LDS (estructuración directa por láser)
Procesos > ► Otros procesos
LDS (estructuración directa por láser)
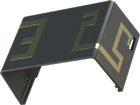
Esta es la tecnología que forma un circuito eléctrico mediante un proceso de marcado con láser y enchapado en la superficie de un artículo de moldeo por inyección de plástico. Este método de producción puede adquirir la ventaja de un cortador de costos, una miniaturización y un ahorro de peso al adoptar como sustitución una placa de circuito eléctrico, una placa de antena, etc.
Estructuración láser directa (LDS)
El proceso LDS utiliza un material termoplástico, dopado con un compuesto inorgánico metálico (no conductor) activado por medio de láser. El componente básico es el moldeado por inyección de un solo componente, prácticamente sin restricciones en términos de libertad de diseño 3D. Luego, un láser escribe el curso de la última traza del circuito en el plástico. Donde el rayo láser golpea el plástico, el aditivo metálico forma una pista microrrugosa. Las partículas metálicas de esta pista forman los núcleos para la posterior metalización. En un baño de cobre no electrolítico, las capas de la ruta del conductor surgen precisamente en estas pistas. De esta manera se pueden levantar sucesivamente capas de acabado de cobre, níquel y oro. El proceso LDS se caracteriza por:
- moldeo por inyección monocomponente
- una amplia gama de materiales está disponible
- tridimensionalidad completa en una esfera
- Flexibilidad: para un enrutamiento modificado de las trazas, solo se deben transmitir nuevos datos de control a la unidad láser. Por lo tanto, se pueden producir diferentes componentes funcionales a partir de una unidad básica.
- precisión: son posibles las trayectorias de conductores más finas con un ancho de <80 µm
- creación de prototipos: el recubrimiento LDS disponible de cualquier pieza permite la muestra de prueba
Tecnología de antena LDS
La estructuración directa por láser (LDS) es un proceso mediante el cual se puede diseñar y producir una antena en un soporte de plástico tridimensional. Este portador puede ser una entidad plástica separada o una parte integral existente de la carcasa del producto del cliente. La carcasa o soporte de plástico se produce mediante el proceso de moldeo por inyección con un polímero especialmente modificado. A continuación, la pieza se monta en la máquina de aplicación de láser LDS, donde se graba el trazo láser en la pieza. A continuación, estas piezas se transfieren para su metalización en un baño de galvanoplastia. Una vez chapadas, las piezas se transfieren a nuestro departamento de calidad, donde cada pieza se prueba para verificar tanto el rendimiento eléctrico como las propiedades mecánicas. A continuación, los componentes se embalan cuidadosamente y se envían al cliente
×
- ► Extrusión
- ► Extrusión compound
- ► Inyección
- ► Sobremolde
- ► Inyección de los polimeros
- ► Adhesión y adhesivos
- ► Defectos de inyección
- ► Defectos de moldeo
- ► Deformación
- ► Falta de resistencia
- ► Empaque
- ► Espumación polímeros
- ► Otros procesos
- Proceso de molienda
- ► Pegamentos
- ► Pelletizadoras
- ► Modificación química
- ► Promotor de adherencia
- ► Modificacion superficial
- ► Moldeo
- ► Moldes
- ► Procesos esteticos
- ► Reticulación
- ► Reciclaje
- ► Soldadura
- ► Vulcanización