PA 66
Thermoplastics > Polyamides
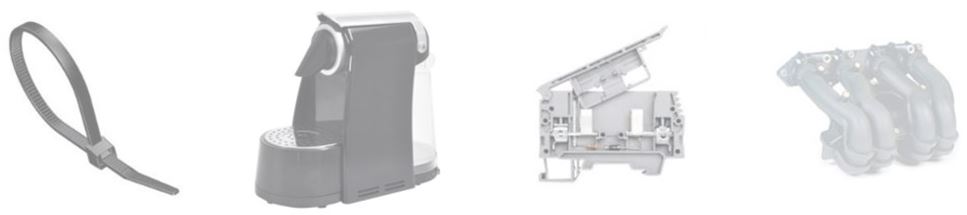
Polyamide 66 - PA6.6 - poli (hexametilenadipamida) | |||||||||
The PA66 if we exclude PA 4.6 is the aliphatic polyamide that has superior characteristics of mechanical strength, such as charge and modulus. Characterized from the amide bond CO-NH, formally derived from the condensation of a carboxylic acid and an amine, on which many of the properties of this type of molecule depend. It is part of synthetic materials more important as thermoplastic, it is a resin that, unlike the PA 6, has greater rigidity, greater characteristics of mechanical strength, has a good resistance to abrasion with a low coefficient of friction and good resistance to organic solvents, excellent dimensional stability and temperature resistance, but has a lower impact resistance (it is more crystalline, and therefore more brittle). The molding cycles are short and through copolymerization, and the loading of fibers, rubber or minerals, can be obtained by degrees with a wide distribution of physical-mechanical and thermal properties. | |||||||||
Symbols | |||||||||
| ![]() | ||||||||
Properties PA66 | |||||||||
| |||||||||
Properties PA66 | |||||||||
Many properties of polyamide are due to the appearance of intermolecular forces between NH and CO groups of contiguous macromolecules. The strongly polar character of the amide groups gives rise to strong attractions between nearby analog groups, establishing, in this way, hydrogen bonds between contiguous molecules aligned. The existence of these hydrogen bridges provides polyamides with a high degree of crystallinity, manifested by high mechanical strengths and melting temperature. The high degree of crystallinity of aliphatic polyamides allows them to be used at temperatures higher than their glass transition (between 35 and 50 ° C) with good mechanical properties up to 190 ° C for PA of type 6.6 and 6. The differences in crystallinity between the polyamides are due to the different proportion between CH2 / CONH groups from one to the other, the odd or even number of carbon atoms and the distance between neighboring macromolecules. The resistance to the traction of the BP diminishes when getting wet, although it increases its tenacity, recovering its primitive properties when drying. It can be said that water acts as a plasticizer that solvates the macromolecules of the polymer and, in fact, there is a considerable increase in volume that must be taken into account in the design of bulky pieces. | ![]() | ||||||||
Physical and mechanical properties PA66 | |||||||||
The main transformation system is injection, although extrusion, extrusion-blow molding and blow molding processes are also viable. They can be welded and pasted. The machining is done with chip removal. The film, the sheets, the bars, the rings and the pipes (plasticized or others) can also be produced by extrusion. Polyamides 6.6 in powder form are also used as protective coatings, such as heat-sensitive powders or in solutions such as glues, waterproofing, etc. Semi-finished parts, sheets, bars and rings are very easy to process mechanically. Dry products are obtained from the transformation. In this state, polyamides do not have the impact and wear resistance that is so highly valued in technical applications. To convert them into suitable material for use, the pieces must be provided with the appropriate water content, equivalent to what they would have under normal conditions, that is, at 23 ° C and at 50% relative humidity, coded at 2.7% for PA 6.6. This humidity contribution is made through the process called "conditioning". This process consists of keeping the pieces submerged in hot water, or keeping them inside a very humid environment. The conditioning will last so much longer (in some cases it can be weeks or months), the greater the wall thickness of the pieces. The humidity is always absorbed by the amorphous zones. If the transformation is carried out incorrectly (excessive temperatures, very long residence of the melt inside the injection unit), the PA can degrade and form harmful vapors, with a very pungent odor (ammonia, amines, aldehydes, etc.). .). In fiberglass reinforced PA, moisture absorption is slightly lower, due to the lower proportion of polymeric material. Also, the variation of characteristics and swelling are reduced, especially in the direction of fiber orientation. | ![]() | ||||||||
Chemical properties | |||||||||
The most interesting feature of the components manufactured from PA is that they resist cracking in the presence of solvents and other aggressive reagents. This is due to the existence of numerous hydrogen bridges, which must be destroyed or replaced in the processes of chemical attack or dissolution. PAs are, in general, attacked by strong inorganic acids (concentrated sulfuric, hydrochloric, trichloroacetic), which yield protons to the nitrogen of the amide group, destroying the hydrogen bridge. Likewise, PAs are attacked by oxidants and, especially, by aqueous solutions of ZnCl2, FeCl3 and CaCl2. Aliphatic PAs are incompatible with concentrated formic acid, formaldehyde, alcohols, phenols and their derivatives. However, they resist the action of acetone well, and saturated and aromatic hydrocarbons, even when subjected to stress. On the other hand, PA is very permeable to water vapor, but it is impermeable to other gases such as O2, N2, CO2, and H2. | ![]() | ||||||||
Polimerization PA66 | |||||||||
PAs of type 6.6 are normally manufactured in two stages. First, the adipic acid and hexamethylenediamine, by heating, form a salt that is called AH and that crystallizes easily. In a second step, the originated salt is introduced in the form of an aqueous solution in an autoclave, under a nitrogen atmosphere, after which the polycondensation is carried out, increasing the temperature to 210-220 ° C and the pressure to 17 bar, until form a precondensate that continues to be soluble in water. Then the temperature is brought to 275 ° C at the same pressure, letting out the water vapor generated during the reaction. Once a yield of 80-90% has been reached, the pressure is canceled and the reaction is terminated under vacuum. In order for the reaction to be carried out, the two reactive terminal groups of a base component must be different from the two terminal groups existing in the second base component. Therefore, to form the macromolecule they must be joined in a strictly alternating manner. ![]() | ![]() | ||||||||
Post-polimerization | |||||||||
| ![]() | ||||||||
Products range PA66 | |||||||||
PA6.6 is offered in a wide variety of grade including no filler / no reinforcement, as well as grade that contains fiberglass, mineral filler, hybrid 2 or more full, with special additives and special lubricant, modified impact and flame retardant. | ![]() | ||||||||
Applications PA66 | |||||||||
PA66 has a wide and general use in automotive air supply, air supply manifolds, transmission systems, pedal box, gear mechanics, pulleys, wheels, rail profiles, threaded rods, clutches, tension chains , motors, covers of air ducts for printed by the swelling, airbag containers, external grids, door handles, wheel covers, mirrors, electricity and electronics, electrical panels of low voltage power distribution, connectors, industrial connections, terminal blocks, the switch of electrical components, the industry in general, tool electrical housings and internal components, sports ski bindings, inline skates, shock absorbers, railway wheels, trucks, various mobile applications, off-piping Shore, packaging films, textile spinning. | ![]() | ||||||||