Piezas Incompletas (Short Shot)
Este es un fenómeno en el cual alguna porción de la pieza moldeada esta faltante o incompleta y es uno de los más frecuentes defectos. Por supuesto, la causa de este defecto viene del hecho de que el material plastificado no alcanza el final de la pieza. La selección de los materiales con buena fluidez y el aumento de la temperatura del plástico y molde son caminos eficientes para corregir este defecto y deben ser hechas como una buena costumbre. El efecto también pude originarse por el uso de una máquina con capacidad de dosificación insuficiente, en cuyo caso se necesita una máquina más grande. Cuando los short shots ocurren, usualmente la resina tiene poca fluidez, la temperatura del canon es insuficiente , la velocidad de inyección es demasiado baja y tal vez el molde cuando la superficie del producto no es plano si no ondulada o presentan múltiples cavidades. Con múltiples cavidades hay diferencia de presión en el cavidades asi que hay piezas completas y piezas incompletas. En moldes de múltiples cavidades, es fundamental la distancia desde el sprue a las entradas de las cavidades sean iguales. Para corregir esto, las entradas de las cavidades que producen short shot deben ser balanzada. Otra razón para estos defectos es el aire en el molde. Los shorts shots causados por esta razón pueden ser detectados si solo una porción de los productos es faltante y las otras partes están completas. Este defecto también ocurre frecuentemente, antes de la inyección existe aire en el molde, si el aire no escapa del molde, el aire es empujado y comprimido por el flujo de plástico o resina por presión y permanece al fin del proceso creando disparos corto o burbujas o quemaduras. Es necesario, entonces, que el aire escape por la línea de partición o crear escape de aire en el molde. Para sacar el aire del molde es efectivo implementar un perno botador, perno ventilador de aire o ventilaciones poco profundas en donde el aire permanece. Si esta parte es la final de la cavidad, implementar pequeñas ranuras que tengan profundidades de 0.01-0.02 mm en la orilla de la cavidad. Estas ranuras son de estas dimensiones ya que es el espacio en donde el termoplástico no puede fluir. En dado caso que no se pueden ser implementar perno botador o ventilador el único modo para corregir este defecto es evacuando el molde antes de la inyección.
Causas
Las causas comunes de los disparos cortos pueden ser una cantidad insuficiente de carga de material en el plastificador, temperatura de fusión es demasiado baja, una temperatura insuficiente del molde combinada con una velocidad de inyección excesivamente lenta, presión de inyección demasiado baja, unas salidas de aire del molde deficientes, conducto de colada o recorrido demasiado estrechos, temperatura de la boquilla demasiado baja.
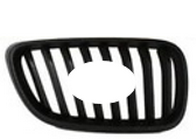
- Cantidad insuficiente de material inyectado
- Velocidad de llenado de inyección insuficiente
- Presión de paquete insuficiente
- Tiempo de inyección insuficiente
- Molde desequilibrado de cavidades múltiples
- Boquilla de obstrucción de material extraño
- Temperatura de stock demasiado baja
- Corredores, puertas, bebederos o conductos de ventilación demasiado pequeños.
- Temperatura del molde demasiado baja
- Capacidad de calentamiento de barriles no deseada
- Desgaste excesivo del tornillo, barril o valor de verificación
Solución
Inyectar mas material, seleccionar una maquina suficientemente potente,
controlar la temperatura de la boquilla, incrementar la velocidad de inyección y modificar el tamaño y la geometría de los canales del molde si fuera necesario.
- Incremento de contrapresión
- Incrementar la presión de inyección
- Aumenta la velocidad de inyección
- Aumenta la temperatura de fusión
- Aumenta la temperatura del molde
- Incrementar la temperatura de la boquilla
- Asegúrese de que el colector y las boquillas hayan alcanzado la temperatura establecida
- Aumenta el tamaño de la toma y confirma el cojín
- Asegúrese de que el moho esté ventilado correctamente y que las ventilaciones estén despejadas
- Confirme que la válvula de retención utilizada no tiene fugas excesivas
- Incremente el interruptor sobre la presión, la distancia o el tiempo
- Cambio de diseño de piezas.
Es posible que las áreas delgadas del molde no se llenen por completo, especialmente si hay una transición gruesa a delgada, o si hay una costilla larga que no se puede ventilar muy bien. Si el diseño de la pieza lo permite, el cambio en estas áreas puede mejorar la situación.