Polimerizaciónes
Procesos > ► Polimerización
Polimerizaciónes
Polimerización "La magnitud del peso atómico determina el carácter del elemento, así como la magnitud de la molécula determina el carácter de un cuerpo compuesto". Dmitri Ivanovich Mendeleev, 1834-1907. Los primeros avances en la tecnología de polímeros se produjeron sin ningún conocimiento real de la teoría molecular de los polímeros. La idea de que la estructura de los polímeros en la naturaleza podría ayudar a comprender los plásticos fue propuesta por Emil Fischer, quien en 1901 descubrió que los polímeros naturales estaban formados por cadenas de moléculas unidas. No fue hasta 1922 que el químico Herman Staudinger propuso que estas cadenas no solo eran mucho más largas de lo que se pensaba, sino que estaban compuestas por moléculas gigantes que contenían más de mil átomos. Las bautizó como 'macromoléculas', pero su teoría no fue probada hasta 1935 cuando se creó el primer plástico con una forma predecible. Esta fue la primera fibra sintética, nailon. Polímero, que significa literalmente muchas partes, es una gran molécula química orgánica (macromolécula), que consiste en una combinación de muchas moléculas químicas pequeñas conocidas como monómeros. Por ejemplo, polietileno (PE), -CH2-CH2-CH2- - - - - -CH2-CH2-, consta de muchos monómeros de etileno, CH2=CH2. El proceso de combinar monómeros para producir una macromolécula se conoce como polimerización. Se utilizan varios tipos de sistemas de polimerización para la conversión de monómero en polímero: polimerización en masa, polimerización en solución, polimerización en suspensión y polimerización en emulsión. El método más simple y directo de convertir monómero en polímero se conoce como polimerización en masa o en masa. Una carga típica podría consistir en un monómero, un iniciador soluble en monómero y quizás un agente de transferencia de carga. Los problemas simples de transferencia de calor y velocidad debido a la cinética de la reacción generalmente crean problemas con la polimerización en masa. Sin embargo, algunos polímeros, como el poliestireno, a veces se fabrican a granel. La adición de disolvente inerte a una masa de polimerización a granel (polimerización en solución) minimiza muchas de las dificultades encontradas en los sistemas a granel. Esto reduce la tendencia a la autoaceleración y el diluyente inerte agrega su capacidad calorífica sin contribuir a la evolución del calor. También reduce la viscosidad de la masa de reacción en cualquier conversión dada. El calor de polimerización también puede eliminarse de forma conveniente y eficaz poniendo a reflujo el disolvente. En la polimerización en suspensión, la eliminación del calor se facilita manteniendo pequeña la dimensión de la masa de reacción. Esto se lleva a cabo suspendiendo el monómero en forma de gotitas en un líquido inerte no disolvente (casi siempre agua). De esta manera, cada gota se convierte en un solo reactor a granel, pero con dimensiones lo suficientemente pequeñas como para que la eliminación del calor no sea un problema, y el calor pueda absorberse y eliminarse fácilmente del medio de suspensión inerte de baja viscosidad. La polimerización en emulsión difiere de la polimerización en suspensión en dos aspectos importantes: el iniciador está ubicado en la fase acuosa y las partículas de polímero producidas son típicamente del orden de 0,1 m de diámetro, unas 10 veces más pequeñas que las más pequeñas encontradas en la polimerización en suspensión. Los sistemas de emulsión permiten producir polímeros de mayor peso molecular a velocidades más altas que los sistemas a granel o en suspensión. Hay dos reacciones de polimerización fundamentales. Clásicamente, se han diferenciado como polimerización por adición y polimerización por condensación. En el proceso de adición, no se desprende ningún subproducto, como en la polimerización de cloruro de vinilo (ver más abajo); mientras que en el proceso de condensación, al igual que en varias reacciones de condensación (por ejemplo, esterificación, eterificación, amidación, etc.) de la química orgánica, se genera un subproducto de bajo peso molecular (por ejemplo, H2O, HCl, etc.). Los polímeros formados por polimerización por adición lo hacen mediante la adición sucesiva de unidades monoméricas insaturadas en una reacción en cadena promovida por el centro activo. Por lo tanto, la polimerización por adición se denomina polimerización en cadena. De manera similar, la polimerización por condensación se denomina polimerización por etapas, ya que los polímeros en este caso se forman por condensación intermolecular, por etapas, de grupos reactivos. Otro proceso de polimerización que ahora ha aparecido como una nueva área de investigación de considerable interés es la polimerización supramolecular. La polimerización es un proceso químico en donde se unen unidades de moléculas iguales (homopolimero) diferentes (co-ter-polímero) uno tras otro para formar una gran cadena con esas unidades. En el proceso de síntesis, que se conoce como polimerización, se obtienen cadenas superiores de polímero. Hay dos tipos principales de polímeros en función de sus métodos de síntesis. Si los monómeros tienen enlaces dobles entre átomos de carbono, a partir de reacciones de adición de los polímeros se pueden sintetizar. Estos polímeros son conocidos como polímeros de adición. En algunas de las reacciones de polimerización, cuando se unen dos monómeros, se extrae una pequeña molécula como el agua. Tales polímeros son polímeros de condensación. Los polímeros se pueden sintetizar con múltiples tipos de reacciones: poliadición, policondensación, poliadición con ataque al isocianato, poliadición con apertura de anillo. Existen muchos tipos de polimerización y varios sistemas para categorizarlos. Las categorías principales son:
- polimerización en suspensión
- polimerización en masa
- polimerización en emulsión
- polimerización en fase gaseosa
- polimerización en solución
- polimerización "paso a paso" o de etapas
Mecanismos de polimerización
Hay dos tipos principales de mecanismos de polimerización: adición (crecimiento de cadena) polimerización y polimerización por condensación (crecimiento escalonado). En la reacción de crecimiento en cadena, la polimerización procede en forma de cadena en una sola dirección. En la reacción de condensación, el crecimiento de la cadena no es espontáneo y generalmente ocurre lentamente: los monómeros primero forman dímeros, trímeros, tetrámeros y oligómeros. Son necesarios tiempos de reacción prolongados para alcanzar polímeros con pesos moleculares medios elevados.
Las técnicas usada en la polimerización de un monómero son:
- Polimerización en masa
- Polimerización en solución
- Polimerización en suspensión
- Polimerización en fase de suspensión
- Polimerización en emulsión
- Polimerización interfacial
- Polimerización en estado sólido
Procesos comerciales de Polimerización
- Proceso de Polimerización en Fase Slurry
- Proceso de Polimerización en Fase Gas
- Proceso de Polimerización en Solución
- Proceso de Polimerización Esferipol
Clasificación de la polimerización
La gran variedad de reacciones disponibles para la preparación de altos polímeros se remonta a dos clases principales: policondensación y poliadición. Los polímeros de adición son aquellas macromoléculas en las que la fórmula química de la unidad de repetición es idéntica a la del monómero utilizado, por ejemplo: polipropileno (C3H6)n, un material ampliamente utilizado, es un polímero de adición obtenido de propileno, olefina de fórmula C3H6. Los polímeros de condensación son compuestos en los que la fórmula química de la unidad repetitiva contiene una cantidad de átomos inferior a la del monómero, o de los monómeros de partida. En cambio, la clasificación se basa en el mecanismo de crecimiento de las macromoléculas y distingue los procesos de polimerización en la polimerización en cadena y en la polimerización en etapas. Esta clasificación permite agrupar adecuadamente todas las reacciones de polimerización conocidas y clasificar mejor sus respectivos productos.
Polimerizaciones en cadena o poliadición
Las polimerizaciones que ocurren con un mecanismo de cadena se pueden clasificar en función de la naturaleza del centro activo que se propaga, en los siguientes tipos:
- Polimerizaciones radicales
- Polimerizaciones aniónicas
- Polimerizaciones catiónicas
- Coordinación de polimerización (metal)
Las polimerizaciones en cadena se caracterizan por reacciones iniciales (con la formación de un centro activo), propagación del centro activo (con crecimiento de la cadena), transferencia de la cadena (con la formación de polímero 'muerto' y un nuevo centro activo y finalmente terminación (con formación de polímero muerto y desaparición de centros activos). La velocidad relativa de estas reacciones, que ocurren en sucesión para una sola cadena, pero en paralelo para diferentes cadenas, determina las características del producto final. Las principales características de los diferentes mecanismos de reacción.
Polimerización por adición (crecimiento de cadena)
Los monómeros de vinilo (moléculas insaturadas, es decir, contienen dobles enlaces carbono-carbono como etileno o estireno) reaccionan mediante polimerización por adición para producir moléculas de cadena larga. Los mecanismos de polimerización por adición son radicales libres, aniónicos y catiónicos. Las polimerizaciones de radicales libres, aniónicas y catiónicas incluyen todas tres etapas: iniciación, propagación y terminación. La iniciación implica la división de las moléculas del iniciador en radicales libres mediante la aplicación de calor a una cierta temperatura, los radicales libres del iniciador luego reaccionan con las moléculas de monómero, comenzando la formación de cadenas de polímero. Los ejemplos de iniciadores incluyen peróxido de benzoílo, (C6H5COO)2 y azo-bis (iso-butironitrilo) (AIBN), (NCC (CH3)2N)2. Por ejemplo, peróxido de benzoílo: el monómero de vinilo es asimétrico con respecto a sus extremos: una cabeza (el átomo de carbono con el grupo R unido) y una cola (el átomo de carbono sin el grupo R). La adición de monómeros durante el proceso de propagación es predominantemente por unión de cabeza a cola debido a efectos estéricos y de resonancia. Una diferencia principal entre la polimerización por radicales y el método iónico es que, en el último, el monómero entrante debe encajar entre el extremo de la cadena en crecimiento y un ion o complejo asociado. La cadena de radicales en crecimiento, por otro lado, no tiene tal impedimento en el extremo de crecimiento.
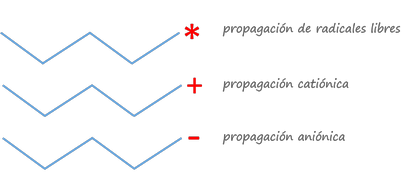
La transferencia de cadena al polímero también puede ocurrir como una etapa de propagación en la polimerización. Este es el proceso en el que un radical de cadena en crecimiento se transfiere al centro de otra cadena de polímero, formando ramas en las cadenas de polímero, lo que puede conducir a una reducción del punto de fusión y la resistencia mecánica del polímero. La ramificación es especialmente frecuente en la polimerización por radicales a alta presión de etileno, utilizado en la polimerización de LDPE. La etapa de terminación implica la reacción de dos radicales libres entre sí, ya sea por combinación o desproporción. La combinación implica el acoplamiento de dos radicales de cadena de polímero en crecimiento. La desproporción es una forma bastante complicada en la que dos cadenas de polímero en crecimiento se vuelven inactivas: cuando dos extremos de cadena en crecimiento se acercan, las cadenas de electrones no apareados se intercambian de una manera tal que la primera cadena gana un elemento H de la segunda cadena, y se forma un doble enlace en la cabeza de la segunda. En presencia de Ziegler-Natta u otros catalizadores estereoespecíficos, se une una cadena de polímero en crecimiento al átomo de metal del catalizador y la posterior adición de monómero se coordina con el átomo de metal, lo que se conoce como polimerización de coordinación, y conduce a una polimerización altamente estereoespecífica. . La molécula de monómero debe sentarse en una posición bastante específica para reaccionar, lo que permite la producción de polímeros estereorregulares. Por ejemplo, la polimerización de propileno mediante la acción del catalizador de titanio da un producto isotáctico; mientras que el catalizador a base de vanadio da un producto sindiotáctico.
En la polimerización de coordinación, el proceso se basa en el sitio y está regulado por el tipo de sitio activo, mientras que en la polimerización por radicales libres el sitio de polimerización se aleja progresivamente del iniciador y no está influenciado por la estructura química del iniciador, por lo tanto, es el tipo de monómero en lugar del iniciador que dicta el proceso de polimerización por radicales libres. La naturaleza flexible y dinámica del sitio de radicales libres puede provocar la formación de ramas laterales mediante un proceso de transferencia de cadena interna conocido como murmuración, que genera un sitio de radicales libres dentro de la cadena de polímero en crecimiento. Esto es mucho menos probable en la polimerización por coordinación ya que no hay radicales libres involucrados en este mecanismo y el sitio activo de la cadena en crecimiento está en una ubicación fija en la superficie metálica del catalizador de coordinación. La terminación en la polimerización de coordinación se logra mediante reacciones del extremo reactivo de la cadena con una molécula modificadora añadida (un agente de transferencia de cadena), por ejemplo, hidrógeno, a una concentración de un hidrógeno por 1000 moléculas de etileno. El uso de hidrógeno proporciona una reacción limpia de bajo costo (sin residuos) para controlar el peso molecular. La temperatura afecta estos procesos: una temperatura más alta aumenta la velocidad de las moléculas y provoca más colisiones, por lo tanto, aumenta la velocidad de reacción. Sin embargo, la reacción del hidrógeno aumenta aún más rápido, lo que da como resultado un mayor grado de terminación que produce un polímero con un peso molecular medio bajo (alto índice de fluidez en estado fundido).
Polimerización con precipitación de polímeros
Se facilita la separación del polímero. El proceso de Spheripol es importante para la obtención de gránulos esféricos de polipropileno.
Polimerización a partir de monómeros gaseosos
Se trata de polietileno. La técnica de lecho fluidizado se usa con catalizadores sólidos sobre los que crece el polímero.
Grado de polimerización
- oligómeros 2 <n <10
- polímeros bajos 10 <n <100
- polímeros promedio 100 <n <1000
- polímeros altos n> 1000
Polimerización escalonada
La polimerización escalonada o "step" se produce mediante una reacción escalonada entre grupos funcionales de reactivos. La reacción conduce sucesivamente de monómero a dímero, trímero, tetrámero, pentámero, etc., hasta que finalmente se forma una molécula de polímero con un gran DP. Sin embargo, tenga en cuenta que las reacciones ocurren al azar entre los intermedios (por ejemplo, dímeros, trímeros, etc.) y el monómero, así como entre los propios intermedios. Por lo tanto, en cualquier etapa, el producto consta de moléculas de diferentes tamaños, lo que da un rango de pesos moleculares. El peso molecular promedio se acumula lentamente en el proceso de polimerización por etapas, y se forma un producto de alto peso molecular solo después de un tiempo de reacción suficientemente largo cuando la conversión es superior al 98%. Dado que la mayoría (aunque no todos) de los procesos de polimerización por etapas implican reacciones de policondensación (condensación repetida), los términos polimerización por etapas y polimerización por condensación se utilizan a menudo como sinónimos. Considere, por ejemplo, la síntesis de una poliamida, es decir, un polímero con amida (–CONH–) como enlace característico. Si comenzamos con, digamos, hexametilendiamina y ácido adípico como reactivos, el primer paso en la formación del polímero (nailon) es la siguiente reacción que produce una monoamida, la reacción continúa paso a paso para dar la poliamida nailon-6,6.
Polimerización por condensación (crecimiento por etapas)
Los monómeros multifuncionales reaccionan produciendo en etapas, dímeros, trímeros, tetrámeros, oligómeros (que constan de 10 a 20 unidades de monómero) y moléculas de polímero. Durante el proceso, se forman enlaces como éster y amida y se elimina una molécula pequeña, por ejemplo, H2O. Los poliésteres contienen el grupo éster, -COO-, que se forma a partir de la reacción entre un ácido carboxílico y un alcohol. Ambos reactivos deben tener dos extremos reactivos (grupos funcionales) para permitir el crecimiento de una cadena. Poli (tereftalato de etileno) (PET) elaborado a partir de ácido tereftálico (ácido benceno-1,4-dicarboxílico) y etilenglicol (etano-1,2-diol): Las poliamidas contienen el grupo amida, -CONH-, un producto de la reacción entre un ácido carboxílico y una amina. Ambas moléculas deben tener una funcionalidad de dos, para que sea posible el crecimiento de la cadena. Los nylons son poliamidas sintéticas hechas de una variedad de ácidos dicarboxílicos y diaminas. Por lo general, dependiendo del número de átomos de C en la amina y los nailon ácidos se designan con números, por ejemplo, "Nylon 4,6 o Nylon 46 o PA46" indica que está polimerizado a partir de una diamina de 4 carbonos y un diácido de 6 carbonos. Kevlar es otro ejemplo, hecho de ácido tereftálico (ácido benceno-1,4-dicarboxílico) y 1,4-diaminobenceno.
Procesos de polimerización
El proceso de polimerización requiere una cantidad de monómeros y un sistema iniciador/catalizador adecuado para iniciar la reacción para formar moléculas de polímero que consisten en miles de monómeros unidos entre sí. Los procesos de polimerización se pueden clasificar en términos del medio de reacción: masa, solución, suspensión, lechada, emulsión y gas.
Polimerización en masa
La polimerización del monómero líquido o gaseoso puro se denomina polimerización en masa. Puede utilizarse para la producción de polímeros de radicales libres y algunos polímeros de condensación. En la reacción solo están presentes monómero, polímero e iniciador y, por tanto, se obtiene un producto muy puro. La polimerización es muy rápida y fuertemente exotérmica. Puede provocar una acumulación peligrosa de temperatura y reacciones de fuga. El sobrecalentamiento puede causar ramificación y reticulación y conducir a la formación de geles. Se utiliza industrialmente para la producción de PS, PVC, PMMA, PET, PA-6.6, PE (alta presión). Sus ventajas son la ausencia de disolvente (lo que implica costes, producción de contaminantes y debe recuperarse posteriormente), y el hecho de que la polimerización se realiza in situ, directamente en el molde (especialmente ventajoso para el PMMA). Los principales inconvenientes se deben al aumento de la viscosidad (en poco tiempo), la dificultad para disipar el calor que se produce durante la reacción, el escaso control de las variaciones dimensionales (diferente densidad), y la imposibilidad de realizar reacciones en las que el disolvente tiene una parte activa. Como característica, el iniciador debe ser soluble en el monómero de partida (la mayoría de los monómeros son apolares). Para evitar fenómenos de autoaceleración se utilizan agentes de transferencia de cadena. El proceso produce polímeros altamente transparentes: por ejemplo, PS y PMMA.
Polimerización en solución
El monómero se agrega a un solvente inerte con un punto de ebullición que corresponde a la temperatura de polimerización. - Durante el proceso de polimerización se evapora algo de disolvente y así ayuda a eliminar el calor de polimerización. Dado que el punto de ebullición del disolvente es constante, esto asegura una temperatura de polimerización constante. Alguna dificultad radica en la separación del disolvente residual del polímero una vez completada la polimerización. En comparación con la polimerización en masa, la polimerización en solución ofrece un control de temperatura más fácil debido a la capacidad calorífica añadida del disolvente y la menor viscosidad.
Polimerización en suspensión
La polimerización en suspensión es esencialmente una polimerización en masa que se lleva a cabo en gotitas en una solución acuosa en la que se dispersa el monómero. El polímero precipita como partículas esféricas finas con diámetros de 0,01 a 1,0 mm. La polimerización comienza por iniciadores de radicales en las gotitas de monómero. Se añaden coloides protectores para evitar la coagulación de las partículas y producir partículas poliméricas uniformes. El agua absorbe el calor de reacción. Se utiliza en la fabricación de PVC y PS. Es necesario eliminar los aditivos residuales. El proceso se utiliza principalmente en la producción de poliolefinas. El catalizador se dispersa/disuelve en un diluyente líquido en el que se disuelve el monómero, o en el monómero líquido por sí mismo. Como en la polimerización en emulsión, el polímero no es soluble en el medio de reacción y precipita sobre la suspensión que forma el catalizador. Se utiliza para PS, PVC, PMMA, fuertemente reacciones exotérmicas. Para facilitar la eliminación del calor, se crea una suspensión en un medio dispersante que tiene una determinada viscosidad. El sistema se fragmenta en masa, formando perlas de unos pocos mm de diámetro. Cada partícula tiene un comportamiento cinético como el proceso en masa. Ventajas • Facilidad de evacuación del calor. Desventajas • eliminación de estabilizadores; • agitación rigurosa. Como característica, se utiliza como dispersante agua estabilizada por caolín, jaleas coloidales y otros, y esto también es importante para la morfología de las partículas poliméricas obtenidas (separadas o coalescidas entre sí). El iniciador y el monómero deben ser insolubles en agua (medio dispersante), y el iniciador debe ser soluble en el monómero.
Polimerización en emulsión
Como en la polimerización en suspensión, el monómero también se dispersa en agua pero en gotitas mucho más pequeñas creadas con el uso de emulsionantes, por ejemplo, jabones. En presencia de agua jabonosa, los productos químicos, como las gotas de monómero y las moléculas de polímero formadas posteriormente, se mantienen separados y se dispersan en lugar de fusionarse en un bulto inútil. El control de la temperatura es más fácil, ya que la viscosidad cambia muy poco con la conversión. Además, la conductividad térmica y el calor específico del agua son más altos que los de los disolventes orgánicos. Algunas de las partículas de tensioactivo (emulsionante) se amontonan formando micelas, otras rodean las partículas de monómero y las aíslan como gotitas. Las micelas constan de 10 a 100 moléculas de jabón con sus grupos hidrófilos en el exterior en la fase acuosa y sus grupos hidrófobos en el interior rodeando los monómeros hidrófobos. Una vez que comienza el proceso, la temperatura aumenta generando radicales libres que atraen a los monómeros y salen de las gotitas y comienzan a agregarse a ese sitio de radicales libres en una micela y finalmente terminan de producir moléculas de polímero que quedan atrapadas en la micela. Por supuesto, este proceso tiene lugar simultáneamente en muchas micelas diferentes que dan como resultado muchas partículas de polímero.Al final del proceso, así como las partículas de polímero, todavía hay algunos monómeros, iniciadores y radicales libres sin reaccionar, que tienen dificultades para participar en la reacción. por razones de obstáculos estéricos. Los residuos de tensioactivos y coagulantes son difíciles de eliminar y también contribuyen a altos niveles de impurezas. Se utiliza principalmente para la producción de acetato de polivinilo, PMMA y PVC. Se utiliza para PS, PVC, PVAc. Ventajas • baja viscosidad • alta vp y DP n simultáneamente. Inconvenientes • presencia del tensioactivo (el látex debe estar coagulado). Se lleva a cabo en un sistema de dispersión en base agua; el monómero no es soluble en agua, pero el iniciador sí lo es. Esta técnica permite obtener altas PM y altas vp. Para una polimerización en emulsión además de agua, monómero e iniciador, es necesario añadir un emulsionante, normalmente un tensioactivo: cuando éste entra en el agua que contiene monómero, se forman micelas, con cabezas polares por fuera y colas apolares por dentro. . Una parte de estas micelas estabilizará gotitas de monómero (y posteriormente de polímero), actuando como reactores; en cambio, algunas gotas grandes contendrán solo el monómero, actuando como reservorios. Luego hay una cantidad de emulsionante que se dispersa como una sola molécula. El iniciador, en fase acuosa, dará lugar a los radicales que se desplazan hasta alcanzar las partículas monoméricas (gotas), y en este punto se iniciará la polimerización radicalaria.
Polimerización en fase gaseosa
El monómero está en estado gaseoso y se usa un catalizador de coordinación heterogéneo tal como un catalizador Ziegler-Natta. En los procesos en fase gaseosa y en suspensión, los catalizadores como Ziegler-Natta y los metalocenos deben apoyarse en una sustancia adecuada, por ejemplo, SiO2, mientras que se pueden agregar directamente en la polimerización en solución. El polímero se forma en los sitios activos del catalizador en una partícula de catalizador-polímero que se expande gradualmente y, como en la polimerización en emulsión, hay un centro activo en cada partícula. El monómero gaseoso fresco se difunde a través de la partícula de polímero para alcanzar el sitio activo. En los reactores, el catalizador está soportado / uniformemente disperso por agitación mecánica o por fluidización. Las técnicas de procesamiento en fase gaseosa y lodos se utilizan principalmente para la producción de poliolefinas como el HDPE.
Reactores de polimerización
Los reactores de polimerización empleados industrialmente incluyen Tanques de agitación horizontal / vertical, reactores de tubo de alta presión, de bucle y de lecho fluidizado, así como polimerización en moldes, por ejemplo, RIM (moldeo por inyección de reacción). El tipo de reactor utilizado viene determinado por el proceso de polimerización. Por ejemplo, los reactores de tanque agitado son adecuados para polimerizaciones en suspensión y emulsión, ya que la agitación ayuda a controlar el tamaño de las partículas del polímero, por ejemplo, en la producción de PVC. La mayoría de las poliolefinas se producen utilizando un reactor de lecho fluidizado. El diseño de la placa distribuidora fluidizada en la base de un reactor es importante para la eficiencia del proceso: la fluidización debe evitar que las partículas calientes del polímero se depositen en la placa y provoquen la aglomeración, al mantener suficiente gas reciclado y gas de alimentación adicional. El flujo de gas, que consiste en monómero / comonómero, hidrógeno, nitrógeno (gas portador inerte) y agente de condensación inerte, proporciona monómero / comonómero para la polimerización, agita el lecho y elimina el calor de polimerización. La temperatura de funcionamiento es de aproximadamente 90°C para LLDPE y 100°C para HDPE y la presión de aproximadamente 10 bar (1 MPa). El gas con algunas partículas de polímero/catalizador sube a la sección abovedada agrandada, conocida como zona de desconexión, donde se produce una variación en las velocidades y las partículas arrastradas se separan del gas, antes de que el gas abandone el reactor y regresen a la zona de reacción. . El agente de condensación puede ser monómeros y líquidos inertes (por ejemplo, pentano, isopentano, butano, hexano) y su calor de vaporización da como resultado el enfriamiento del reactor. El punto de ebullición del líquido condensable tiene que ser más bajo que la temperatura operativa de polimerización, para un control efectivo de la reacción. El gas que sale de la parte superior del reactor se condensa en el intercambiador de calor y se devuelve al reactor en forma líquida. El polvo de polímero pasa a un recipiente de purga donde un agente desactivante (la relación en peso del agente desactivante al catalizador es aproximadamente 0,001) elimina toda la actividad del catalizador, el nitrógeno elimina las trazas de monómeros del polvo caliente y una pequeña cantidad de vapor (un pocos kg/h) elimina el trietilaluminio (TEA) y otras sustancias químicas no monoméricas. El acabado de los polímeros incluye la adición de aditivos (por ejemplo, calor, UV y quizás otros estabilizadores, lubricantes, pigmentos, colorantes, etc.), secado, extrusión y granulación. El polímero puede entrar en la extrusora bastante caliente y, por lo tanto, puede necesitar enfriamiento, en lugar de calentar, a lo largo del cilindro de la extrusora. La temperatura del agua de enfriamiento para la peletización es crítica: el enfriamiento/solidificación rápido y/o lento puede producir pellets con defectos.
Proceso tubular de alta presión
El proceso tubular de alta presión es típico para la producción de LDPE. En este proceso, el monómero de etileno se comprime gradualmente a un nivel de presión adecuado para la reacción, hasta 3000 bar (300 MPa) con un reactor tubular. La polimerización por radicales libres se inicia a aproximadamente 150°C, utilizando oxígeno o un peróxido orgánico como iniciador. La temperatura de la reacción de polimerización puede alcanzar un máximo de más de 300°C. Una mezcla de polímero y monómero sin reaccionar se transporta desde el tubo de reacción a una parte de separación y reciclaje, que incluye un separador de alta presión (HPS). El HPS está conectado a un separador de baja presión (LPS) para una mayor eliminación de monómeros. La fase de polímero fundido resultante se pasa del LPS a una sección de acabado de polímero para extrusión. El monómero sin reaccionar separado en HPS se recicla a una presión similar a la de la salida del compresor primario y se combina con la alimentación que contiene monómero que pasa del compresor primario al secundario. El monómero sin reaccionar del LPS se recicla a través del compresor primario. El agente de transferencia de cadena (CTA) también se agrega al circuito y se transporta al reactor. La CTA se usa para reducir el peso molecular (MW) y para estrechar la distribución del peso molecular sin cambiar la tasa general de conversión de monómero en polímero (usar más iniciador es otra forma de disminuir el MW, pero la velocidad de reacción aumentaría proporcionalmente con un riesgo de una situación peligrosa que surja).
Polimerización industrial
El corazón de cualquier planta de polímeros es la sección del reactor donde el monómero se convierte en polímero. En el caso de la polimerización, el reactor adquiere una importancia adicional porque es aquí donde se establecen en gran medida las propiedades últimas del polímero tales como el peso molecular, la estructura molecular, la distribución del peso molecular, la composición del copolímero, etc. Para lograr estas propiedades en el grado deseado, el reactor debe satisfacer lo siguiente: (a) eliminación eficiente de calor, (b) proporcionar el tiempo de residencia necesario, (c) proporcionar una mezcla uniforme para un buen control de temperatura y homogeneidad del reactivo, y (d ) controlan el grado de retromezclado en una polimerización continua.
Eliminación de calor
Los procesos de polimerización van acompañados de liberación de calor. Todos los monómeros vinílicos comunes generan aproximadamente la misma cantidad de calor durante la polimerización sobre una base molar. Para el PVC de poli (cloruro de vinilo), es de aproximadamente 23 kcal/mol o 650 Btu/lb, y para el estireno, es de 17 kcal/mol (300 Btu/lb). El calor se libera en un período corto de 5 a 10 horas y, además, la liberación máxima de calor puede ser varias veces mayor que este promedio. Para eliminar este calor liberado, los reactores de polimerización generalmente están encamisados y enfriados por agua. Los reactores de polimerización generalmente se construyen de acero inoxidable o acero al carbono revestido de vidrio. La tasa de transferencia de calor en el primero es mucho más alta que en el segundo. Por lo tanto, el coeficiente de transferencia de calor general para un recipiente de acero inoxidable puede ser tan alto como 125 Btu/(h)(°F) (ft2), en comparación con 55-70 para un recipiente revestido de vidrio. La diferencia surge de la resistencia adicional a la transferencia de calor que ofrece la capa de vidrio. Por lo tanto, siempre que se requiera un revestimiento de vidrio para reducir el ensuciamiento del reactor, solo se debe especificar el espesor mínimo del vidrio. La eliminación del calor es relativamente fácil en los reactores pequeños, pero se convierte en un problema en los más grandes, ya que la relación entre la superficie de la camisa de enfriamiento y el volumen del recipiente se vuelve más pequeña con el tamaño más grande. Cuando se aumenta la escala de un recipiente cilíndrico manteniendo la similitud dimensional, el aumento en el área de transferencia de calor es proporcional al aumento de volumen elevado a la potencia 0,67. Los hervidores grandes requieren, además de las camisas de enfriamiento, la provisión de ayudas adicionales para eliminar el calor. Con la polimerización en suspensión, esto se logra comúnmente mediante deflectores de enfriamiento. En este caso, los deflectores previstos para la agitación también están hechos para servir como auxiliares de enfriamiento. Dos tipos comunes de deflectores de enfriamiento son (a) deflector de enfriamiento tipo tubería de entrada inferior, montado a través del fondo y (b) deflector de enfriamiento de placa, montado a través de la pared lateral con camisa y extraíble a través de la boca de inspección. Otro método de enfriamiento suplementario que se utiliza con frecuencia es mediante el uso de condensadores de reflujo. La presencia de un diluyente o disolvente, que hierve más bajo que el monómero o forma una mezcla azeotrópica, ayuda a eliminar el calor mediante el reflujo. La eliminación del calor es más fácil en la operación semicontinua, donde el monómero y el iniciador se agregan gradualmente, y es aún más fácil en la operación continua.
Agitación del reactor
Un aspecto importante del diseño y la ampliación del reactor de polímero es la agitación. Se utilizan varios tipos de agitadores, desde hélices de tipo marino, turbinas de palas planas y turbinas inclinadas hasta tipos de impulsores de alto cizallamiento. Debido a la erosión, existen limitaciones prácticas de velocidad máxima que no deben excederse. Estos corresponden a 1200 pies/min para turbinas de palas planas o inclinadas y 1800 pies/min para turbinas de curva en retroceso con vidrio.
Tiempo de residencia
La duración de la polimerización tiene una influencia significativa en las propiedades del polímero, como la distribución del peso molecular, el tamaño de partícula, la superficie de la partícula, la configuración o la composición. La permanencia excesiva en el reactor de polimerización da como resultado "puntos duros". El fenómeno de los puntos difíciles es familiar para todos los interesados en el control de calidad. En la fabricación de PVC, los puntos duros significan partículas de superficie cerrada que no pueden absorber el plastificante. En otros casos, como el poliestireno o el polietileno, los puntos duros son partículas de polímero de alto peso molecular o reticuladas que no se derriten tan fácilmente como la porción principal del lote. Para reducir la formación de puntos duros, las calderas deben limpiarse frecuentemente con agua a presión, vapor o solvente. A este respecto, la polimerización discontinua tiene ventaja sobre la polimerización continua. Con el reactor por lotes, además, el tiempo de polimerización puede mantenerse exactamente uniforme para todo el lote, dando como resultado un producto de especificaciones uniformes. En procesos continuos, el tiempo de polimerización depende del tiempo de residencia en el recipiente de reacción. Suponiendo que se emplee un único recipiente agitado para la suspensión continua o polimerización en emulsión y que tenga lugar una mezcla "perfecta", la distribución normalizada de la edad de salida.
Reactores industriales
El tipo de reactor utilizado para la producción a gran escala de polímeros depende de muchos factores, como el estado físico del monómero (gas, líquido o sólido), el mecanismo de polimerización (radicales libres, coordinación, iónico o condensación), el método de polimerización (a granel) , solución, suspensión, emulsión o fluidización), solubilidad del polímero en monómero, problemas de transferencia de calor, cambios de viscosidad y forma final del producto (solución, emulsión, perla o polvo).
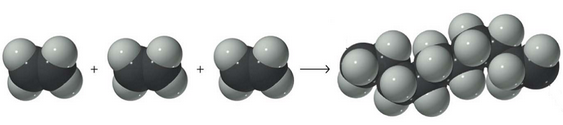
Polimerización por adición o en cadena
Pn + M ➡ Pn + 1
M representa una molécula de monómero; este paso de crecimiento de la cadena suele ser muy rápido.
Polimerización por adición de coordinación
Polimerización escalonada
La polimerización escalonada o "step" se produce mediante una reacción escalonada entre grupos funcionales de reactivos. La reacción conduce sucesivamente de monómero a dímero, trímero, tetrámero, pentámero, etc., hasta que finalmente se forma una molécula de polímero con un gran DP. Sin embargo, tenga en cuenta que las reacciones ocurren al azar entre los intermedios (por ejemplo, dímeros, trímeros, etc.) y el monómero, así como entre los propios intermedios. Por lo tanto, en cualquier etapa, el producto consta de moléculas de diferentes tamaños, lo que da un rango de pesos moleculares. El peso molecular promedio se acumula lentamente en el proceso de polimerización por etapas, y se forma un producto de alto peso molecular solo después de un tiempo de reacción suficientemente largo cuando la conversión es superior al 98%. Dado que la mayoría (aunque no todos) de los procesos de polimerización por etapas implican reacciones de policondensación (condensación repetida), los términos polimerización por etapas y polimerización por condensación se utilizan a menudo como sinónimos. Considere, por ejemplo, la síntesis de una poliamida, es decir, un polímero con amida (–CONH–) como enlace característico. Si comenzamos con, digamos, hexametilendiamina y ácido adípico como reactivos, el primer paso en la formación del polímero (nailon) es la siguiente reacción que produce una monoamida, la reacción continúa paso a paso para dar la poliamida nailon-6,6.
Polimerización radical
La polimerización radical es actualmente la técnica más utilizada para preparación a escala industrial de polímeros de vinilo. La reacción tiene lugar de acuerdo con un mecanismo de cadena en el que los centros activos, que son los portadores de la cadena cinética, son radicales libres de carbono. Un radical libre es un fragmento molecular que puede considerarse originado por la escisión homolítica de un enlace covalente, y en el que el electrón no apareado resultante no participa en ningún tipo de interacción química; En los radicales de carbono, el electrón no apareado reside en el orbital 2pz ortogonal al plano de los tres orbitales híbridos 2sp2. Cuando se estabiliza, de lo contrario la formación estaría extremadamente en desventaja, la presencia del electrón no apareado significa que estos radicales siguen siendo especies altamente reactivas y, por lo tanto, en capaz de sumarse con extrema facilidad a los múltiples enlaces de moléculas insaturadas. El proceso de polimerización por medios radicales se basa en este tipo de reacción. La polimerización radical se define como la polimerización en cadena en la que el centro activo que se propaga es un radical libre, es decir, consiste en un átomo (típicamente carbono) que tiene un orbital con un solo electrón. Los radicales de carbono (C*) son especies de alta energía que, por lo tanto, pueden reaccionar fácil y rápidamente con otras especies químicas que se encuentran en el medio de reacción. Más específicamente, pueden dar:
- a) Reacciones de adición: es decir, reaccionar con sustancias que tienen dobles enlaces, agregarles y transferir el radical a otro átomo de carbono,
---- C* + -C1 = C2- = ---- C-C1-C2* ---
Si el radical C2 * es a su vez capaz de reaccionar con -C1 = C2- la cadena se propaga.
- Reacciones de transferencia: osea reaccionar con otras especies de tipo AX, arrancando el átomo X y generando otra especie radical A *
---- C* + -AX = ---- CX + A*
La especie AX puede ser, por ejemplo, un disolvente o impurezas contenidas en ella, el monómero en sí, el polímero formado en el medio de reacción, una sustancia especialmente añadida.
- Reacciones con otras especies radicales: acoplamiento con formación de un enlace covalente estable---- C * + R * = ---- C-Ro de desproporción con la desaparición de dos radicales y la formación de dos moléculas estables;---- C * + R * = ---- C ’+‘ R---- CH2-CHX * + * XHC-CH2 ---- = ---- CH = CHX + XCH2-CH2 ----Todas estas reacciones pueden tener lugar en competencia entre sí y la velocidad relativa de las diferentes reacciones determinará las características de la estructura molecular final del polímero.
Las poliadición son reacciones en cadena en las que el polímero se obtiene simplemente de la suma de las moléculas de monómero. Como todos los átomos de monómero están incluidos en la cadena del polímero, la composición porcentual del polímero es igual a la del monómero. Las poliadición son típicas de moléculas que contienen dobles enlaces C=C, es decir, que contienen alquenos o dienos. Los principales tipos de monómeros curables por radicales son sustancias orgánicas con dobles enlaces, como por ejemplo estireno, metacrilato de metilo, cloruro de vinilo, dienos, acetato de vinilo, incluso si sustancias como viniléteres, isobuteno, propileno y a-olefinas no se polimerizan con este mecanismo. , y otros como el etileno, curan solo a alta presión (para dar LDPE). A nivel industrial, los principales tipos de polímeros producidos con polimerización radical son: PS, PVC, LDPE, PMMA, PAN, PTFE, PVDF, PVAc, poliésteres insaturados y varios copolímeros.
La polimerización radical es actualmente la técnica más utilizada para preparación a escala industrial de polímeros de vinilo:
- Polietileno de baja densidad (LDPE)
- Poli(cloruro de vinilo)
- Acetato de polivinilo)
- Poliacrilonitrilo y fibras acrílicas
- Polimetacrilato de metilo)
- poliacrilamida
- policloropreno
- Poli(vinilpiridina)
- Copolímeros de estireno-acrilonitrilo (SAN)
- politetrafluoroetileno
- Poli(fluoruro de vinilo)
- Copolímeros de acrilonitrilo-butadieno-estireno (ABS)
- Copolímeros de ácido etileno-metacrílico
- Copolímeros de caucho de estireno-butadieno (SBR)
- Caucho de nitrilo butadieno (NBR)
- Poliestireno (PS)
Polimerizaciones en etapas
Las polimerizaciones en etapa son particularmente delicadas. Para obtener polímeros comercialmente explotables de alto peso molecular, las reacciones deben limpiarse. Por reacciones limpias nos referimos a reacciones selectivas, es decir, que no dan mezclas de diferentes productos, y cuyo equilibrio puede empujarse hacia un rendimiento cuantitativo del producto deseado. La polimerización por etapas se define como un proceso que implica la reacción entre uno o más monómeros, cada uno con al menos dos grupos funcionales. La reacción inicial entre los monómeros conduce a la formación de dímeros, que a su vez reaccionan entre sí y / o con los monómeros para formar trímeros y tetrámeros. El proceso continúa con la formación de oligómeros de peso molecular que aumenta gradualmente hasta que se obtienen macromoléculas de alto peso molecular. Cada reacción entre dos monómeros/oligómeros conduce a la desaparición de dos grupos funcionales, con o sin formación de subproductos.
Polimerización de crecimiento de cadena o por etapas
En la polimerización por crecimiento de cadena los monómeros pasan a formar parte de la cadena de uno en uno. Primero se forman dímeros, después trímeros, a continuación tetrámeros, etc. La cadena se incrementa de uno en uno, monómero a monómero. En la polimerización por crecimiento en etapas (o pasos) es posible que un oligómero reaccione con otros, por ejemplo un dímero con un trímero, un tetrámero con un dímero, etc., de forma que la cadena se incrementa en más de un monómero. En la polimerización por crecimiento en etapas, las cadenas en crecimiento pueden reaccionar entre sí para formar cadenas aún más largas. Esto es aplicable a cadenas de todos los tamaños. En una polimerización por crecimiento de cadena sólo los monómeros pueden reaccionar con cadenas en crecimiento.
Polimerización por condensación
Los polímeros de condensación muestran unidades repetitivas unidas entre sí por unidades funcionales como éster, amida, carbonato, uretano, etc. La polimerización se realiza por etapas. El tamaño de la macromolécula aumenta lentamente con el siguiente mecanismo:
- monómero + monómero = dímero
- dímero + monómero = trímero
- dímero + dímero = tetrámero
- trímetro + trímetro = hexamer
- trímetro + dímero = pentámero
- trímetro + monómero = tetrameter
- etcétera
En la práctica, dos especies moleculares (monómeros) pueden reaccionar entre sí durante la polimerización y dar lugar a muchas cadenas (macromoléculas) cuyos grupos terminales pueden reaccionar aún más entre sí hasta que tengan un polímero lineal con un alto peso molecular ( es decir, con una gran cantidad de unidades repetitivas). Cualquier proceso de condensación, lo que resulta en la formación de polímeros, se conoce como polimerización por condensación. Las policondensaciones son reacciones que no necesitan iniciarse, pero los monómeros pueden unirse con la expulsión de moléculas pequeñas, generalmente agua, ácido clorhídrico o metanol. El monómero debe tener grupos funcionales en los extremos, que pueden reaccionar juntos para continuar la polimerización. Por ejemplo, si los extremos de unión de dos moléculas tienen un grupo -OH y un grupo -COOH, una molécula de agua será liberado y forma un enlace éster. El poliéster es un ejemplo de un polímero de condensación así.
Polimerizaciones iónicas
Las polimerizaciones iónicas siguen los mismos pasos básicos que las polimerizaciones de crecimiento de cadena de radicales libres (es decir, iniciación, propagación y terminación); sin embargo, existen algunas diferencias importantes, como se discutirá en las siguientes secciones. Se puede formar un sitio iónico carbanión (-) o carbonio (+) en el proceso de iniciación. La polimerización de monómeros vinílicos con un grupo atractor de electrones puede proceder por una ruta aniónica, mientras que los monómeros con un grupo donante de electrones (por ejemplo, metilo) pueden polimerizar mediante un mecanismo catiónico.
Copolimerización iónica
Como en el caso de la copolimerización por radicales libres, se pueden copolimerizar dos o más monómeros mediante un mecanismo iónico. Por ejemplo, el elastómero comercial de poliisobutileno (caucho butílico) es un copolímero obtenido por copolimerización catiónica de isobutileno con 0,5% a 2% de isopreno. Otro ejemplo importante de una copolimerización iónica es el copolímero tribloque SBS, que tiene un bloque central de butadieno con un bloque de estireno en cada extremo de la cadena. Este copolímero tribloque es un ejemplo de elastómero termoplástico que es elástico a temperatura ambiente pero que puede moldearse como otros termoplásticos a temperaturas más altas. Puede prepararse añadiendo monómero de estireno a una cadena de butadieno activo que tiene sitios aniónicos en ambos extremos (es decir, un dianión de butadieno). El dianión se obtiene usando un iniciador de transferencia de electrones como el naftalenuro de sodio preparado haciendo reaccionar el naftaleno con sodio. El anión del radical naftaleno puede transferir un electrón al monómero (butadieno) para formar un anión del radical monómero. Dos de estos aniones radicales pueden combinarse para dar un dímero con sitios de carbanión en extremos opuestos. Los sitios de carbanión están disponibles para la adición de más monómeros de butadieno para obtener un grado predeterminado de polimerización. En ese momento, se puede añadir monómero de estireno para formar el copolímero tribloque SBS.
Polimerización catiónica
La polimerización catiónica es un proceso en el que las especies que propagan la cadena cinética, es decir, los centros activos de la reacción de polimerización, tienen una naturaleza electrofílica (ácidos de Lewis), consisten en carbohidratos verdaderos o solo en especies de pseudocarbocatión. El carbocatión es un ion de carbono positivo compuesto por un átomo de carbono hibridado 2sp2 en el que el orbital orbital atómico, no híbrido (normal al plano híbrido), está vacante. La reactividad y, en consecuencia, la vida del ion dependen de la naturaleza y del número de sustituyentes presentes en él. Grupos capaces de dar densidad electrónica al átomo de carbono (efecto inductivo de las especies donantes de electrones) o sustituyentes capaces de eliminar parte del la carga positiva presente en él deslocalizándola en un área más amplia (mesómero o efecto hiperconjugativo y resonancia) puede estabilizar este ion extendiendo su vida y, por lo tanto, lo hace portador adecuado de una cadena cinética que alcanza la formación de alto polímero. La polimerización radical es actualmente la técnica más utilizada para preparación a escala industrial de polímeros :
- Poliisobutileno (PIB)
- Caucho de butilo
- Poliacetal
Polimerizaciones aniónicas
Las polimerizaciones aniónicas entran en la clase de poliaducciones controladas en cadena y se caracterizan por tener un átomo de carbono con una carga como centro activo. negativo parcial o total, asociado con un contraataque. El requisito fundamental que un monómero debe poder satisfacer para ser polimerizado por anión es poder generar una especie carbaniónica suficientemente estabilizada a través de efectos inductivos y mesoméricos. Los monómeros de vinilo y dieno son las especies que normalmente se polimerizan con este tipo de técnica. La polimerización radical es actualmente la técnica más utilizada para preparación a escala industrial de polímeros :
- Elastómeros de olefina termoplástica (copolímeros de butadieno, isopreno y estireno)
- Poliacetal
Polimerización interfacial
Este método es limitado a un pequeño número de polimerizaciones en etapas, debido a las condiciones de reacción necesarias. Es un método de polimerización que puede usarse cuando la reacción de polimerización involucra la reacción de dos monómeros A y B, cada uno de los cuales puede reaccionar con el otro pero no consigo mismo (es decir, A puede reaccionar con B y viceversa). , pero A no puede reaccionar con A y B con B). Es un método de polimerización que puede usarse, por ejemplo, para producir policarbonato de bisfenol A y poliamidas de tipo AB. En el proceso de polimerización interfacial, los dos monómeros se disuelven en dos solventes diferentes que no son miscibles entre sí (A disuelto en el solvente A 'y B disuelto en el solvente B'), uno de los cuales generalmente es agua. Dado que los dos monómeros están en diferentes medios, su reacción solo puede tener lugar en la interfaz donde los dos monómeros pueden entrar en contacto. Por lo tanto, el polímero se forma como una película en la interfaz. En general, para aumentar la velocidad del proceso, se opera bajo agitación fuerte y en presencia de emulsionantes de tal manera que los dos líquidos se dispersan entre sí en forma de pequeñas gotas (con una alta relación S / V). Generalmente los monómeros utilizados se caracterizan por altas velocidades de reacción.
También en este caso las principales ventajas son:
- posibilidad de polimerización incluso a baja temperatura
- baja viscosidad del medio de reacción
- fácil eliminación del calor de reacción
- el polímero no necesita ser soluble en uno de los dos solventes
Los principales problemas pueden resumirse en los siguientes puntos:
- los polímeros obtenidos tienen baja pureza debido a la dificultad de eliminar los aditivos e impurezas presentes en solventes
- es necesario recuperar solventes (generalmente caros)
- el método es aplicable solo a algunos tipos de monómeros
- dificultad para recuperar el polímero
Beneficios:
no se requiere una pureza de reactivo excesiva una relación estrictamente estequiométrica de monómeros no es necesaria altas velocidades de reacción (pocos minutos frente a horas de polimerización en masa) baja T de reacción facilidad de eliminación de productos de reacción.
Desventajas:
es necesario recuperar el solvente orgánico necesita manejar grandes volúmenes de líquidos con monómeros muy reactivos, el rendimiento puede ser bajo debido a fenómenos de hidrólisis.
Procesos en suspensión con reactores de agitación continua
Durante años, se han desarrollado varias modalidades de procesos en suspensión utilizando catalizadores del catalizador en el producto. Pero, gracias a la mayor actividad de los catalizadores, hace algunos años que es posible prescindir de esta fase. Las plantas modernas con procesos en «slurry» de mezcla perfecta suelen utilizar hexano como diluyente. Algunas instalaciones antiguas utilizan hidrocarburos más pesados, que suelen requerir una separación (stripping) con vapor para eliminar el diluyente del polímero. La temperatura de reacción varía entre 80 y 90°C, y se emplea hexano como diluyente. El suministro principal del reactor es diluyente reciclado. El suministro de flujos de etileno y comonómero se introducen mediante lechos de purificación para eliminar las trazas de venenos para el catalizador. A continuación, se añade al reactor una cantidad controlada de monómero de etileno, un comonómero e hidrógeno, así como una suspensión de una mezcla de catalizador/cocatalizador (alquil aluminio). En el reactor de parada, el etileno disuelto ya se ha consumido casi completamente. El etileno restante se puede recuperar y volver a enviar a un fraccionador cercano o utilizarlo como gas combustible. La concentración de polímero en el «slurry» es un parámetro importante del proceso. Si la concentración es alta, se puede obtener un índice de producción elevado para un volumen de reactor determinado, pero, al mismo tiempo, dificulta la transferencia de calor a la camisa refrigerante del reactor y el funcionamiento del agitador en el reactor. La concentración máxima de «slurry» de polímero depende de muchos factores, como el tipo de disolvente o el tamaño y la forma del granulado, y, básicamente, la densidad del agregado de las partículas de polímero. La concentración de «slurry» de polímero puede variar entre 15% y 45% en peso, aunque se suele situar entre un 30% y un 35%. Después de abandonar el reactor, el «slurry» de polímero pasa a un proceso de centrifugado que elimina la mayor parte del disolvente. El disolvente separado se vuelve a introducir en el reactor. En un secador de lecho fluidizado, el polímero se seca en un flujo de nitrógeno caliente y se libera del disolvente restante. El disolvente se puede condensar del gas de salida del secador de lecho fluidizado para reciclarlo posteriormente. A continuación, se extrae un pequeño flujo de purga, que contiene principalmente nitrógeno, del flujo de reciclaje del lecho fluidizado para controlar la acumulación de material inerte ligero y venenos para el catalizador. Por último, este gas de purga se suele enviar a un quemador. Los productos más habituales que se producen con procesos de suspensión son: Cloruro de polivinilo, polimetilmetacrilato, poliestireno (HIPS y EPS), politetrafluoretileno, y poliolefinas en forma de «slurry» en fracciones de aceite mineral.
Polimerizaciones de metalocenos
En 1980, Sinn y Kaminsky informaron de un avance significativo en la polimerización homogénea estereorregular de etileno, -olefinas, incluido el propileno, y varios otros monómeros comercialmente importantes, incluidos el estireno y el metacrilato de metilo. Este nuevo tipo de polimerización por coordinación utiliza catalizadores de metaloceno. Se han utilizado varios metales de transición diferentes (típicamente del grupo IVb) en la preparación de catalizadores de metaloceno, incluidos circonio (es decir, circonoceno), titanio (es decir, titanoceno) y hafnio (es decir, hafnoceno). El orden de actividad del metaloceno es generalmente Zr> Hf> Ti. Los metalocenos se pueden utilizar para obtener polímeros extremadamente uniformes con una distribución de peso molecular estrecha. El etileno fue la primera olefina que se polimerizó utilizando catalizadores de metaloceno. Los metalocenos también se pueden usar para copolimerizar etileno con propileno, buteno, hexeno y octeno. En comparación con los catalizadores Z – N, los metalocenos son más caros pero pueden ser más productivos en términos de la cantidad de polímero producido por cantidad de catalizador. Los polímeros de metaloceno comerciales, con propiedades que van desde el cristalino hasta el elastomérico, se produjeron por primera vez en 1991 y han estado capturando rápidamente el mercado de las poliolefinas. Las propiedades mejoradas de algunos polímeros catalizados por metaloceno abren nuevas oportunidades para los termoplásticos básicos tradicionales. Por ejemplo, la claridad óptica superior, la ductilidad a baja temperatura y cantidades reducidas de impurezas (por ejemplo, residuos de metales del catalizador) hacen que los polímeros de metaloceno sean adecuados para muchas aplicaciones biomédicas. Casi el 100% de polipropileno sindiotáctico (s-PP) y poliestireno sindiotáctico (s-PS) se han producido por primera vez a escala comercial usando polimerizaciones de metaloceno. Los catalizadores de metaloceno se utilizan con un cocatalizador, típicamente metilaluminoxano (MAO), una mezcla compleja de oligómeros de óxido de metilaluminio (–CH2AlO–). La MAO se forma mediante la hidrólisis controlada de trimetilaluminio. La actividad catalítica de los catalizadores de metaloceno es directamente proporcional al grado de oligomerización del aluminoxano. Se pueden usar otros cocatalizadores de ácido de Lewis como tetrafenilboratos para polimerizar monómeros que contienen grupos sustituyentes, como metacrilato de metilo. La mayoría de los reactores para los reactores de polimerización Ziegler – Natta están diseñados para su uso con catálisis heterogénea. Para utilizar las instalaciones existentes, los metalocenos pueden apoyarse en varios óxidos inorgánicos como SiO2 (gel de sílice), Al2O2 y MgCl2 con o sin MAO. Por ejemplo, los metalocenos con soporte de sílice se pueden utilizar para obtener polietileno lineal de baja densidad (LLDPE) mediante el proceso de fase gaseosa. Los catalizadores de metaloceno más utilizados consisten en dos ligandos de ciclopentadienilo (doblados) (Cp2MX2). Son posibles muchas otras estructuras de metaloceno, incluido un solo anillo de ciclopentadienilo utilizado en la polimerización de s-PS. El anillo ciclopentadienilo de un metaloceno está unido individualmente al átomo metálico central mediante un enlace.
Copolimerizaciones
Modificaciones de los plásticos
Los consumidores de plásticos tienen exigencias muy concretas y complejas.
Para cubrir y satisfacer toda esta demanda, los fabricantes y transformadores disponen
de varios caminos, como son la modificación química de los polímeros, la modificación
física y la modificación con aditivos.
La modificación de los plásticos por vía química puede ser de varias maneras:
- mediante el control de las reacciones de síntesis; es decir, gobernando a
voluntad los parámetros más importantes de las macromoléculas como son la longitud
de cadena, las distribución de pesos molecualres, el grado de ramificación y la
cristalinidad
- mediante copolimerización y copolimerizaión de injerto, en la que según la
velocidad de polimerización del monómero, la disposición de las unidades de
monómero dentro del polímero será fortuíta, es decir irregular, o alternante.
(i) Plásticos con cargas de relleno. A los plásticos se les agregan con
frecuencia cargas de relleno, en cantidades que, en ocasiones, superan el
50% del material. Son insolubles en el polímeros, no volátiles y no se
alteran en el intervalo de temperaturas de uso. Las cargas de relleno se
usan o bien para lograr propiedades especiales o bien para abaratar el
producto.
(ii) Plásticos reforzados. Si se pretende mejorar sobre todo las
característica mecánicas (resistencia, rigidez, estabilidad al impacto), se
recurre a materiales de refuerzo, que normalmente son fibras, como fibra
de vidrio, tejidos o fieltros de carbono y celulosa. El material más
conocido son las “resinas de poliéster insaturado reforzadas con fibra de
vidrio” (UP-GF).
(iii) Plásticos plastificados. Para lograr un plástico blando como la goma,
se le puede agregar plastificantes que, por lo general, son líquidos. El
PVC es el caso más típico de termoplástico duro y rígido que, con los
plastificantes, se convierte en blando y flexible.
(iv) Plásticos espumados. Estos plásticos presentan estructura porosa,
celular. Sus celdillas están llenas de aire o de otro gas, por lo que tienen
una densidad muy inferior a la de los plásticos no espumados obtenidos
con el mismo polímero. Este tipo de plásticos será tratado con más
profundidad en sucesivos apartados.
Polimerización por precipitación
La polimerización por precipitación, también conocida como polimerización en suspensión, implica sistemas en solución en los que el monómero es soluble pero el polímero no. Probablemente sea el proceso más importante para la polimerización por coordinación de olefinas. El proceso implica, esencialmente, una etapa de preparación del catalizador y polimerización a presiones normalmente inferiores a 50 atm y bajas temperaturas (menos de 100°C). El polímero resultante, que se precipita como flóculos finos, forma una suspensión que consta de aproximadamente un 20% de polímero suspendido en el hidrocarburo líquido empleado como disolvente. El polímero se recupera eliminando el disolvente, lavando el catalizador y, si es necesario, extrayendo cualquier componente polimérico indeseable. Finalmente, el polímero se mezcla con aditivos y estabilizadores y luego se granula. La suspensión de los flóculos de polímero en el solvente produce un sistema físico de baja viscosidad que es fácil de remover. Sin embargo, pueden surgir problemas debido a la sedimentación del polímero y la formación de depósitos en las paredes del agitador y del reactor. La mayoría de los catalizadores industriales de metales de transición son insolubles y, en consecuencia, la polimerización se produce en un sistema multifásico y puede controlarse mediante transferencia de masa. Por tanto, el tipo de catalizador empleado ejerce una mayor influencia sobre los parámetros y la geometría del reactor.
Se han sintetizado diversos polímeros en CO2 mediante polimerización por precipitación de radicales libres. En los primeros estudios, se investigó la polimerización por radicales libres de etileno en CO2 mediante radiación gamma o iniciación AIBN. Otras patentes describen la polimerización de varios monómeros de hidrocarburos vinílicos en líquido y scCO2. Se han elaborado homopolímeros de cloruro de vinilo, acrilonitrilo, ácido acrílico, acetato de vinilo, 2-hidroxietilacrilato y algunas N-vinilcarboxamidas, así como copolímeros aleatorios de PS/PMMA y PVC/PVAc. Las reacciones de polimerización dieron como resultado polímeros con rendimientos gravimétricos que variaban del 15 al 97% y pesos moleculares promedio de viscosidad (Mv) que variaban de 1.2 x 104 a 1.6 x 106 g/mol dependiendo del monómero y las condiciones de reacción utilizadas. Más recientemente, se ha logrado la polimerización por radicales libres de poli (ácido acrílico) de alto peso molecular (Mn=1,5 × 105 g/mol) en scCO2 a pesar de que el polímero precipita de la solución a pesos moleculares superiores a 1000 g/mol. El peso molecular del polímero podría controlarse añadiendo etilmercaptano como agente de transferencia de cadena o manipulando los parámetros de temperatura y presión para la reacción. También se han sintetizado fluoropolímeros de alto rendimiento en CO2 mediante polimerización por precipitación de radicales libres. Los homopolímeros y copolímeros de tetrafluoroetileno (TFE) han generado un interés particular, ya que se descubrió que el TFE se puede manipular de manera más segura como una mezcla con CO2. En 1995, se informaron homopolimerizaciones de TFE y copolimerizaciones de TFE con hexafluoropropileno (HFP) o perfluoropropil vinil éter (PPVE) que produjeron polímeros de alto peso molecular (> 106 g / mol) con buen rendimiento. La copolimerización de monómeros de TFE y perfluoroalquil vinil éter en CO2 se produce prácticamente sin escisión β, lo que implica que la propagación de radicales terminales que contienen vinil éter es más favorable en CO2 que en disolventes tradicionales. Se ha desarrollado un sistema para la polimerización continua de varios monómeros en scCO2. La polimerización por precipitación continua de fluoruro de vinilideno y ácido acrílico puede ocurrir en un reactor de tanque agitado continuo (CSTR) intensamente agitado. Las velocidades de polimerización del fluoruro de vinilideno en el CSTR son significativamente más altas que las velocidades medias de polimerización por lotes, en condiciones similares. El CO2 también se ha empleado como disolvente en polimerizaciones por precipitación de polímeros reticulados, utilizando altos niveles de reticulante de divinilbenceno. Las reacciones iniciadas por AIBN se realizaron a 65°C durante 12 h en 31 MPa (310 bar) de CO2 y produjeron partículas esféricas sin el uso de tensioactivos. También se investigaron monómeros multifuncionales como trimetacrilato de trimetilolpropano y dimetacrilato de etilenglicol. Estas reacciones produjeron monolitos poliméricos bien definidos con diámetros de poro que oscilaban entre 20 y 8000 nm (consulte la sección "Síntesis de polímeros porosos"). Una clara ventaja del uso de CO2 en cada una de estas reacciones de precipitación es que los productos se aíslan fácilmente de los recipientes de reacción despresurizados como materiales secos, sin disolventes.
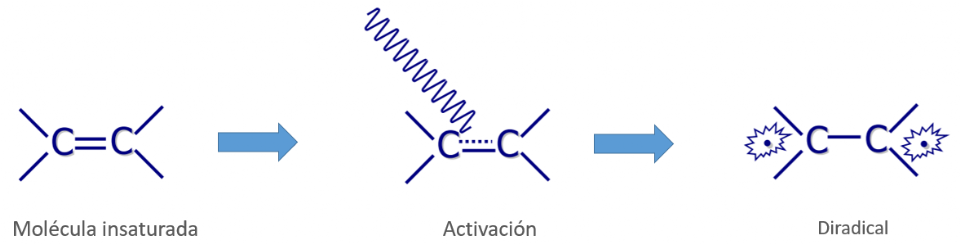