Líneas de tigre
Procesos > ► Defectos de inyección > ► Defectos de moldeo
Tira de tigre (tiger strips)
El término Líneas de tigre se refiere a la aparición alterna de rayas brillantes y mates perpendiculares a la dirección del flujo en la superficie de la parte moldeada. Se asemejan a los patrones en el pelaje de un tigre y son causadas por el flujo intermitente de la masa fundida, especialmente en termoplásticos compuestos por diferentes monómeros (blends)El defecto aparece como una secuencia repetitiva de ondas y surcos perpendiculares a la dirección del flujo. Este fenómeno ocurre cerca de la salida del troquel, en correspondencia con un esfuerzo cortante crítico a la pared que da lugar a la ruptura de la capa externa, donde lambda "λ" representa la amplitud de las ondas.
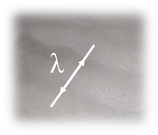
- Inestabilidad interfacial
- Pulsaciones en la presión de fundido
- Temperatura de la resina fundida
La banda de tigre de moldeo por inyección se forma en una placa inyectada junto con la dirección del flujo de las mezclas fundidas indica una fluctuación periódica que repite los grados de brillo más altos y más bajos, que corresponden al período de las porciones brillantes y turbias de la franja de tigre. Etos grados de brillo local dependen en gran medida de las morfologías de las fases dispersas cerca de la capa superficial de la muestra inyectada.
- aumentando el grosor de la capa superficial
- disminuyendo la viscosidad de la capa superficial (aumentando la T de la matriz)
- reduciendo la velocidad de extrusión
- aumentando la brecha del dado (h)
- disminuye cuando el ratio L/D se reduce
- Aumentando fluidez y/o las temperaturas
A medida que aumenta la velocidad de salida del dado, en comparación con las condiciones de flujo estable, llegamos a un punto donde la interfaz adquiere una conformación característica en zigzag (inestabilidad en zigzag).
Inestabilidad de las olas
- se vuelve más pronunciada a medida que aumenta la diversidad entre los grosores de las capas
- puede generarse por grandes diferencias entre las viscosidades extensionales de las capas adyacentes o por una alta viscosidad extensional en la capa externa.
Causas
- Las secciones transversales
del punto de inyección,
bebedero y colada son muy
pequeños
- El diámetro de la boquilla de la
máquina es muy pequeño
- Insuficiente espesor de pared
de la parte moldeada
- Caída de presión muy grande
en el flujo del material
- La temperatura del molde
es muy baja
Solución
Aumentar la temperatura de la masa fundida, subir la temperatura del molde hasta el máximo recomendado, aumentar las secciones transversales de los puntos de inyección y la colada, revisar si es posible aumentar el espesor de pared de la parte moldeada, y instalar una boquilla con un diámetro más grande.