/Al/Ti
• Tecnología Phillips que utiliza sistemas catalíticos Ziegler Cr/Ti, Cr/P, Cr, Ti/Mg, V y Ti/V
Reactor de bucle de diluyente pesado en fase de suspensión
• Tecnología Solvay que utiliza un sistema catalítico Ziegler
• Tecnología de National Distillers/ICI utilizando un sistema catalítico Ziegler
Reactor de piscina líquida en fase de suspensión
• Tecnología El Paso utilizando un sistema catalítico Ziegler
• Tecnología Montedison usando un sistema catalítico Ziegler
• Tecnología Montell (ahora llamada Basell) que utiliza sistemas catalíticos Ziegler–Natta de Ti/Mg