Adhesion
Procesos > ► Adhesión y adhesivos
Adhesión
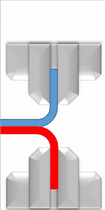
A diferencia de la soldadura, todos los polímeros se pueden unir entre sí y con otros materiales, como madera, textiles, vidrio y metales, mediante el uso de adhesivos, con la excepción de la adhesión con solvente, que estrictamente hablando debe considerarse como un proceso de soldadura. Durante la adhesión, los sustratos no se ponen en contacto directamente entre sí. En este caso, una capa de polímero similar o diferente que puede difundirse parcialmente en la superficie del sustrato es responsable de la unión. No se necesita calor o se necesita muy poco para la adhesión, de modo que la estructura y las propiedades de los sustratos de unión permanezcan sin cambios. A diferencia de la soldadura, la adhesión también se puede utilizar para la unión de grandes superficies, un hecho que tiene una importancia considerable en la industria del embalaje. Las uniones adhesivas pueden ser ópticamente superiores a las uniones soldadas, lo cual es importante con los polímeros transparentes. Sin embargo, la fabricación de uniones adhesivas fuertes a menudo requiere procesos de varias etapas y puede llevar varios días. La resistencia de las uniones adhesivas de polímeros se puede probar de forma no destructiva solo hasta un punto muy limitado. Para unir plásticos se utiliza una amplia gama de adhesivos con varios mecanismos de adhesión y curado (ver ! Adhesivos). Algunos polímeros se pueden ablandar aplicando solventes y luego fusionarlos. Estrictamente hablando, esta técnica debe considerarse como soldadura por difusión. También se emplean con frecuencia adhesivos basados en disolventes que se endurecen por evaporación de los disolventes. Los disolventes también pueden hacer que la superficie de los sustratos de unión se hinche y, por lo tanto, pueden facilitar la difusión mutua de las moléculas del adhesivo y las moléculas del sustrato. Esto solo es posible con termoplásticos. Aunque la adhesión con solventes o adhesivos a base de solventes es simple y económica, a menudo surgen problemas con este proceso debido al envejecimiento de la unión porque el solvente no se puede eliminar completamente de la junta después de la unión. El termosellado y los adhesivos fundidos también han ganado importancia en la unión de plásticos. Las mayores fuerzas de unión adhesiva con polímeros se obtienen generalmente con adhesivos de uno o dos componentes de endurecimiento químico. En la mayoría de los casos, los adhesivos de un solo componente requieren calentamiento para la reacción de curado, mientras que los sistemas de dos componentes también curan a temperatura ambiente. Los procesos de adhesión ahora se pueden automatizar ampliamente. Se pueden realizar procesos de adhesión continuos y tiempos de ciclo cortos, particularmente cuando se utilizan adhesivos termosellados y fundidos. Los polímeros se pueden clasificar por su comportamiento de unión adhesiva como:
- Polímeros de fácil unión
- Polímeros de unión limitada
- Polímeros de unión difícil
Las diferencias en la capacidad de unión se deben a variaciones en la solubilidad de los polímeros y la polaridad de las macromoléculas. Otras influencias son la tensión superficial y, por tanto, la humectabilidad. Un requisito previo para la adhesión es que la tensión superficial del adhesivo sea inferior o igual a la del polímero. Solo cuando esto se aplica, el aglutinante se adapta a los contornos de la superficie sólida durante la etapa de humectación para que puedan ocurrir las reacciones interfaciales físicas y químicas requeridas para una buena adhesión. Solo en los adhesivos a base de disolventes que contienen componentes que se disuelven fuertemente se puede despreciar hasta cierto punto el criterio de humectación. Si la tensión superficial del plástico es inferior a la del adhesivo, la superficie debe prepararse mecánicamente o, en el caso de polímeros de difícil adherencia, debe tratarse químicamente. Los polímeros fácilmente adheribles son: poli(cloruro de vinilo) con bajo contenido de plastificante, poliestireno, poliacrilatos, policarbonatos y poliuretanos, así como resinas de poliéster, epoxi y fenólicas en estado no reforzado y reforzado. Mientras que el poliestireno se puede unir más fácilmente con adhesivos a base de solventes, los miembros restantes del grupo se pueden unir de manera confiable con una variedad de adhesivos sin tratamiento previo o después de la rugosidad mecánica. Las superficies de los sustratos de unión deben limpiarse con solventes o mecánicamente, incluso cuando se trate de polímeros fácilmente adheribles, para eliminar los contaminantes y los agentes de liberación residuales. Los polímeros de unión limitada incluyen PVC con alto contenido de plastificante, que debe limpiarse a fondo con solventes orgánicos antes de la aplicación del adhesivo. El pronunciado comportamiento de contracción e hinchamiento del PVC puede dificultar el uso de adhesivos a base de solventes. El PVC plastificado se puede unir de manera rápida y confiable usando solo solventes (p. ej., tetrahidrofurano). Se encuentran mayores problemas con la adhesión a cauchos sintéticos y poliamida. Este último se puede unir por difusión utilizando ácido fórmico; de lo contrario, se requieren adhesivos de dos componentes que, sin embargo, proporcionan una unión fuerte solo si la superficie del sustrato de poliamida se ha rugoso mecánicamente. Además, la adhesión a la poliamida depende en gran medida de la estructura química del polímero. Los polímeros difíciles de unir incluyen todas las poliolefinas, fluoropolímeros, poliacetales y resinas de silicona. Estos polímeros no se pueden unir en estado no tratado. Las poliolefinas pueden grabarse químicamente y tratarse electrostáticamente mediante el uso de equipos de descarga de corona o tratarse con una llama oxidante. Se debe tener cuidado de que la estructura básica del plástico no sea alterada por el pretratamiento de la superficie. Las mayores dificultades se encuentran en la unión adhesiva de copolímeros de fluoroetileno-propileno y politetrafluoroetileno, que pueden unirse con adhesivos solo después de grabar con sodio en amoníaco líquido o naftalenida de sodio. Aunque ambos procesos son complicados, dan enlaces de alta resistencia mecánica y buena resistencia al envejecimiento. Los desarrollos actuales en adhesivos están relacionados con la mejora de la fuerza de unión, la resistencia y la estabilidad, y con la simplificación de la procesabilidad. Un ejemplo son los adhesivos reactivos de un solo componente a base de cianoacrilatos, que son ideales para unir caucho y cuyo endurecimiento toma solo segundos o minutos. También se pueden alcanzar altas velocidades de fabricación con termosellado y adhesivos fundidos, cuya principal ventaja es su ausencia de disolventes. Los adhesivos fundidos a base de poliamidas, poliésteres lineales o polisulfonas aromáticas muestran una buena estabilidad térmica y tienen tiempos de procesamiento de una fracción de segundo. De los adhesivos de reacción de dos componentes, los poliuretanos flexibles tienen una amplia gama de usos para unir polímeros, incluida la unión de construcción y la fabricación de laminados como materiales de embalaje, láminas de núcleo ligero, láminas de metal laminadas con película y polímeros revestidos de metal.
Adhesión mecánica
En este caso se define la unión entre un adhesivo y una superficie con una cierta
rugosidad, donde, de nuevo partiendo de la base de un mojado adecuado del sólidoo, el incremento en resistencia adquirido sobre substratos de alta rugosidad se
asocia a la mejor disipación de energía plástica durante la fractura al existir una mayor
área de contacto efectivo. Supone la adhesión debida al anclaje mecánico del adhesivo en
las heterogeneidades de la superficie del sólido.
Adhesión electrostática
Explica fenómenos de tipo eléctrico que pueden observarse durante la ruptura de
una unión adhesiva, y considera la transferencia de carga electrostática entre el adhesivo y
el substrato, tomando este sistema como un condensador de placas paralelas,
tal y como describe la doble capa eléctrica eléctrica descrita por muchos autores. Dicha capa, existente en
una interfase metal-disolución, consiste en un exceso o defecto de electrones en el sólido,
y una cantidad equivalente de iones de carga contraria en la disolución, a una distancia (d)
dependiente del radio iónico. El modelo eléctrico, se basa en la
comparación de la unión adhesiva con un condensador plano de placas constituidas por la
doble capa eléctrica establecida al poner en contacto dos materiales de distinta naturaleza,
de modo que se da compartición de electrones. Este modelo muestra poca aceptación, entre otros motivos, ya que la energía
asociada a estos procesos es prácticamente despreciable comparada con la energía de
fractura, y no puede ser tomado como un modelo universal.
Adhesión por difusión
Proporciona un modelo de auto-adhesión en superficies poliméricas, explicando la
dependencia de la unión de polímeros con el peso molecular de los mismos. Se planteó la adhesión entre polímeros debida a la difusión
de partes de las cadenas poliméricas solubles existentes en los planos superficiales,
creándose una nueva zona que es la definida como interfase espesa. Únicamente se
producirá esta difusión de zonas poliméricas desde el seno del adherente hacia el
adhesivo cuando las mismas exhiban un cierto grado de solubilidad y movilidad.
Entre los modelos existentes, los referentes a anclaje mecánico, unión molecular y
adhesión termodinámica han sido objeto de mayor interés por parte de la comunidad
científica en los últimos años, por lo que a continuación se van a describir algunos de los
estudios realizados en estos campos. Además de los mecanismos de adhesión mencionados, se contemplan el mecanismo reológico y la teoría de capas de débil
cohesión. El modelo reológico complementa aspectos no vistos en los modelos
anteriores, como son la influencia de las propiedades mecánicas de los adhesivos y
adherentes, planteando que la energía de fractura en una unión adhesiva viene
determinada tanto por las características superficiales como por las propiedades másicas
de los elementos. Otro aspecto no contemplado anteriormente es la existencia de capas de
débil cohesión sobre el substrato, para lo cual Vickerman46 desarrolló un modelo que
considera la propagación de la fractura no hacia la interfase, sino hacia uno de los
adherentes. Así, define las capas en siete clases, en función de cómo se establecen (por
existencia de aire entre adhesivo y substrato, por migración de sustancias de bajo peso
molecular hacia la superficie, o por la generación de sub-productos de reacción). La
formación de las mismas se deberá a la creación de estructuras, reticulación de
componentes o sobre-tratamiento de las muestras.
Mecanismo de adhesión mecánica
Existen dos tendencias actuales en cuanto a
este mecanismo de adhesión, y son aquella que considera que, mediante este fenómeno,
se logra una elevada resistencia de la unión adhesiva por humectación de la superficie
porosa (madera, porcelana, etc), y la creencia de una unión gracias a la generación de
mayor área de contacto adhesivo-adherente cuando la rugosidad es alta.
Así pues, el tratamiento abrasivo de superficies a fin de crear una elevada
rugosidad superficial sobre materiales lisos para la generación de una mayor resistencia
en la unión adhesiva de los mismos, puede explicarse tanto por el gran área de contacto
inducido como por la creación de sitios radicálicos activos susceptibles de enlace
químico. Es conocida la influencia de fuerzas de interacción secundarias de tipo van der
Waals en los procesos de adhesión, aunque éstas no presentan la fortaleza necesaria para
explicar la unión interfacial entre polímeros. Asumiendo la mayor influencia del enlace
químico frente a la rugosidad superficial, se demuestran la dependencia con las interacciones físicas, mecánicas y químicas de la adhesión de partículas de
aluminio a una matriz epoxídica.
Se observan superficies poliméricas de polisiliconas microestructuradas
mecánicamente, encontrando que la adhesión de las mismas es altamente dependiente de
las fuerzas establecidas en la región existente entre las zonas que no están en contacto
entre los substratos.
En el caso de la adhesión de substratos poliméricos sobre metales, los mecanismos
dominantes en el proceso son la adsorción y anclaje mecánico.
Mecanismo de adhesión química
Este mecanismo es el más ampliamente aceptado, y define las fuerzas
intermoleculares existentes entre adherente y adhesivo como interacciones de tipo dipolo,
van der Waals y químicas, por lo que considera la existencia de grupos polares como
responsable del incremento en resistencia de la unión. De este modo, el modelo considera
la adhesión debida a enlaces de naturaleza covalente (caso de la unión de materiales
elastómeros con adhesivos epoxi) e iónicos.
Es posible postular el tipo de enlaces moleculares que tendrán lugar al poner en
contacto dos superficies, en función de la química de cada una de ellas. Así, en el caso de
la unión por soldadura de metales, se puede hablar del establecimiento de enlaces
metálicos, mientras que en la unión de agentes promotores de la adhesión de tipo
silano existen evidencias de enlace covalente. La
medida aumenta el número de uniones químicas en la zona de contacto entre
substratos, también lo hace la resistencia de la unión, pasando por un máximo, a partir del
cual la resistencia vuelve a disminuir a consecuencia de una concentración de tensiones
excesiva en la interfase.
Otras investigaciones evidencian la dependencia de la resistencia de la unión con
el espesor de la misma, ya que cuanto menor sea ésta, tendrá más capacidad para disipar
tensiones.
Debido a la dificultad inherente a la demostración de la existencia de enlaces
químicos hasta que se han desarrollado herramientas de análisis como la espectroscopia
de masas por tiempo de vuelo de iones secundarios (ToF-SIMS) o la espectroscopia
fotoelectrónica de rayos X (XPS), se encuentran pocas referencias bibliográficas acerca
de este tipo de mecanismo de adhesión.