Polypropylene
Thermoplastics > Polyolefins > Polypropylene
Polypropylene (PP)
Polypropylene (PP) is the partially crystalline thermoplastic polymer, which is obtained from the polymerization of propylene (or propene). It belongs to the group of polyolefins. It can be compared to some extent with the high density polyethylene and is similar manufacturing. Polypropylene has a hardness and superior to those of high density polyethylene but lower impact resistance thermal resistance.
Polypropylene homopolymer
Definition:
is a thermoplastic polymer containing only propylene monomers along the polymer chain. Its structure presents a high degree of crystallinity, resulting in the contribution of stiffness and hardness to the finished piece, but exhibits poor impact resistance at low temperatures and transparency is not sufficient for some applications.
Properties:
Among the features include:
it presents high temperature resistance,
it can be sterilized by gamma and ethylene oxide rays,
has good resistance to acids and bases at temperatures below 80 ° C,
organic solvents it can dissolve at room temperature.
It has good dielectric properties,
Its tensile strength is excellent in combination with elongation,
impact resistance is good at room temperature, but at temperatures below 0 ° C becomes fragile and brittle.
Applications:
Polypropylene Homopolymer mainly has the following applications:
Movie
- Raffia
- Medical products
- Consumer Sector
- Home appliances
- Automotive
Polypropylene copolymer
Definition:
It is a thermoplastic polymer having a higher ethylene content (between 10 and 25%). In the production of high impact copolymer one stage bipolimérica ethylene / propylene rubbery characteristics is formed. They are produced using a cascade reactor system. In the first reactor a homopolymer is obtained with less processing time, which is transferred to a second gas phase reactor where ethylene and propylene are added. These are activated by the catalyst from the first reactor to form the ethylene-propylene copolymer (60% ethylene and 40% propylene) growing inside the polypropylene matrix.
Properties:
It has excellent resistance to low temperatures
It is more flexible than the homopolymer type,
Impact resistance is much greater than the homopolymer
increased when modified with EPDM rubber, also increasing its tensile elongation like; However, chemical resistance is lower than the homopolymer, weakness is accentuated at elevated temperatures.
Applications:
The Impact Copolymer Polypropylene is used in the following sectors:
Consumption sector (pipes, profiles, toys, food containers, boxes, coolers, etc.)
Automotive (Accumulators, boards, etc.)
Appliances (Coffeemakers, faceplates, etc.)
Grades:
By adding from 5 to 30% ethylene in the polymerisation a copolymer having greater impact resistance than the homopolymer PP is obtained. There are , in turn, two types:
random copolymer. Ethylene and propylene are introduced simultaneously in the same reactor, resulting polymer chains in which both monomers alternate randomly.
Block copolymer. In this case the first is carried out the polymerization of propylene in a reactor and then, in another reactor, ethylene polymerizes on PP already formed, thereby obtaining chains homogeneous blocks of PP and PE is added. The impact strength of these copolymers is very high, so they are known as PP or PP impact shock
Modifications:
Reinforcing material and functional additives.
- Fiberglass
- Carbon fiber
- mineral fillers, talc, calcium carbonate, Wollastonite, Mica
- Fiberglass / mineral charges
- Graphit
- Molybdenum sulfide
- Carbon Black
- modificato impact
They can be obtained halogenated flame retardants additives, red phosphorus, halogen-free additives.
- UV stabilizaded
- Tailor made
- PP fiber glass reinforced
These products have been studied in version homopolymer and copolymer to also develop applications high rigidity under conditions of thermal stress. The action of chemical glue, (coupling agent), in combination with the sizings of glass fiber (chopped Strandt) ensure a compound with high mechanical properties . The applied fields of PP reinforced with glass fiber ranging from appliance sectors, (Cuba washers and structural parts), the automotive industry (under hood and internal parts) segments specialized market as pressure pumps, drills and tools generally the following table shows typical values:
PP with talc filler
polymers talc filler show increased elastic modulus and creep resistance, as compared to those loaded with calcium carbonate but dell'impatto reduction. Has a high aspect ratio, it is important to perform a omeogenea mixture during extrusion, and that is why treated powders are used, to avoid weakening because talc. Due to the high thermal resistance alladegradazione surface area talc charged polymers is very low at high temperatures.
PP Calcium Carbonate
Calcium carbonate is the most widely used load in the field of waterproofing membranes that is characterized by
- low cost
- Absence of toxicity (therefore suitable for environments intended to come into contact with humans)
- The white
- low hardness (about 3 on the Mohs scale)
types most commonly used are the soil : before grinding is the removal of impurities such as iron oxides and silica; precipitates can also be used in the case of high purity applications. The surface treatment is performed mainly stearic acid or calcium stearate.
PP Mica
During milling material, no peeling between the layers, thus forming sheets thin way dimensions high aspect ratio aspect ratio and the ease with which the mica sheets oriented with each other, physicochemical properties Mechanical is obtained , alll'orientamento through the sheets into the melt polymer will have increases in the elastic modulus of considerable size, improved with the addition of silane ligands, in contrast has a brittleness of the polymer matrix with a decreased impact. Having a dark color, clear limits its use in specific.
PP with Wollastonite
Wollastonite is a calcium meta silicate, inert, like needles, bianca.Viene used to reinforce the PP, in particular, to reduce costs, improve the physical and mechanical properties such as load characteristics, shape, dimensional stability and thermal, impact resistance, the supericiale appearance, scratch resistance, and to reduce shrinkage.
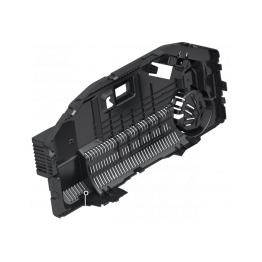
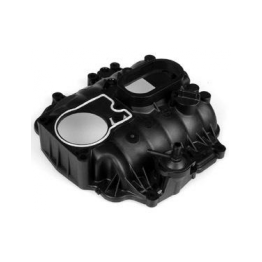

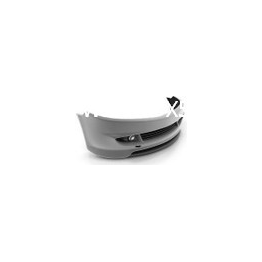