| Thermoplastic polyurethane
|
|
| 
|
| Product range XTHANE |
|
|
|
In Mexpolimeros a wide variety of thermoplastic polyurethane elastomers TPU’s are available, with hardness values that range from 50 Shore A to 90 Shore D. As discussed earlier the TPUs are available in two classes. The polyester based TPUs have higher tensile strength and better resistance to ozone, oxygen, oil, and solvents than the polyether type TPU’s. However, the etherbased TPE’s have better low temperature properties and better resistance to hydrolysis and microbial attack.
|
| 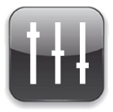
|
| What is Thermoplastic Polyurethane (TPU)
|
|
|
|
TPU is a polyurethane elastomer that is fully thermoplastic. It is a linear segmented block copolymer composed of hard and soft segments. Polyurethanes are characterized by carbamate groups (-NHCO 2 ) in their molecular backbone. In this type of chemical reaction a diisocyanate (OCN-R-NCO) is reacted with a diol (HO-R-OH). The hard segment can be either aromatic or aliphatic in nature. Synthetic polymers, like polyurethane, are produced by reacting monomers in a reaction vessel. Aromatic TPUs are based on isocyanates such as MDI. Aliphatic TPUs are based based on isocyanates like H12 MDI, HDI and IPDI are light stable and offer excellent optical clarity. When these isocyanates are combined with various short chain diols they become the hard block. Normally it is aromatic, but where color and clarity retention during exposure to sunlight is a priority, an aliphatic hard segment is typically recommended. The soft segment can be either polyether or polyester type. Polyester-based TPUs (mainly derived from adipic acid esters), Polyether-based TPUs (mainly based on tetrahydrofuran (THF) ethers). By altering the ratio of the rigid phase, it is possible to vary properties such as hardness, strength, rigidity, extensibility and low-temperature flexibility over a broad range. A distinction is drawn between polyether and polyester polyurethane as a function of the polyols employed.The choice affects the relative suitability for a given application. For use in wet environments, for example, a polyether-based TPU is preferred. When oil and hydrocarbon resistance are primary factors, a polyester-based TPU is the material of choice. Another polyester type, polycaprolactone, also provides oil and hydrocarbon resistance with improved hydrolytic stability.
|
| 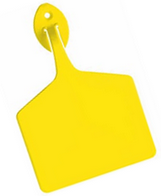
|
| Names - Symbol
| Chemical Formula |
|
|
|
- Thermoplastic polyurethane
- TPU
- TPE-U
- RTPU
- Polycarbamates
- Gross formula: (O- (C6H4) -C (CH3) 2- (C6H4) -CO
- CAS Registry Number 9018-04-6
|
|
| Polyurethane properties
|
|
|
|
| Advantages of thermoplastic urethane elastomers:
- Excellent resistance Oil
- Excellent abrasion resistance
- Burst Pressure resistance: About the same as the ether
- Tube based polyurethane polyester is generally stronger
- High resiliency
- Low temperature performance
- Weather resistance
- Hydrocarbon resistance (polyester-type)
- Hydrolytic resistance (polyether-type)
- Optical clarity (aliphatic type)
- Temperature range: -40°C ÷ 125 °C
- Environmental resistance (humidity, ozone, UVradiation, microbes)
- TPU tube has cost advantage over the pipe polyether based PU
- It is not recommended for use in high humidity or water exposure > 70 ° C
Disadvantages of thermoplastic urethane elastomers:
• poor hydrolysis resistance • poor resistance to chlorinated and aromatic solvents • relatively poor UV light resistance
|
| 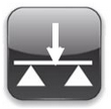
|
| Polyurethane mechanical properties
|
|
|
|
A wide variety of property combinations can be achieved by varying the molecular weight of the hard andsoft segments, their ratio and chemical type, the shore hardness ranges available from 60A to 80D. TPU also offers high tensile strength, elongation , good tear resistance ,good compression set, excellente flexibility without plasticizers, very good abrasion resistance and impact resistance as compared to other TPEs. The compression set is extremely low (20% at 70°C/70h). Due to its high hydrolysis stability, it is especially recommended for use in tropical regions. As compared to chemically crosslinked elastomers the swelling in mineral oils is very small.
|
| 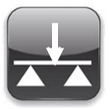
|
| Polyurethane thermal properties |
|
|
|
Both polyester and polyether urethanes work well at elevated temperatures, polyesters already withstand high temperatures and are more resistant to aging heat. Polyethers are much less susceptible to the dynamics of heat buildup. All TPUs become harder and Less flexible at low temperatures and become brittle. The TPU has a brittleness point Tg of -20°C to -40°C depending on the formulation. Application temperatures range from -20°C to +110°C.
|
| 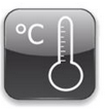
|
| Polyurethane electrical properties
|
|
|
| The electrical conductivity of plastics is very small. The electrical properties of the polyurethanes are not good enough for use as primary insulation, but their general toughness leads to their use in cable jacketing. There is to note that the resestencias and dielectric values depend on the moisture content, temperature and frequency.
|
| 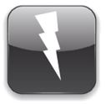
|
| Polyurethane chemical properties
|
|
|
|
The chemical resistance is conditioned essentially by the action time, quantity and concentration of the chemical that acts. Due to its saturated structure TPU has good ozone, weather and temperature resistance. Swelling in mineral oils is relatively low in comparison to many chemically crosslinked elastomers. Gas permeability of TPU is very low (inclination to explosive decompression is not relevant). Polyurethane elastomers is more radiation-resistant than chemically crosslinked elastomers. Generally, the rate of hydrolytic degradation of TPU increases with increasing temperatures. The hydrolysis resistance of the flame retardant halogen free grade is decreased because of the additive. Some polyurethane materials can be vulnerable to damage from heat, light, atmospheric contaminants, and chlorine. For this reason, stabilizers are added to protect the polymer. One type of stabilizer that protects against light degradation , against oxidation reactions, antioxidants are used. Various additives are available for every need. |
| 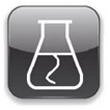
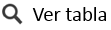
|
| Is thermoplastic polyurethane (TPU) toxic?
|
|
|
|
Each chemical substance and material , polymers or elastomers can be toxic or safe depending on several factors. In general, TPU is not toxic; is safe in many applications. It is even used in biomedical cases. The potential toxicity of polymers may be caused by some factors. The additive used on the materials added to the polymer product may be the source of toxicity. And, the polymer during service and under harsh or natural conditions can be degraded to produce smoke toxic. Burning of TPU produces toxic smokes. For more information you can make reference to MSDS.
|
| 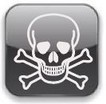
|
| Polyurethane UV radiation resistance |
|
|
|
Aromatic TPU may yellow on exposure to UV radiation. In applications where a TPU be exposed to sunlight, it is best to employ, not yellow or degraded outdoor exposure aliphatic TPU. TPU has excellent ozone resistance even without additional stabilisation while the UV-radiation causes yellowing and surface embrittlement of MDI based thermoplastic polyurethanes, and the mechanical properties are also reduced. To prevents the yellowing we add UV absorbers and HALS , carbon black or pigment to reduce the deep penetration of UV rays and thus mechanical degradation.
|
| 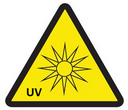
|
| Polyurethane ozone resistance
|
|
|
| Ozone is a powerful oxidizing agent which can decompose the double bonds present in some elastomers. All grades of TPU of us are resistant to ozone and meet VDE requirements 472-805.
|
| 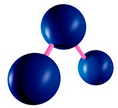
|
| Polyester
|
|
|
| TPU ester is hydrolysis resistant and belongs to the group of polar and saturated elastomers, in fact TPU are compatible with PVC and other polar plastics. Offering value in the form of enhanced properties they are unaffected by oils and chemicals, provide excellent abrasion resistance, offer a good balance of physical properties and are perfect for use in polyblends. Mechanical performance UV stability
|
| 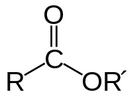
|
| Polyether
|
|
|
| Polyether TPUs are slightly lower in specific gravity than polyester and polycaprolactone grades. They offer low temperature flexibility and good abrasion and tear resilience. They are also durable against microbial attack and provide excellent hydrolysis resistance, making them suitable for applications where water is a consideration. Special additives and raw material makes suitable for use in water, biologically degradable fluids, fire-resistant liquids (HFA, HFB) and mineral oils with additives.
|
| 
|
| Policaprolactona
|
|
|
| Polycaprolactone TPUs have the inherent toughness and resistance of polyester-based TPUs combined with low-temperature performance and a relatively high resistance to hydrolysis. They are an ideal raw material for hydraulic and pneumatic seals.
|
| 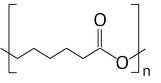
|
| The TPU can also be subdivided into aromatic and aliphatic
|
|
|
|
TPU aromatic - based isocyanates such as MDI products are workhorse and can be used in applications that require flexibility, strength and hardness.
The TPU aliphatic based isocyanates such as H12 MDI, HDI and IPDI are stable to light and have excellent optical clarity. They are commonly used in automotive interior and exterior applications and as laminated films for bonding glass and polycarbonate in the glazing industry. They are also used in projects where attributes as optical clarity, adhesion and surface protection is required. |
| 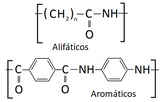
|
| Poliuretano procesability |
|
|
|
TPU estr and ether have smilar processing conditions. The materials are hygroscopic, and must be dried prior to processing 0.05% to prevent loss in molecular weight and physical properties. If the melt contains bubbles, then moisture is probably present. When the material is processed correctly, the melt should appear slightly off-white to a very light yellow color. A mold temperature of between 30°C and 65°C is sufficient for optimum surface appearance and physical properties. Excessive melt temperatures will result in a very transparent , purge shot and sticking to the mold cavities. During shutdown, the barrel should be purged clean with a material such as polyethylene or polystyrene to prevent possible degradation of the material that remains in the barrel. Generally, the TPU’s are quite easy to mold if the material is dry and proper melt temperatures are maintained. Also, it is important to note that most polyurethane do not achieve their ultimate properties for several days. This is due to their rearrangement and ordering of their crystalline structure over a period of time . Toughness and lower compression set can be improved if the parts are annealed at 95°C for 8 to 10 hours.
| | 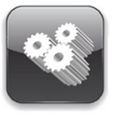
|
| Blend with other polymers |
|
|
| TPU is an outstanding contributor of properties in polymer blends. When added to polymers such as PVC, TPU helps improve toughness, abrasion resistance, low temperature flexibility and compression set. When compounded with polycarbonate, ABS or acetal, a TPU resin with a nominal 18,000 flexural modulus can produce resins with a flexural modulus value of up to 150,000 psi. Specialized resins can be made that blend the properties of engineering plastics with the features and benefits of TPU. Whether for its outstanding abrasion resistance, improved product durability, or ease of manufacturing, TPU is a versatile performer in today’s TPE marketplace. TPU bridges the gap between rubber and plastics. Its range of physical properties enables TPU to be used as both a hard rubber and as a soft engineering thermoplastic.
|
| 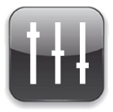
|
| Polyurethane polymerization |
|
|
| Polyurethanes result from the reaction between an alcohol having at least two hydroxyl groups and an isocyanate containing at least two isocyanate groups. As the basic components are polyol, diisocyanate, while low molecular weight diol or diamine act as chain extenders play a very vital role in polyurethanes.
One shot process One-step polymerization is established by simultaneous addition of a polyol, a diisocyanate, and a chain extender stoichiometerically. Polymerization methodology either bulk or solution determine the use of solvent. Solvent is recommended for solution polymerization. Common solvents used in urethane synthesis are dipolar aprotic solvents including N, N'-dimethylacetamide (DMAc), dimethylsulfoxide (DMSO) and dimethyl formamide (DMF). The reaction mixture is heated above 80-100°C.
Two step process However, two-step synthesis is a more common route for manufacturing the polyurethane. This technique is also termed as the prepolymer method. In the first step, a polyol is reacted with excess of diisocyanate to form a NCO terminated oligomer of high molecular mass known as prepolymer, depending upon the polyol’s molecular weight and the ratio between these two reactants. The prepolymer that is formed is usually a sticky liquid, which is easily stored. In the second step, prepolymer is converted in to the final polyurethane by reacting with a diol or diamine acting as chain extender and usually referred to as the chain extension step.
Isocyanates To produce polyurethanes one the most improtant raw material is the diisocyanates. These TPU are characterized by a (NCO) group, which are highly reactive alcohols. The most widely used isocyanates employed in polyurethane production are toluene diisocyanate (TDI) and polymeric isocyanate (PMDI). TDI is produced by chemically adding nitrogen groups on toluene, reacting these with hydrogen to produce a diamine, and separating the undesired isomers. PMDI is derived by a phosgenation reaction of aniline-formaldehyde polyamines.
Polyether polyols The other reacting species required to produce polyurethanes are compounds that contain multiple alcohol groups (OH), called polyols. Materials often used for this purpose are polyether polyols, which are polymers formed from cyclic ethers. They are typically produced through an alkylene oxide polymerization process. They are high molecular weight polymers that have a wide range of viscosity. Various polyether polyols that are used include polyethylene glycol, polypropylene glycol, and polytetramethylene glycol. However, polyether polyols became significantly less expense and have supplanted polyester polyols.
Polyester polyols Polyester polyols may also be used as a reacting species in the production of polyurethanes. They can be obtained as a byproduct of terephthalic acid production. They are typically based on saturated aromatic carboxylic acids and diols. Branched polyester polyols are used for polyurethane foams and coatings. Polyester polyols were the most used reacting species for the production of polyurethanes.
|
|
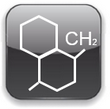
|
| Polyurethane applications
|
|
|
|
Polyester is mainly used where high demands are made on mechanical properties and wear-resistance in addition to good resistance to mineral oil. e.g.: Seals that have to meet high demands on low friction, little wear, high extrusion strength, simple fitting (snap and/or slip-on installation), small size and long service life. Main use: rod seals , piston seals, wipers rotor seals, O-rings
Polyether is mainly used for applications where high hydrolysis stability and chemical resistance (also to many polar hydraulic fluids) are demanded in addition to good mineral oil resistance. Mechanical properties and wear resistance correspond approximately t fulfils the sealing demands for little friction, little wear, high extrusion-strength, simple fitting (snap and/or slip-on installation), small construction size. As well as the additional demands for hydrolysis stability (mining, water hydraulics) and chemical resistance (biologically degradable hydraulic oils).
|
| 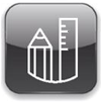
|
| Applications |
|
|
|
Polyurethane systems due to their mechanical characteristics allow the manufacture of automotive interior and exterior parts. It can be used in the manufacture of different parts and components of the car, such as seats, awnings, steering wheels, armrests, boards, among others. Polyurethanes are versatile, modern and safe. They have a huge spectrum of applications to create all kinds of industrial products and basic consumption to make our life more practical, comfortable and respectful with the environment. Typical applications are in the automotive sector, gaskets, construction inserts, appliances , console box, anti-slip, jaws, gaskets, profiles, locks, soft-touch armrests, sleeves, bellows, brackets, spacers, wheels, splash guard, for windows seals, pipe seals, vacuum cleaner seals, power tools, sealing rings, cables, plugs and sockets, cable coverings, switches, enclosures, garden tools, jaws, shock absorbers, "O" Rings, process and conveyor belts, transmission belts / rounded / toothed. The TPU have a minimal recoil of the mold and the extraction of the products from the molds can be carried out without particular difficulty thanks to the excellent recovery of the elastic deformation of the material. Due to the reduced temperatures, the use of TPU compounds in hot water> 70 ° C is not recommended.
|
| 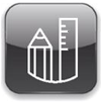
|
| Polyurethane shoes
|
|
|
|
Quality footwear must be comfortable, durable, appropriate to their use and affordable course. Allow the TPU to fulfill all these proprieades. The polyurethanes is lightweight, high abrasion resistance is suitable for manufacturing soles of shoes resistant and offer excellent long - term mechanical properties. TPU soles are practical and waterproof and easy to process. Although its use is more widespread in sports shoes and mountain, it is also used extensively in formal and soles for shoes design and safety shoes with high quality. Polyurethane systems compact and low density are used in making midsoles and outsoles. | |
|
|
|
|
|
|