Moldeo por compresión de goma
Procesos > ► Moldeo
Moldeo por compresión
El moldeo por compresión es el método más común mediante el cual se moldean los plásticos termoendurecibles [1-3]. En este método, el plástico, en forma de polvo, gránulo o disco, se seca mediante calentamiento y luego se calienta adicionalmente hasta cerca de la temperatura de curado; esta carga calentada se carga directamente en la cavidad del molde. La temperatura de la cavidad del molde se mantiene entre 150 ° C y 200 ° C, según el material. A continuación, el molde se cierra parcialmente y el plástico, licuado por el calor y la presión ejercida, fluye hacia el hueco del molde. En esta etapa, el molde está completamente cerrado y el flujo y el curado del plástico están completos. Finalmente, se abre el molde y se expulsa la pieza moldeada completamente curada. El equipo de moldeo por compresión consta de un molde adaptado, un medio para calentar el plástico y el molde y algún método para ejercer fuerza sobre las mitades del molde. Para condiciones de moldeo severas, los moldes generalmente están hechos de varios grados de acero para herramientas. La mayoría se pulen para mejorar el flujo de material y la calidad general de la pieza. El latón, acero dulce o plásticos se utilizan como materiales de molde para condiciones de moldeado menos severas o productos de corta duración. En el moldeo por compresión, una presión de 2250 psi (158 kg / cm2) - 3000 psi (211 kg / cm2) es adecuada para materiales fenólicos. La presión más baja es adecuada solo para materiales de fácil flujo y una forma moldeada poco profunda, sencilla y sin complicaciones. Para un material de flujo medio y donde hay huecos, núcleos, formas y pasadores de tamaño medio en la cavidad de moldeo, se requiere una presión de 3000 psi (211 kg / cm2) o superior. Para moldear materiales de urea y melamina, se necesitan presiones de aproximadamente una vez y media que las necesarias para el material fenólico. El tiempo necesario para endurecer los materiales termoendurecibles se denomina comúnmente tiempo de curado. Dependiendo del tipo de material de moldeo, la temperatura de precalentamiento y el espesor del artículo moldeado, el tiempo de curado puede variar de segundos a varios minutos. En el moldeo por compresión de termoendurecibles, el molde permanece caliente durante todo el ciclo; Tan pronto como se expulsa una pieza moldeada, se puede introducir una nueva carga de polvo de moldeo. Por otro lado, a diferencia de los termoestables, los termoplásticos deben enfriarse para endurecerse. Entonces, antes de expulsar una pieza moldeada, se debe enfriar todo el molde y, como resultado, el proceso de moldeo por compresión es bastante lento con termoplásticos. Por tanto, el moldeo por compresión se usa comúnmente para termoendurecer plásticos tales como fenólicos, urea, melamina, y alquidos; normalmente no se utiliza para termoplásticos. Sin embargo, en casos especiales, como cuando se necesita una precisión extrema, los termoplásticos también se moldean por compresión. Un ejemplo son los discos fonográficos de termoplásticos de vinilo y estireno; Se necesita una precisión extrema para una reproducción de sonido adecuada. El moldeo por compresión es ideal para productos tales como interruptores eléctricos y otras partes eléctricas, vajillas de plástico, gabinetes de radio y televisión, cajones de muebles, botones, perillas, manijas, etc. Al igual que el proceso de moldeo en sí, la maquinaria de moldeo por compresión es relativamente simple. La mayoría de las prensas de compresión constan de dos platos que se cierran entre sí, aplicando calor y presión al material dentro de un molde. La mayoría de las prensas se operan hidráulicamente con una meseta que varía en tamaño desde 6 pulgadas cuadradas hasta 8 pies cuadrados o más. Los platos ejercen presiones que van desde 6 hasta 10.000 toneladas. Prácticamente todas las prensas de moldeo por compresión son de diseño vertical. La mayoría de las prensas que tienen tonelajes inferiores a 1000 actúan hacia arriba, mientras que la mayoría de las de más de 1000 toneladas actúan hacia abajo. Algunas prensas están construidas con una disposición de abrazadera de lanzadera que mueve el molde fuera de la sección de abrazadera para facilitar la instalación y extracción de piezas. Los moldes de compresión se pueden dividir en moldes manuales, moldes semiautomáticos y moldes automáticos. El diseño de cualquiera de estos moldes debe permitir la ventilación para permitir el escape de vapor, gas o aire producido durante la operación. Después de la aplicación inicial de presión, la práctica habitual es abrir ligeramente el molde para liberar los gases. Este procedimiento se conoce como respiración. Los moldes manuales se utilizan principalmente para corridas experimentales, para artículos de pequeña producción o para moldear artículos que, debido a la complejidad de la forma, requieren el desmantelamiento de las secciones del molde para liberarlos. Los moldes semiautomáticos consisten en unidades montadas firmemente en los platos superior e inferior de la prensa. El funcionamiento de la prensa cierra y abre el molde y acciona el sistema de expulsión para la extracción del artículo moldeado. Sin embargo, un operador debe cargar el material de moldeo, activar los controles de la prensa para la secuencia de moldeo y retirar la pieza expulsada del molde. Este método es muy utilizado Los moldes totalmente automáticos están especialmente diseñados para adaptarse a una prensa totalmente automática. Todo el ciclo de operación, incluida la carga y descarga del molde, se realiza automáticamente y todas las operaciones de moldeo se controlan con precisión. Los polímeros termoendurecibles se pueden moldear a velocidades de hasta 450 ciclos / h. Las herramientas deben ser del más alto nivel para satisfacer las exigentes demandas de la producción de alta velocidad. Los moldes automáticos ofrecen el método más económico para tiradas de producción largas porque los costos de mano de obra se mantienen al mínimo. Los tres tipos comunes de diseños de moldes son flash abierto, completamente positivo y semipositivo.
Flash abierto
En un molde de flash abierto, se carga un ligero exceso de polvo de moldeo en la cavidad del molde. Al cerrar las placas superior e inferior, el material sobrante se expulsa y se forma una rebaba. El flash incluye el plástico que queda en la cavidad y hace que el émbolo del molde ejerza presión sobre él. El gas o el aire pueden quedar atrapados cerrando el molde demasiado rápido, y el material finamente pulverizado puede salpicar fuera del molde. Sin embargo, si el cierre se realiza con cuidado, el molde flash abierto es sencillo y da muy buenos resultados. Dado que la única presión sobre el material que queda en el molde flash cuando está cerrado resultante de la alta viscosidad de la masa fundida que no consigue que se escape, mediante este proceso sólo se puede moldear resinas que tengan altas viscosidades de la masa fundida. Dado que la mayoría de los cauchos tienen altas viscosidades de fusión, el molde flash se usa ampliamente para producir juntas y ojales, tapones de tina y flash, tacones de zapatos, tapetes para puertas y muchos otros artículos. Debido a que la menor presión ejercida sobre el plástico en los moldes flash, los productos moldeados suelen ser menos densos que cuando se fabrican con otros moldes. Además, debido al exceso de carga de material necesario, el proceso es un poco derrochador en lo que respeta a las materias primas. Sin embargo, el proceso tiene la ventaja de que los moldes son baratos y son necesarios unos costes laborales muy reducidos para pesar el polvo.
Totalmente positivo
En los moldes totalmente positivos no se hace ningún margen para colocar el exceso de polvo en la cavidad. Si se carga un exceso de polvo, el molde no se cerrará; una carga insuficiente resultó en un espesor reducido del artículo moldeado. Por lo tanto, debe usarse una carga correctamente medida con este molde; es una desventaja del molde positivo. Otra desventaja es que los gases liberados durante la reacción de curado químico quedan atrapados en el interior y pueden aparecer como ampollas en la superficie moldeada. El desgaste excesivo de la superficie de ajuste deslizante en las fuerzas superiores e inferiores y la dificultad de expulsar la moldura son otras razones para descartar este tipo de molde. El molde se utiliza una pequeña escala para moldear termoendurecibles, plásticos laminados y ciertos componentes de caucho.
Semipositivo
El molde semipositivo combina ciertas características del flash abierto y moldes totalmente positivos y en cuenta tiene el exceso de polvo y flash [4]. También es posible obtener flash tanto horizontal como vertical. Los moldes semipositivos son más costosos de fabricar y mantener que los otros tipos, pero son mucho mejores desde el punto de vista de las aplicaciones. El funcionamiento satisfactorio de los moldes semipositivos se obtiene teniendo una holgura (0,025 / 25 mm de diámetro) entre el émbolo (fuerza superior) y la cavidad. Además, el molde tiene una conicidad de 2-3 ° en cada lado. Esto permite que el flash fluya y los gases atrapados escapen junto con él, produciendo así un componente de molde limpio y sin imperfecciones.
Aplicabilidad del proceso
El moldeo por compresión es más rentable cuando se usa para piezas de tiradas cortas que requieren tolerancias estrechas, alta resistencia al impacto y baja contracción del molde. Por más antiguo que sea el proceso, las nuevas aplicaciones continúan evolucionando en el moldeado por compresión. Por ejemplo, en los campos médico y dental, los retenedores de ortodoncia y las carcasas de marcapasos ahora se moldean principalmente por compresión debido a los bajos costos de las herramientas. Las herramientas de moldeo por inyección para producir la misma pieza costarían hasta ocho veces más. Los fabricantes de juntas y sellos que comenzaron con productos moldeados por inyección para aprovechar los tiempos de ciclo más rápidos, ahora están volviendo al moldeo por compresión para mantener el nivel de calidad requerido para estas piezas. El uso del moldeo por compresión se ha expandido significativamente en los últimos años debido al desarrollo de nuevos materiales, en particular materiales reforzados. El moldeo de plásticos reforzados (RP) requiere dos matrices emparejadas, generalmente hechas de aluminio, plástico o acero de bajo costo y que se utilizan en tiradas cortas. La adición de cámaras de vacío a los equipos de moldeo por compresión en los últimos años ha reducido la cantidad de defectos causados por el aire o el agua atrapados en el compuesto de moldeo, lo que da como resultado piezas terminadas de mayor calidad. Otra mejora relativamente nueva ha sido la adición de varias formas de automatización al proceso. Por ejemplo, los robots se utilizan tanto para instalar insertos como para eliminar piezas terminadas.
Moldeo por compresión de goma
El moldeo por compresión es el método de producción original para moldear caucho. Es ideal para volúmenes de producción bajos a medios y es un proceso de moldeo particularmente útil para moldear juntas, sellos, juntas tóricas y piezas grandes y voluminosas. Es un método de producción ampliamente utilizado, eficiente y económico para muchos productos, particularmente bajos volúmenes de producción de piezas medianas a grandes y materiales de mayor costo.
Procesos
El moldeo por compresión implica tomar compuesto de caucho o materia prima mezclada y hacer "preformas" que estén cerca de la forma del producto final. Estas formas se cargan, típicamente a mano, en un molde abierto. Se cierra el molde, se cura el caucho y luego se desmolda.
¿Qué tipo de proceso de moldeo es el adecuado para su aplicación?
Hay una serie de factores a considerar al determinar el tipo de proceso de moldeo requerido algunos de estos incluyen:
- El tamaño y la geometría de su pieza
- El peso de tu parte
- El material requerido
- El volumen de piezas requerido
Moldeo por transferencia de caucho
Transfer Molding combina las ventajas del moldeo por inyección con la facilidad del moldeo por compresión. El moldeo por transferencia de caucho es un proceso ideal para moldear piezas que requieren múltiples cavidades, piezas complejas que requieren un molde cerrado, unir piezas de caucho a metal y si la geometría de la pieza puede hacer que las cavidades del molde atrapen aire.
Procesos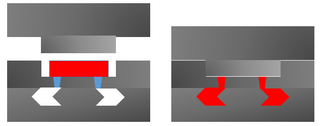
Similar al moldeo por compresión, el moldeo por transferencia requiere una preparación secundaria de la materia prima en "preformas" que se cargan en una "olla". Cuando se cierra el molde, un "pistón" comprime el caucho en el "recipiente" y lo fuerza a través de agujeros o brotes en la cavidad para llenar la cavidad de la pieza. Las ventajas del moldeo por transferencia sobre el moldeo por compresión puede incluir:
- Menos formas previas y más simples porque una forma previa puede llenar muchas de las cavidades
- Control de tolerancia dimensional más estricto porque el molde está cerrado, por lo tanto no se mantiene abierto por exceso de material derrame de la línea de separación de la cavidad durante el moldeo. Esta mantiene la geometría de la pieza más exacta y las líneas de partición más pequeño y menos notable.Las piezas de goma coloreadas se benefician porque las preformas se pueden cortar a mano de las hojas de materia prima, reduciendo significativamente la posibilidad de contaminación que puede venir de la preparación mecánica para
- moldeo por compresión o el tornillo de inyección y barril en moldeo por inyección.
- El material en la "olla" precalienta antes de ser forzado a las cavidades. Esto disminuye la viscosidad del material, lo que le permite fluir más fácilmente en las cavidades para reducir el tiempo de curado. La desventaja principal es el aumento de residuos; El "flash pad" o el caucho que queda en la olla después de la transferencia generalmente se cura y debe descartarse.
El moldeo por compresión se realiza de forma automática. Para esto es necesario utilizar una prensa de moldeo equipada con sistemas adicionales para almacenar cierta cantidad de material de moldeo, medir exactamente la cantidad de polvo de moldeo por ciclo, depositarla dentro de las cavidades del molde, y extraer, finalmente, la pieza moldeada. Con este tipo de prensa el operario sólo debe cargar periódicamente la tolva de alimentación y retirar las piezas moldeadas. En este caso se necesitan producciones suficientemente grandes ya que exige una mayor inversión de capital. Por otra parte, el moldeo automático asegura una producción masiva de artículos moldeados de calidad muy homogénea y con unos costes mínimos de producción. Como principal inconveniente, destacar que el moldeo automático no es practicable cuando la pieza moldeada lleva inserciones, resaltes o taladros laterales.