Mould
Procesos > ► Moldes
Tipos de moldes
Los tipos básicos de moldes, independientemente de que sean de compresión, inyección, transferencia o incluso soplado, suelen clasificarse por el tipo y número de cavidades que tienen. Por ejemplo,hay varios tipos de moldes: (a) cavidad única, (b) cavidad múltiple dedicada y (c) cavidad múltiple familiar. El molde de una sola cavidad representa uno de los conceptos de molde más simples. Este diseño se presta a una producción de bajo volumen y a diseños de piezas de plástico de gran tamaño. Los moldes de múltiples cavidades pueden ser de dos tipos. Un molde dedicado de múltiples cavidades tiene cavidades que producen la misma pieza. Este tipo de molde es muy popular porque es fácil equilibrar el flujo de plástico y establecer un proceso controlado. En un molde familiar de cavidades múltiples, cada cavidad puede producir una pieza diferente. Históricamente, los diseños de moldes familiares se evitaron debido a la dificultad de llenar de manera uniforme; sin embargo, los avances recientes en la fabricación de moldes y la tecnología de compuertas hacen que los moldes familiares sean atractivos. Este es el caso, especialmente, cuando un procesador tiene un conjunto de varias piezas y le gustaría mantener los inventarios equilibrados.
Moldes
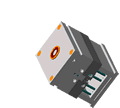
- distribuir el material inyectado a las impresiones
- determinar la forma del objeto
- permitir la liberación de aire o gases que se forman durante la inyección
- eliminar el calor del material termoplástico fundido
- expulse la pieza una vez que se haya enfriado y solidificado
Los moldes requieren de componentes diversos para que la inyección del plástico se lleve a cabo de manera fluida, logrando que todas las partes del proceso se sincronicen a la perfección como instrumentos de una orquesta. Los moldes son hecho de dos o más medias conchas, que delimitan el área del espacio con la forma de la pieza a obtener, generalmente son los componentes de los moldes. El acero templado (obtenido de un proceso térmico que mejora sus características) o endurecido, es el material con el que los moldes de producción se fabrican con mayor frecuencia, sin embargo, para procesos particulares, también se utilizan moldes de aluminio o madera. Los materiales menos resistentes, como el yeso, la silicona o la resina, se utilizan para construir moldes destinados a la producción de series pequeñas o para la creación rápida de prototipos. Los moldes se pueden usar para la producción de algunas piezas, incluso una sola, o para hacer cientos de miles de muestras. El fresado se usa a menudo para la construcción de moldes medianos y grandes, mientras que los moldes particularmente pequeños, con acabados complejos o de muy alta precisión, del orden de unas pocas centésimas de milímetro, se crean gracias a procesos de alta tecnología como EDM o fotograbado.
Diseño de molde
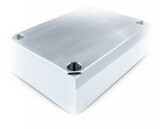
Diseño de herramientas
El diseño de las herramientas para producir una pieza de plástico específica debe considerarse durante el diseño de la pieza en sí. El diseñador de la herramienta debe considerar varios factores que pueden afectar la pieza fabricada, como el material plástico, la contracción y el equipo de proceso. Además, las presiones competitivas dentro de la industria del plástico requieren que el diseñador de la herramienta considere cómo facilitar los cambios de herramienta, optimizar el mantenimiento de la herramienta y simplificar (o eliminar) las operaciones secundarias. Históricamente, los moldes y matrices de plástico fueron construidos por fabricantes de herramientas que pasaron sus vidas aprendiendo y perfeccionando su oficio. Hoy en día, el vacío creado por la disminución del número de estos fabricantes de herramientas con formación clásica se está llenando con el desarrollo de centros de maquinaria controlados numéricamente (NC), centros de maquinaria controlados numéricamente por computadora (CNC) y sistemas de diseño asistido por computadora (CAD). Los moldes y matrices ahora se pueden mecanizar en molinos, tornos y máquinas de descarga eléctrica controlados por computadora que requieren comprensión de las computadoras y el diseño, en lugar de años de experiencia y habilidades de mecanizado. La calidad de los componentes de las herramientas ahora depende más del equipo que de la habilidad del fabricante de herramientas. Los altos costos de los moldes y el hecho de que muchos moldes de producción se construyen con limitaciones de tiempo extremas no dejan lugar a prueba y error. Aunque la creación de prototipos se ha utilizado ampliamente para evaluar diseños de piezas más pequeñas cuando las circunstancias y el tiempo lo permiten, la creación de prototipos no siempre es factible para diseños de piezas más grandes. Sin embargo, existen varias alternativas a la creación de prototipos, por ejemplo, CAD, análisis de elementos finitos (FEA) y creación rápida de prototipos. Mientras que CAD permite que un diseñador de herramientas trabaje con un modelo de computadora tridimensional de la herramienta que se está diseñando y analizar el diseño, FEA permite que la herramienta sea evaluada (en una computadora) para determinar su capacidad de producción. Luego, el molde se fabrica a partir del modelo de computadora, un proceso llamado fabricación asistida por computadora (CAM). La creación rápida de prototipos es un método relativamente nuevo de producir una pieza de plástico mediante el uso de un dibujo por computadora en tres dimensiones. Un sofisticado aparato de creación de prototipos interpreta el dibujo y guía un rayo láser articulado a través de un medio específico, como un plástico fotopolimérico o papel laminado, el resultado es una representación física del dibujo por computadora. Las piezas de prototipos se pueden producir en menos de 24 h, y los diseños de piezas se pueden escalar para adaptarse al tamaño del equipo de creación de prototipos. Otra tendencia es la introducción de moldes que aceptan módulos intercambiables. Los módulos tardan menos en fabricarse y, a su vez, reducen el tiempo y los costes de entrega. Además, normalmente se necesita menos tiempo para cambiar el módulo que todo el marco del molde.
Placa de sostenimiento
Tiene dimensiones mayores a lo ancho generando pestañas de ambos lados en donde se montan bridas para sujetar a la platina móvil de la máquina aplicando presión con un tornillo, al centro tiene un barreno por el cual pasa el perno de botado, su grosor dependerá del tamaño total del molde y de la pieza a inyectar evitando esfuerzos y posibles deformaciones o fracturas en la placa. Se encuentra en ambas partes del molde, aunque la de la parte fija contiene algunos aditamentos montados como el sprug, el bebedero y el anillo centrador.
Placas Paralelas
Estas placas sirven como protecciones para los botadores y placas de botado, mantienen al molde unido ya que tienen barrenos pasados por los cuales entran tornillos que unen las placas de la parte móvil, por lo general tienen un acanalamiento en el cual entra parte de la brida de sujeción.
Placa de golpeo
También conocida como cama de botado, es la placa que se encuentra en la parte interior de la cavidad que generan las placas paralelas, la cual sostiene a los botadores, esta placa sirve para desplazar los botadores para expulsión de las piezas inyectadas.
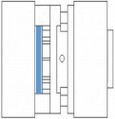
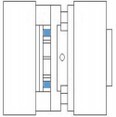
Estos pernos son más largos que los botadores, de forma cilíndrica y su principal característica es que no están en contacto con la pieza inyectada, su función es regresar el sistema de botado del molde, algunos se accionan por contacto con la parte fija, aunque existen otros tipos, el accionado por resortes, los cuales se ponen en la parte de las placas de botado y el ultimo tipo el cual solo son guías para la colocación de la cama de botado, pues el retroceso es generado por el sistema de expulsión de pieza de la máquina ya que en la placa de golpeo se tiene un barreno con cuerda para atornillar el buje de golpeo.
Placa porta botadores
Esta placa sirve para mantener en una posición idónea e invariante a los botadores, con la finalidad de que los botadores no generen problemas al llenar el molde, en algunas placas se tiene sistema de retorno por resortes, los cuales se montan en los pernos de retroceso para regresar el sistema de botado.
Botadores
Son generalmente cilindros metálicos con punta modificada denacuerdo a la forma del inserto en el que se moldea el material, su función es la extracción de las piezas plásticas mediante el contacto directo del botador con la pieza, estos botadores son accionados por el golpeo de un pistón o servomotor con un buje.
Pernos de retroceso
Placa de Enfriamiento
En esta placa se encuentra un sistema de canales por los que circula líquido refrigerante, el cual es una mezcla de agua y aceite soluble, el cual regula y disipa la temperatura del molde en procesos continuos, esta placa se encuentra en ambas partes del molde, cada una detrás de las placas de contacto (porta insertos y porta cavidades), para facilitar el control de la temperatura, por lo general cuando se trabaja con materiales de ingeniería, en la parte fija se utiliza un termorregulador para mantener una temperatura superior y facilitar el flujo del material evitando así posibles defectos de llenado en la pieza.
Placa porta insertos
Insertos
Son las partes que generan la pieza deseada, generalmente son de aceros especiales, se utilizan cuando el molde tiene cajas de insertos, disminuyendo el costo de fabricación de un molde nuevo, estas piezas se introducen a las placas porta insertos por altas presiones, se sujetan por tornillos y cuando se desean extraer únicamente se extrae el tornillo sujetador y se aplica un poco de fuerza. Cabe mencionar que en algunos casos se colocan por medio de expansión térmica, ya que la placa se somete a temperatura para que se dilate y el inserto entre fácilmente, y del mismo modo se extrae.
Pernos guía
Estos pernos se utilizan como referencia al momento de ensamblar (armar) un molde, o en la apertura y cierre del mismo durante el ciclo de expulsión de la pieza, evitan que el molde por cualquier motivo este descentrado y genere problemas al proceso, suelen ser cuatro los pernos utilizados pues ayudan al acoplamiento fino del ciclo arrojando un alto nivel de ajuste evitando también el desplazamiento de las partes hacia algún sentido debido a la presión de inyección a la que es sometido el molde.
Bujes
Son orificios en los cuales corren los pernos guía, los cuales se encuentran de lado de la parte fija del molde, cuentan con un ajuste preciso para evitar el juego entre estos y los pernos, ya que son piezas de ajuste y en ellos radica el correcto acoplamiento de ambas partes del molde. Se colocan por lo general en las esquinas de las placas para un mejor acoplamiento de las partes.
Anillo centrador:
Cada máquina tiene un diámetro diferente en la ranura de la platina fija para el montaje del molde, por consecuente para centrar la boquilla con el bebedero del molde es necesario la aplicación de un anillo centrador. Cuando se fabrica el anillo centrador en la placa fija del molde se tiene mayor precisión en el montaje.
Proceso de produccion de moldes
Normalmente los moldes están hechos de acero especial para moldes, más raramente pueden estar hechos de acero inoxidable, aluminio, aleaciones de cobre, latón. Existen varias tecnologías a través de las cuales hacer los moldes, los más comunes son:
- Fusión
- Fresadora
- Torno
- Electro-erosión
- Rectificación
Normalmente, después de su fabricación, el molde se somete a un tratamiento térmico y las partes más sujetas al desgaste están recubiertas con un material particularmente resistente al deterioro y la oxidación (aleación de níquel o cromado duro). El mantenimiento también es fundamental en el uso correcto de los moldes y una mayor inversión inicial en la construcción del molde se minimiza durante su ciclo de vida, asegurando que las intervenciones de mantenimiento se minimicen. Las dimensiones de cada molde varían dependiendo del número de cavidades que en él se contengan, el tamaño de la pieza, el sistema de enfriamiento, longitud de los botadores y tipo de colada, además del tamaño de las placas de sostenimiento, que son las de mayor longitud, por ello se requiere saber la separación de paralelas y apertura total de platinas para determinar si el molde puede montarse o no en una máquina en específico.
Moldes de inyección
Estos moldes se encuentran entre los más caros, ya que requieren numerosos equipos adicionales, como sensores de temperatura, calefacción y refrigeración, extractores automáticos o respiraderos para la inserción de aire para facilitar la extracción de las piezas. Dado que el proceso de producción puede ser particularmente peligroso debido a las altas presiones y temperaturas involucradas, a menudo están diseñados para ensamblarse en máquinas totalmente automatizadas. En los moldes, el plástico se inyecta a temperaturas de alrededor de 250 grados y a presiones de varias toneladas por centímetro cuadrado. Llenó la cavidad con una cantidad definida de material (poner más podría provocar la ruptura del molde), se inyecta aceite o agua fría para acelerar la extracción. Se abre el molde y se retira la pieza terminada, luego se prepara un nuevo ciclo. Un molde puede alcanzar hasta 150,000 ciclos, a menudo con múltiples piezas producidas en una inyección.
Moldes de moldeo por soplado
Moldeo rotacional
La introducción de material en un molde que gira giroscópicamente se llama moldeo rotacional. Gracias a este proceso, es posible producir objetos monobloque con cavidades internas. El molde está hecho de acero o, más a menudo, de aluminio: este material tiene una conductividad más alta y mantiene el material fluido por más tiempo, asegurando una mejor distribución. Es posible montarlos en estructuras ramificadas para completar múltiples ciclos simultáneamente, siempre que los moldes no sean demasiado grandes. Estos moldes no pueden hacerse concavidades, ni tampoco paredes con espesores diferentes.
Desarrollo de los moldes
El desarrollo de los moldes para este proceso resulta ser una actividad compleja y costosa que lleva mucho tiempo. Por lo tanto, se puede hacer una distinción entre los tipos de moldes utilizados para el proceso de moldeo por inyección:
- Los moldes de acero llamados "herramientas duras", que están hechos de material duro y, por lo tanto, se fabrican utilizando cortadores de control numérico (CNC) o mediante EDM (EDM). Se utilizan para la producción en masa y la realización de millones de ciclos. El problema que presentan es el alto costo (decenas de miles de euros) y el tiempo de entrega para su producción, que a menudo se mide en meses en lugar de semanas o días.
- Los moldes de aluminio llamados "herramientas suaves" están hechos de un material más dúctil y más fácil de trabajar. Hasta unas pocas decenas de miles de piezas moldeadas se utilizan para la producción. Están hechos de aluminio, por lo tanto, son menos costosos (unos pocos miles de euros) y más rápidos de producir (unas pocas semanas).
- Los moldes en material polimérico son adecuados para pequeñas producciones o pre-series porque el material del que están compuestos se degrada rápidamente con las temperaturas y presiones durante el proceso de moldeo por inyección. Tienen costos relativamente más bajos que los moldes de aluminio tradicionales y plazos de entrega de unos pocos días.
Ejector pin o botadores
El proceso de extracción de moldes, inmediatamente después del enfriamiento, es un proceso imprescindible para la correcta separación de las piezas de los moldes. La función de un perno botador es “botar” o expulsar la pieza de plástico al terminar la inyección del polímero dentro del molde, usualmente se fabricados en una sola pieza nitrurados, para incrementar su resistencia.
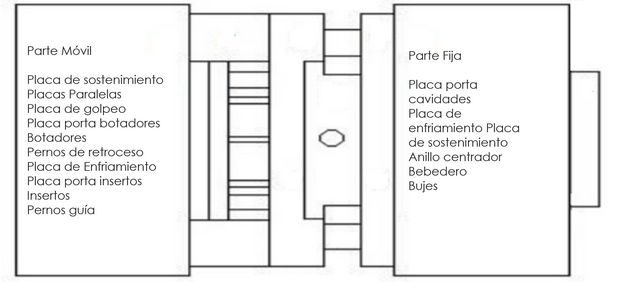
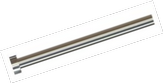
Keywords : Moldes,molds
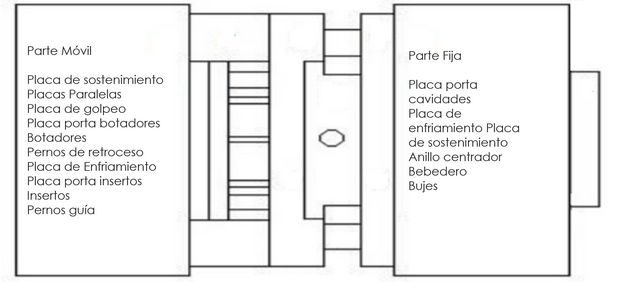
Para el correcto diseño de un molde de inyección es importante tener claro los siguientes pasos :
- Diseñar correctamente el plano de la pieza a inyectar, marcar las líneas de partición, zona de entrada de inyección, posición de los expulsores y cualquier detalle del molde que pueda facilitar su correcta fabricación.
- Según las especificaciones del plástico a utilizar en el molde, hay que tener en cuenta la contracción, características de flujo y abrasión, estructura molecular, comportamiento térmico, viscosidad.
Tomando en cuenta que la fabricación de piezas, equipos y estructuras se hace con herramientas, Las cuales tienen características de especiales de dureza que de acuerdo a su tipo nos ayudan a cizallar; barrenar, golpear, etc., Hay un acero para cada uso. De acuerdo a esto la selección del acero apropiado para cada tipo de molde o herramienta es todo un arte. No es nada fácil establecer una relación directa entre la adición de un aleante específico y la característica del acero que se modifica. Además, hay que tomar en cuenta variables como el procesado y los tratamientos térmicos, que suelen tener gran influencia.
Para fabricar un molde y una pieza de inyección de precisión, los principales puntos a tener en cuenta son la exactitud dimensional con las tolerancias exigidas, el material a utilizar en el proceso de moldeado y el acabado final de la pieza. Los plásticos con baja contracción no presentan problema a la hora de calcular su dimensión final y las dimensiones del molde pueden ser fácilmente calculadas para dar la exactitud final de la dimensión del producto. Los plásticos con alta contracción se deben tomar con más consideración y estudiar más puntos críticos ya que es más complicado a la hora de calcular su reacción. Para la fabricación de moldes para la inyección de plásticos es obligado la utilización de aceros especiales, debido a las cargas a las que son sometidas. Existen una gran variedad de materiales para la fabricación de moldes para la inyección de plásticos Algunos de los aceros utilizados en los moldes para inyección son:
- A2: Acero endurecido a 58-60 Rockwell C, resiste abrasión
- D2: Acero con más contenido de cromo, más resistente a la abrasión y más difícil de mecanizar que A2, más frágil, mejor para piezas pequeñas.
- D7: Acero de muy buena resistencia a la abrasión pero más difícil de mecanizar que A2 y D2.
- ESR es un acero para moldes resistente a la corrosión gracias al templado, muy recomendable para moldes pulido espejo por contenido en cromo y baja porosidad.
- Placas base: 1730
- Placas portamolde: 2311, 2738, P 20
Los costes para la fabricación de los moldes suelen ser altos, ya que los tiempos empleados en la mecanización y ajuste de estos suele ser considerable. Además la exactitud de dimensiones y la calidad superficial suele ser extremadamente laboriosa conseguirla.
Endurecimiento superficial
La competencia entre la dureza de los aceros y su tenacidad es casi tan vieja como el acero mismo. Es fácil hacer que un acero sea duro aunque frágil, o que un acero sea dúctil y tenaz, pero blando. Que sea duro, dúctil y tenaz ya no es tan fácil. Siempre se tiene que llegar a un compromiso porque, de lo contrario, una propiedad afecta a la otra. Como la resistencia al desgaste de los aceros es casi siempre proporcional a su dureza, entre más dura sean las placas del molde, mayor duración tendrá. No sería difícil conseguir aceros y otros materiales durísimos con los cuales fabricar las placas; el problema sería enfrentar su fragilidad. Por un lado hay que fabricar el molde mismo, lo que impone al acero la necesidad de dejarse cortar y maquinar. Luego, el molde mientras se opera, debe ser tenaz para soportar esfuerzos de flexión y torsión de manera permanente, además de impactos ocasionales.