Slush Molding
Procesos > ► Otros procesos
Slush molding
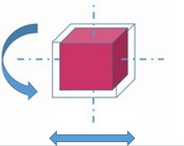
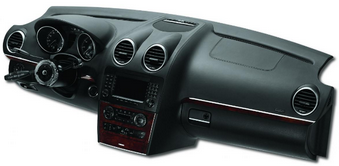
Beneficios de los sistemas de moldeo rotativo
- Larga vida útil de los moldes
- Ahorro de costes en la adquisición de nuevos moldes
- Marco de gran tamaño
- Posibilidad de utilizar moldes dobles o múltiples
- Alta flexibilidad de los moldes en el sistema
- Posibilidad de uso simultáneo de diferentes moldes en circulación
- Precisión de alta en todo el espesor de piel con buen molde
- El tamaño del marco del molde puede ser grande
- El sistema calienta y enfría muy suavemente con aire
Requirements for interior parts:
- Háptica suave similar al cuero
- Flexibilidad independiente de alta temperatura
- Resistencia al rayado
- Requisito de baja temperatura <-40°C
- Dureza y háptica ajustables
- Brillo ajustable
- Buenas propiedades de choque
- Buena resistencia a la intemperie
- Resistencia química
- Bajas emisiones
- Buena adherencia
- Libertad en el diseño
- Reciclable
Tecnologías de vanguardia para el tacto suave
Los tres procesos principales que se utilizan para fabricar pieles blandas para interiores son:
- Moldeo de aguanieve
- Termoformado positivo y negativo (lámina)
- Poliuretano aromático rociado (PU) - En revestimiento de molde
El moldeado con aguanieve es el proceso preferido. Brinda a los fabricantes una mayor libertad en el diseño de componentes y se utiliza para producir una variedad de componentes para el interior de automóviles, tales como: Paneles de instrumentos Consolas de molduras de puertas Cubiertas de bolsas de aire Protectores de rodilla.
Termoformado positivo y negativo
El termoformado es un proceso de conformación de una lámina termoplástica plana que incluye dos etapas: ablandamiento de la lámina mediante calentamiento, seguido de formación en la cavidad del molde. Existen tres métodos de termoformado, que se diferencian en la técnica utilizada para la etapa de conformado:
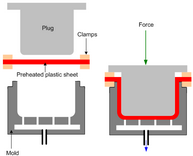
- Termoformado al vacío
- Termoformado a presión
- Termoformado Mecánico
A diferencia de otros procesos como la inyección, el soplado y el rotomoldeado, el termoformado parte de una lámina rígida de espesor uniforme realizada por el proceso de extrusión, y permite realizar pequeñas producciones por su bajo costo en matricería llegando a ser rentable en altas producciones.
Poliuretano aromático rociado (PU) - En revestimiento de molde
Utilizaron un sustrato de espuma de uretano alifático con una laca a base de disolvente o uretano de dos componentes. Con el advenimiento de elastómeros aromáticos de bajo costo a fines de la década de 1990, se ha puesto un mayor énfasis en la conversión de piezas de automóviles interiores de PVC a aplicaciones en molde, lo que aumenta el rendimiento y mejora la apariencia. Actualmente, los siguientes componentes se están preparando mediante procesos en molde: paneles de instrumentos, paneles de puertas, volantes, fundas de airbag, apoyabrazos, manijas de asistencia, reposacabezas y fundas de asientos. Los procesos en molde utilizados son elastómero de poliuretano pulverizable, elastómero de poliuretano inyectado y espuma de poliuretano. La mayoría de estas aplicaciones utilizan recubrimientos en molde a base de agua. El proceso en el molde permite un tiempo de procesamiento más rápido y ocupa menos espacio que una aplicación posterior a la pintura. La mayoría de las aplicaciones posteriores a la pintura requieren entre 6 y 8 minutos para procesarse y requieren equipos de lavado a presión, líneas de rociado y hornos.
Sinterizado rotacional de polímeros
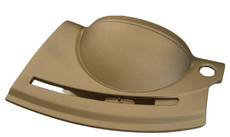
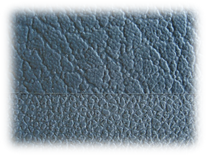
